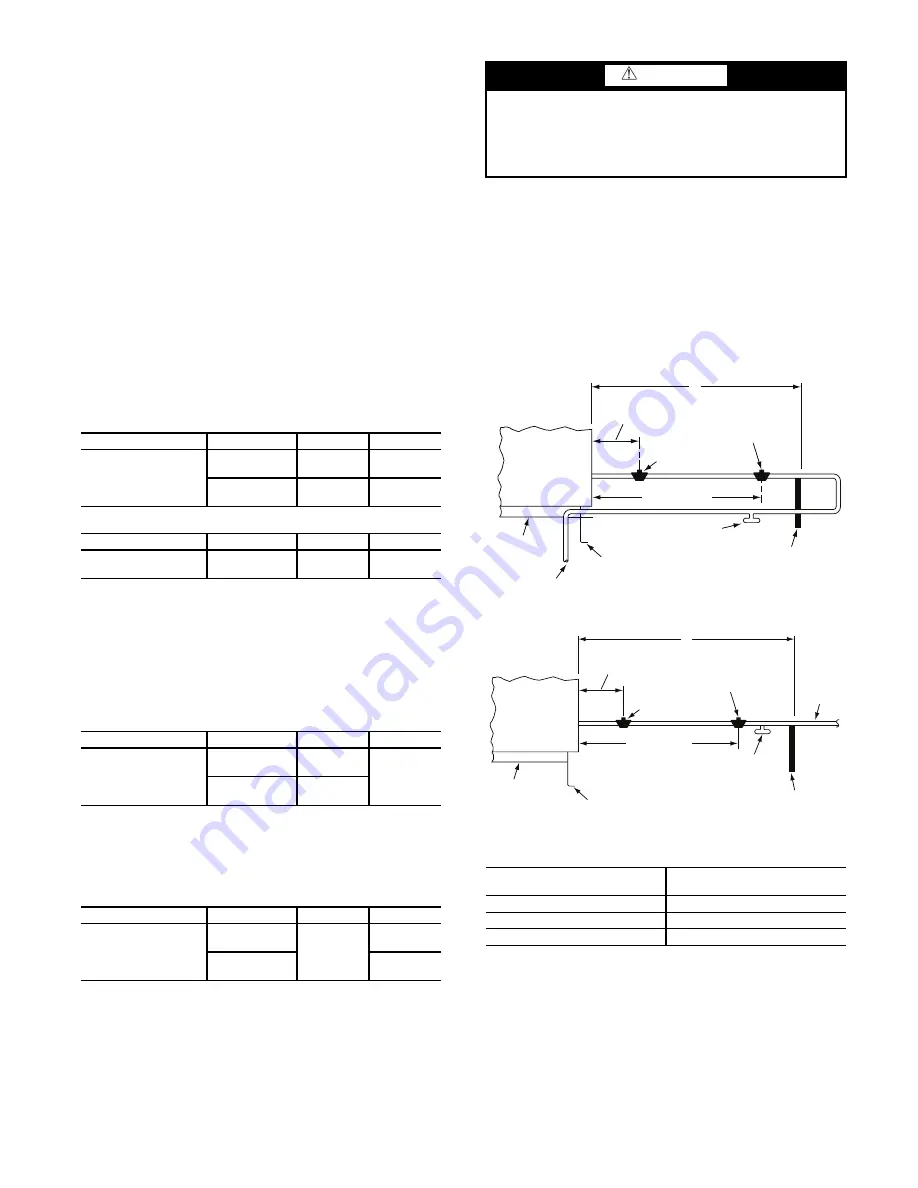
21
Step 10 — Install Gas Piping —
Installation of the gas pip-
ing must be accordance with local building codes and with appli-
cable national codes. In U.S.A., refer to NFPA 54/ANSI Z223.1
National Fuel Gas Code (NFGC). In Canada, installation must be
accordance with the CAN/CSA B149.1 and CAN/CSA B149.2
installation codes for gas burning appliances. This unit is factory
equipped for use with Natural Gas fuel at elevations up to 2000 ft
(610 m) above sea level. Unit may be field converted for operation
at elevations above 2000 ft (610 m) and/or for use with liquefied
petroleum fuel. See accessory kit installation instructions regard-
ing these accessories.
NOTE: Furnace gas input rate on rating plate is for installation
up to 2000 ft (610 m) above sea level. In U.S.A. the input rat-
ing for altitudes above 2000 ft (610 m) must be derated by 4%
for each 1000 ft (305 m) above sea level.
For natural gas applications, gas pressure at unit gas connection
must not be less than 4 in. wg (996 Pa) or greater than 13 in. wg
(3240 Pa) while the unit is operating for size 08 to 14 and 5 in. wg
(996 Pa) or greater than 13 in. wg (3240 Pa) while the unit is oper-
ating for size 16 (see Table 3). For liquefied petroleum applica-
tions, the gas pressure must not be less than 11 in. wg (2740 Pa) or
greater than 13.0 in. wg (3240 Pa) at the unit connection, see
Table 4.
Table 3 — Natural Gas Supply Line Pressure Ranges
Table 4 — Liquid Propane Supply Line Pressure Ranges
The gas supply pipe enters the unit at the burner access pan-
el on the front side of the unit, through the long slot at the bot-
tom of the access panel. The gas connection to the unit is made
to the
1
/
2
-in. FPT gas inlet port on the unit gas valve for sizes
08-14 and
3
/
4
-in. FPT gas inlet port on the unit gas valve for
size 16, see Table 5.
