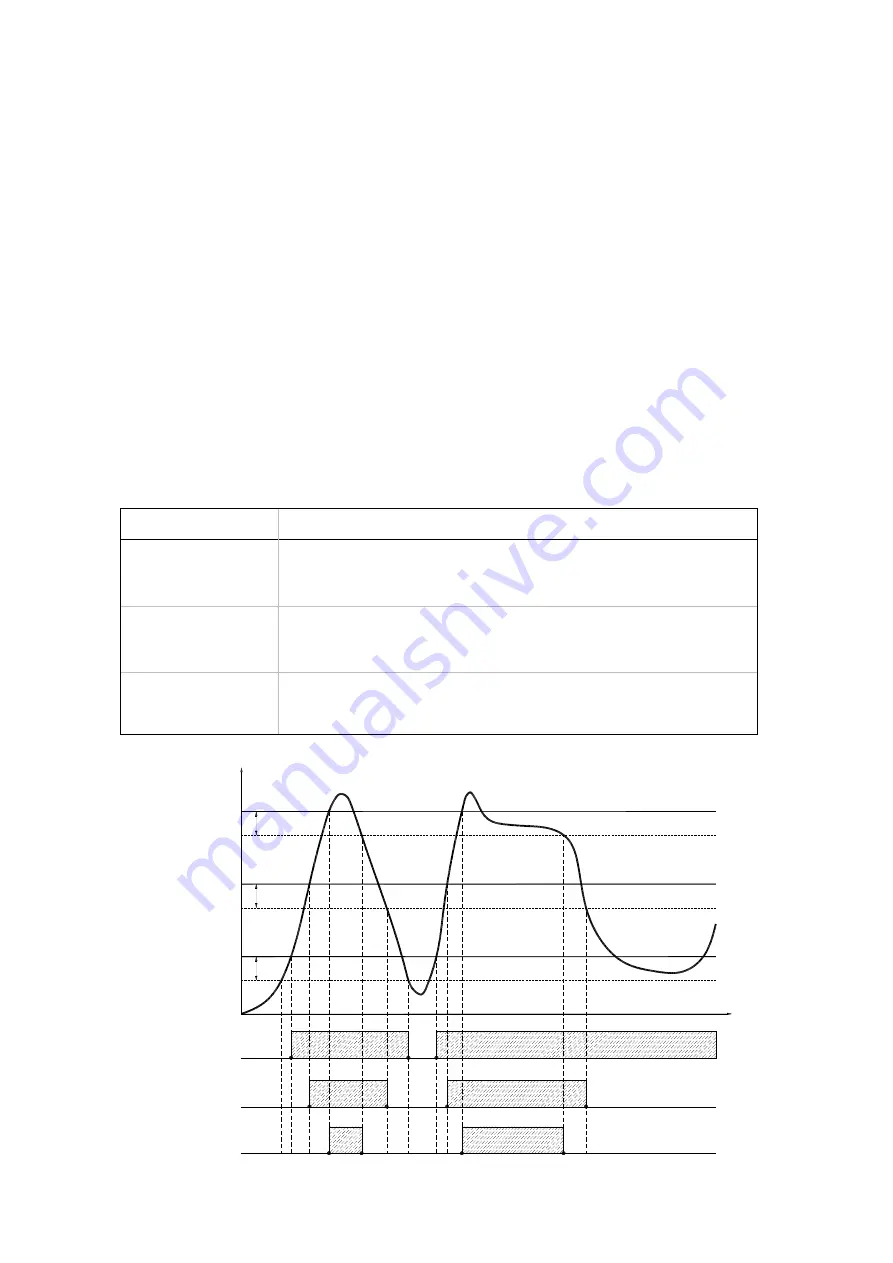
42
Di
sp
la
y
ON
OFF
RY3(L3) setting value
RY1(L1) setting value
0
Time
RY2(L2) setting value
ON
OFF
ON
OFF
LO (L1) output
OK (L2) output
HI (L3) output
Hysteresis
data width
Hysteresis
data width
Hysteresis
data width
2. High limit mode
In case of RY1(LO), RY2(OK), and RY3(HI), it is turned on when the measurement value becomes
higher than setting value and it is turned off when it becomes lower than width of hysteresis.
■
RY1(LO) output
It is immediately turned on when the measurement value becomes higher than RY1(LO) setting value.
When the measurement value becomes lower than setting value under On status of RY1(LO), it
is not immediately turned off when the measurement value becomes lower than setting value
but it is turned off when it becomes lower than width of hysteresis.
■
RY2(OK) output
It is immediately turned on when the measurement value becomes higher than RY2(OK) setting value.
When the measurement value becomes lower than setting value under On status of RY2(OK), it
is not immediately turned off when the measurement value becomes lower than setting value
but it is turned off when it becomes lower than width of hysteresis.
■
RY3(HI) output
It is immediately turned on when the measurement value becomes higher than RY3(HI).
When the measurement value becomes lower than setting value under On status of RY3(HI), it
is not immediately turned off when he measurement value becomes lower than setting value
but it s turned off when it becomes lower than width of hysteresis.
Relay Output Terminal
Output Condition
L1 (RY1/ LO)
Measurement value
≥
RY1 setting value
Measurement value
≥
RY1 setting value – Hysteresis setting value
L2 (RY2/ OK)
Measurement value
≥
RY2 setting value
Measurement value
≥
RY2 setting value – Hysteresis setting value
L3 (RY3/ HI)
Measurement value
≥
RY3 setting value
Measurement value
≥
RY3 setting value – Hysteresis setting value