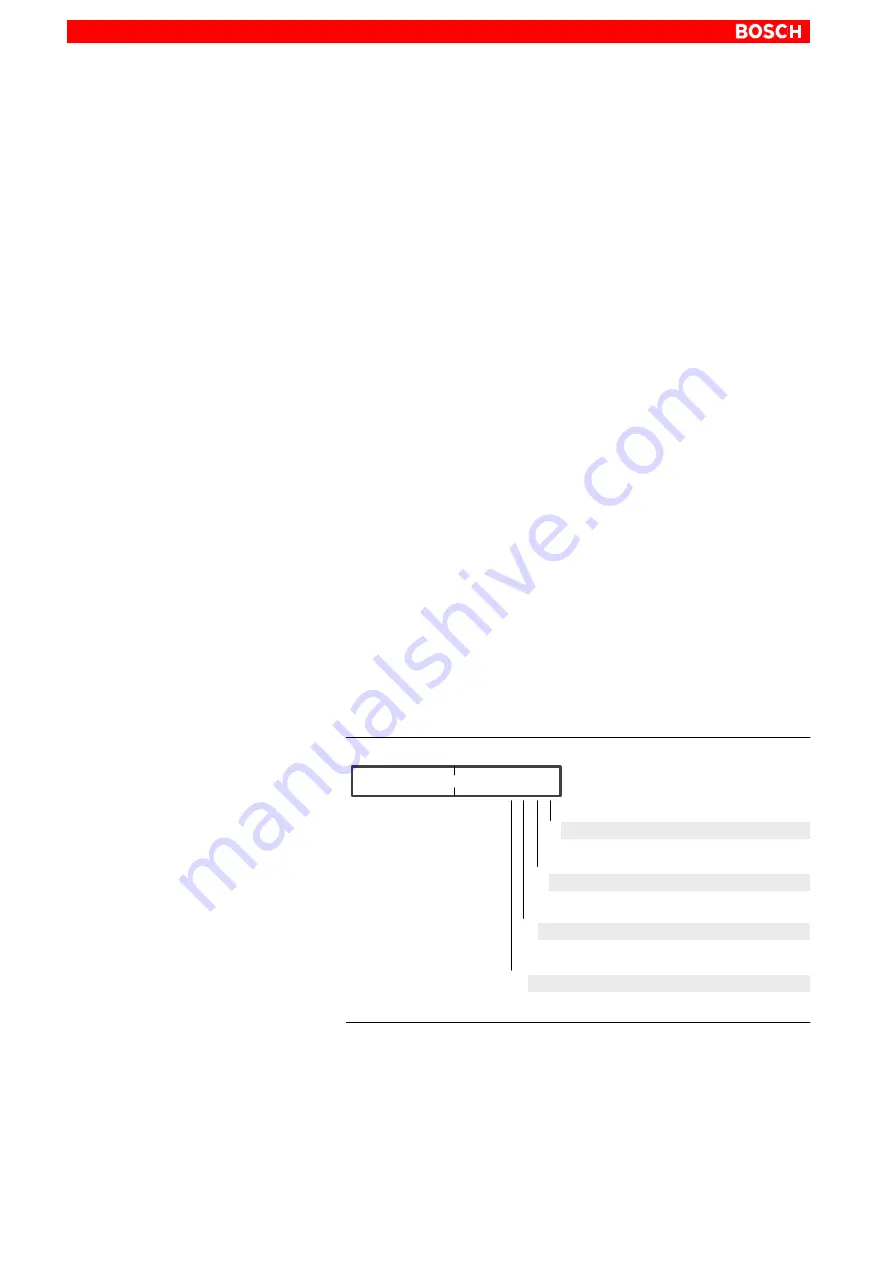
PROFIBUS-DP interface
3–2
1070 066 091-102 (01.08) GB
3.2
Possible modes of the drive
Inverters equipped with PROFIBUS-DP offer the following modes:
D
”Motion-controlled mode”,
D
”Interpolation in drive”,
D
”Velocity control”, or
D
”Velocity control with actual value feedback”
3.2.1
Motion-controlled mode (MC mode)
Features:
D
Positioning mode with a maximum of 32 motion blocks stored in the drive.
Shortest cycle time of the position setpoint generator: 2 ms
D
Absolute as well as incremental position inputs are possible
D
Path-optimized starting (shortest distance) for absolute position inputs
for an endless axis (rotary axis with modulo calculation) possible
D
Start, interruption and abortion of a motion
D
Referencing
D
Jogging
Function:
First, up to 32 blocks consisting of position, velocity, acceleration and decel-
eration data are uploaded to the drive by the DSS. All block information may
also be replaced by the DSS during operation. The changes made will not
become effective before the next block is selected.
The following is exchanged cyclically between the master and the drive
using the ”Data_Exchange” service in order to
control the drive
:
D
PROFIBUS control word (P-0-2800)
Bit 0: Drive Halt
drive halt, setpoints are inhibited
setpoints are effective
r r r r r r r r r r r r X X X X
15
0
1
0
X = 0 or 1
r = reserved
2
1
0
1
Bit 1: Drive enable
no drive enable
drive has been enabled
0
1
Bit 2: Drive on
drive off
drive on.
0
1
Bit 3: Reset diagnostics class 1
no effect
reset diagnostics class 1
.
Bits 0, 1 and 2 are high:
Power is connected. The motor is controlled.
LSA Control S.L. www.lsa-control.com [email protected] (+34) 960 62 43 01