Manifold pressure is factory-adjusted for NG fuel use. Adjust
as required to obtain best flame characteristics.
Table 5 — Natural Gas Manifold Pressure Ranges
Manifold pressure for LP fuel use must be adjusted to specified
range, see Table 6. Follow instructions in the accessory kit to
make initial readjustment.
Table 6 — Liquid Propane Manifold Pressure Ranges
Install a gas supply line that runs to the unit heating section.
Refer to the NFPA 54/NFGC or equivalent code for gas pipe siz-
ing data. Do not use a pipe size smaller than
1
/
2
-in. Size the gas
supply line to allow for a maximum pressure drop of 0.5-in. wg
(124 Pa) between gas regulator source and unit gas valve connec-
tion when unit is operating at high-fire flow rate.
The gas supply line can approach the unit in three ways: hori-
zontally from outside the unit (across the roof), thru-curb/under
unit basepan (accessory kit required) or through unit basepan (fac-
tory-option or accessory kit required). Consult accessory kit instal-
lation instructions for details on these installation methods.
Observe clearance to gas line components per Fig. 25.
Fig. 25 — Gas Piping Guide (with Accessory Thru-the-
Curb Service Connections)
UNIT MODEL
UNIT SIZE
MIN.
MAX.
580J
08, 09, 12, 14
4.0 in. wg
(996 Pa)
13.0 in. wg
(3240 Pa)
16
5.0 in. wg
(1250 Pa)
13.0 in. wg
(3240 Pa)
UNIT MODEL
UNIT SIZE
MIN.
MAX.
580J
08, 09, 12, 14,
16
11.0 in. wg
(2740 Pa)
13.0 in. wg
(3240 Pa)
UNIT MODEL
UNIT SIZE
HIGH FIRE LOW FIRE*
580J
08, 09, 12, 14
3.5 in. wg
(872 Pa)
2.0 in. wg
(498 Pa)
16
3.0 in. wg
(747 Pa)
*LOW FIRE, 1.7 in. wg (423 Pa), applies to the following units only:
580J*08D/F and 580J*09D.
UNIT MODEL
UNIT SIZE
HIGH FIRE LOW FIRE*
580J
08, 09, 12, 14
10.0 in. wg
(2490 Pa)
5.7 in. wg
(1420 Pa)
16
6.6 in. wg
(1644 Pa)
*LOW FIRE, 5.0 in. wg (1420 Pa), applies to the following units
only: 580J*08D/F and 580J*09D.
CAUTION
Failure to follow this caution may result in damage to
equipment.
When connecting the gas line to the unit gas valve, the
installer MUST use a backup wrench to prevent damage to
the valve.
X
BASE UNIT
BASE RAIL
ROOF
CURB
9” MINIMUM CLEARANCE
FOR PANEL REMOVAL
MANUAL GAS
SHUTOFF VALVE
*
GAS
REGULATOR
*
48” MINIMUM
DRIP LEG
PER NFGC
*
FIELD-FABRICATED
SUPPORT
*
FROM
GAS
METER
* Field supplied.
STEEL PIPE NOMINAL
DIAMETER (in.)
SPACING OF SUPPORTS X
DIMENSION (ft)
1
/
2
6
3
/
4
or 1
8
1
1
/
4
or larger
10
X
BASE UNIT
BASE RAIL
ROOF
CURB
9” MINIMUM CLEARANCE
FOR PANEL REMOVAL
MANUAL GAS
SHUTOFF VALVE
*
GAS
REGULATOR
*
48” MINIMUM
DRIP LEG
PER NFGC
*
FIELD-
FABRICATED
SUPPORT
FROM
GAS
METER
SIZES 08-14
SIZE 16
Содержание 580J*16D Series
Страница 4: ...4 Fig 2 Unit Dimensional Drawing Sizes 08 09 and 12 ...
Страница 5: ...5 Fig 2 Unit Dimensional Drawing Sizes 08 09 and 12 cont ...
Страница 6: ...6 Fig 3 Unit Dimensional Drawing Size 14 ...
Страница 7: ...7 Fig 3 Unit Dimensional Drawing Size 14 cont ...
Страница 8: ...8 Fig 4 Unit Dimensional Drawing Size 16 ...
Страница 9: ...9 Fig 4 Unit Dimensional Drawing Size 16 cont ...
Страница 15: ...15 Fig 9 580J 16 Roof Curb Details ...
Страница 32: ...32 Fig 58 580J 08 14 Typical Perfect Humidity Dehumidification System Humidistat Wiring ...
Страница 33: ...33 Fig 59 580J 16 Typical Perfect Humidity Dehumidification System Humidistat Wiring ...
Страница 48: ...48 Fig 67 580J 08 12N P Typical RTU Open System Control Wiring Diagram ...
Страница 49: ...49 Fig 68 580J 08 14 Typical RTU Open System Control Wiring Diagram ...
Страница 50: ...50 Fig 69 580J 16 Typical RTU Open System Control Wiring Diagram ...
Страница 51: ...51 Fig 70 580J 8 14 Typical RTU Open System Control Wiring Diagram with Perfect Humidity System ...
Страница 52: ...52 Fig 71 580J 16 Typical RTU Open System Control Wiring Diagram with Perfect Humidity System ...