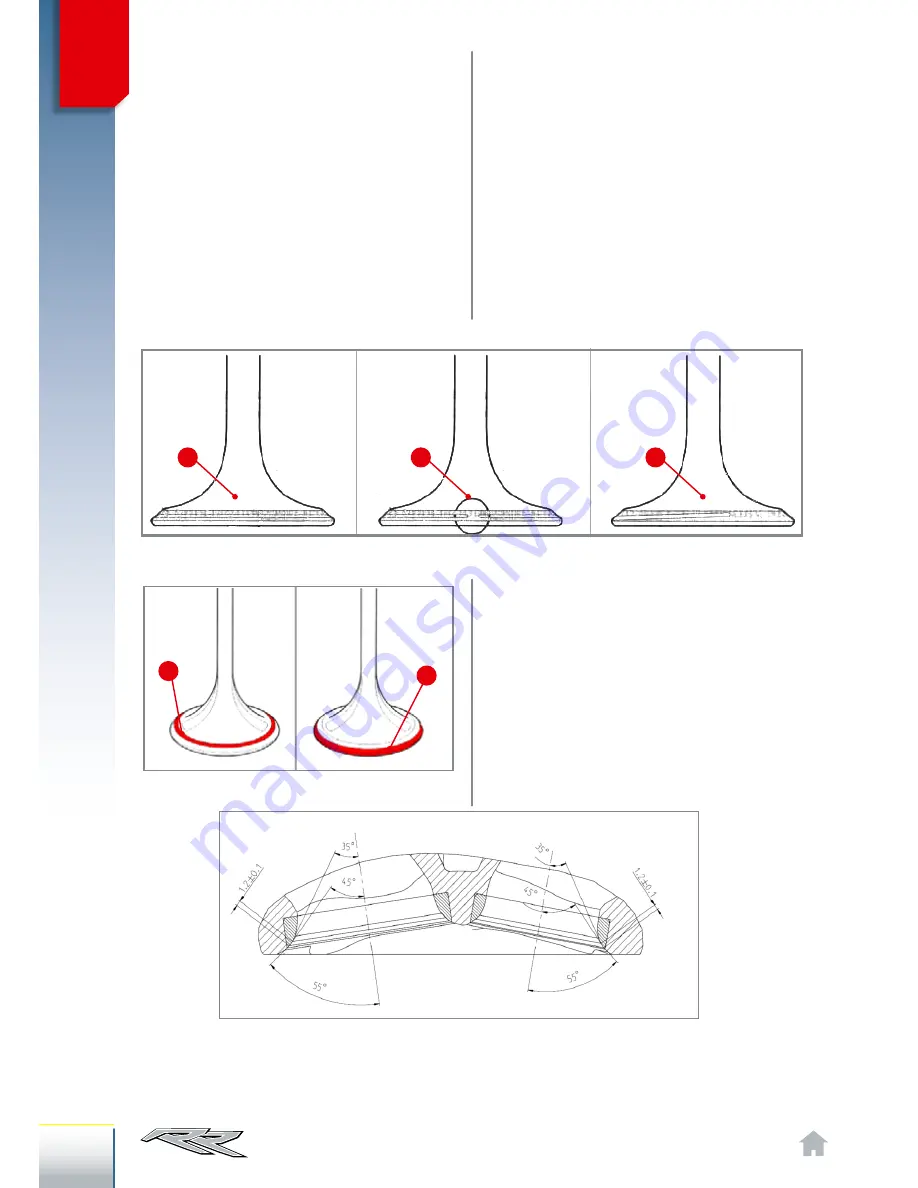
2
102
E
N
G
IN
E ASS
E
M
B
LY AN
D CO
NTRO
LS
Valve-seat contact conditions: A) Correct; B) Incorrect - contact face damaged-; C) Incorrect - uneven width-.
Positioning of contact area: D) too high; E) too low
Geometric features of valves seats.
Taking the valve out, the paint will be missing in
the contact zone. Its width must not be greater
than the following service limit:
Width service limit of valve seat contact zone:
1,9 mm.
The contact zone can principally take on three
different appearances, as shown in the figure:
A
- correct;
B
- incorrect (contact face damaged);
C
- incorrect (uneven seat width).
Also check the correct positioning of the contact
area. It must be neither higher (case
D
) or lower
(case
E
).
Should the incorrect conditions described abo-
ve occur, the valve seats must be rectified, re-
specting the conditions carried in the following
drawing.
If the valve seats are beyond recovery, replace
the cylinder head.
A
D
E
B
C
Содержание Enduro RR 350 2013
Страница 1: ......
Страница 133: ...2 131 ENGINE ASSEMBLY AND CONTROLS NOTE ...
Страница 134: ......