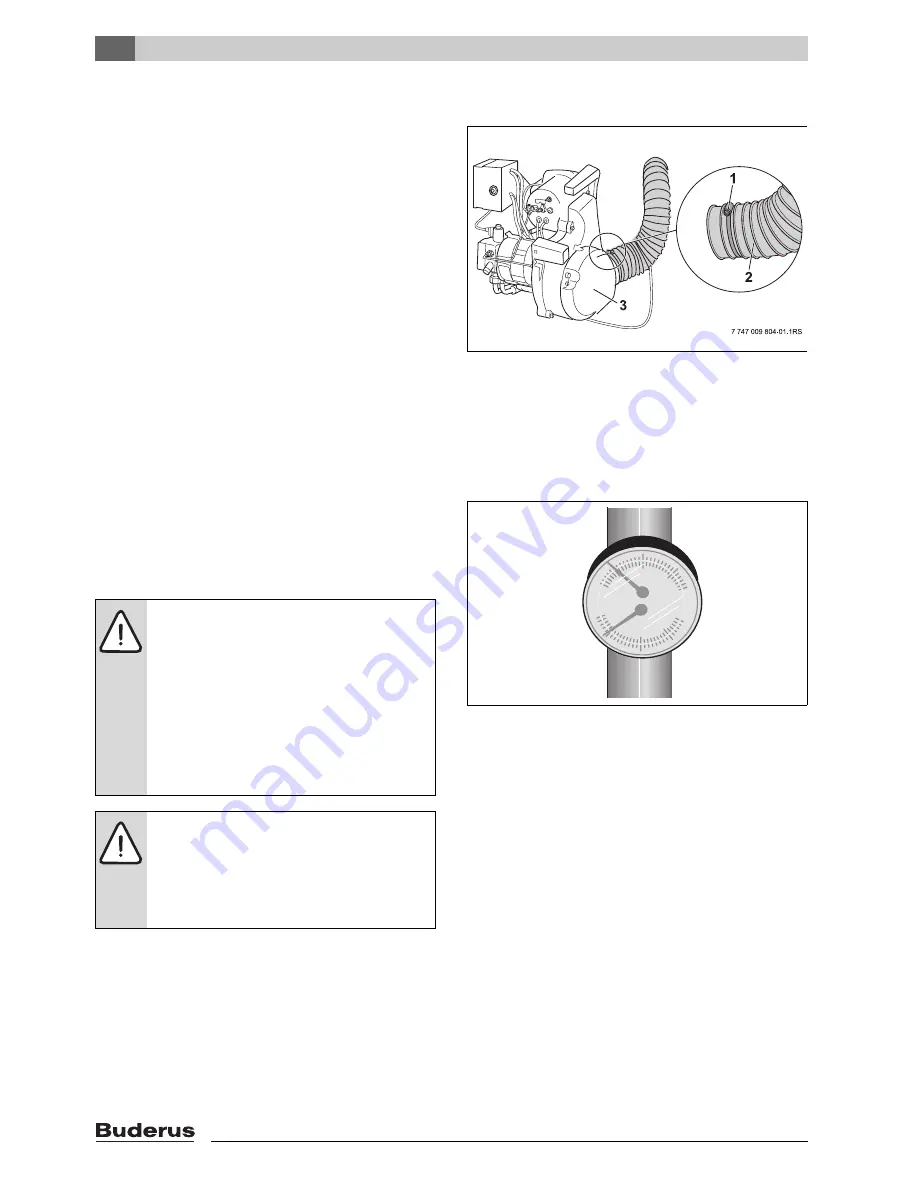
8
Heating system inspection
Logano GB125 BE US/CA - Subject to technical modifications.
44
8.6
Checking the air supply hose
B
Disconnect the corrugated hose [2] from the burner
intake silencer [3] by undoing the special hose clip [1]
and check for dirt.
B
If dirty, clean the corrugated hose [2] with a vacuum
cleaner.
Fig. 48 Inspecting the corrugated hose
1
Special hose clip
2
Corrugated hose (air supply for combustion)
3
Intake silencer
8.7
Check heating system operating pressure
The system pressure for closed systems must be
15 – 30 psi (1.0 – 2.1 bar).
B
Checking the operating pressure
B
If the pressure gauge shows less than 15 psi, the
operating pressure is too low. Add water to the system.
Fig. 49 Pressure/temperature gauge for showing
operating pressure and supply temperature
CAUTION:
Risk of system damage due to
frequent topping up!
If you have to top up the heating water
frequently, the heating system may suffer
damage from corrosion or scaling,
depending on the water quality.
B
Ensure that your heating system is bled
properly.
B
Check the heating system for leaks and
proper operation of the expansion vessel.
WARNING:
Health risk from contaminated
domestic water!
Observe all national standards and
regulations regarding prevention of domestic
water contamination (e.g. by water from
heating systems).
7 747 019 141-17.1RS