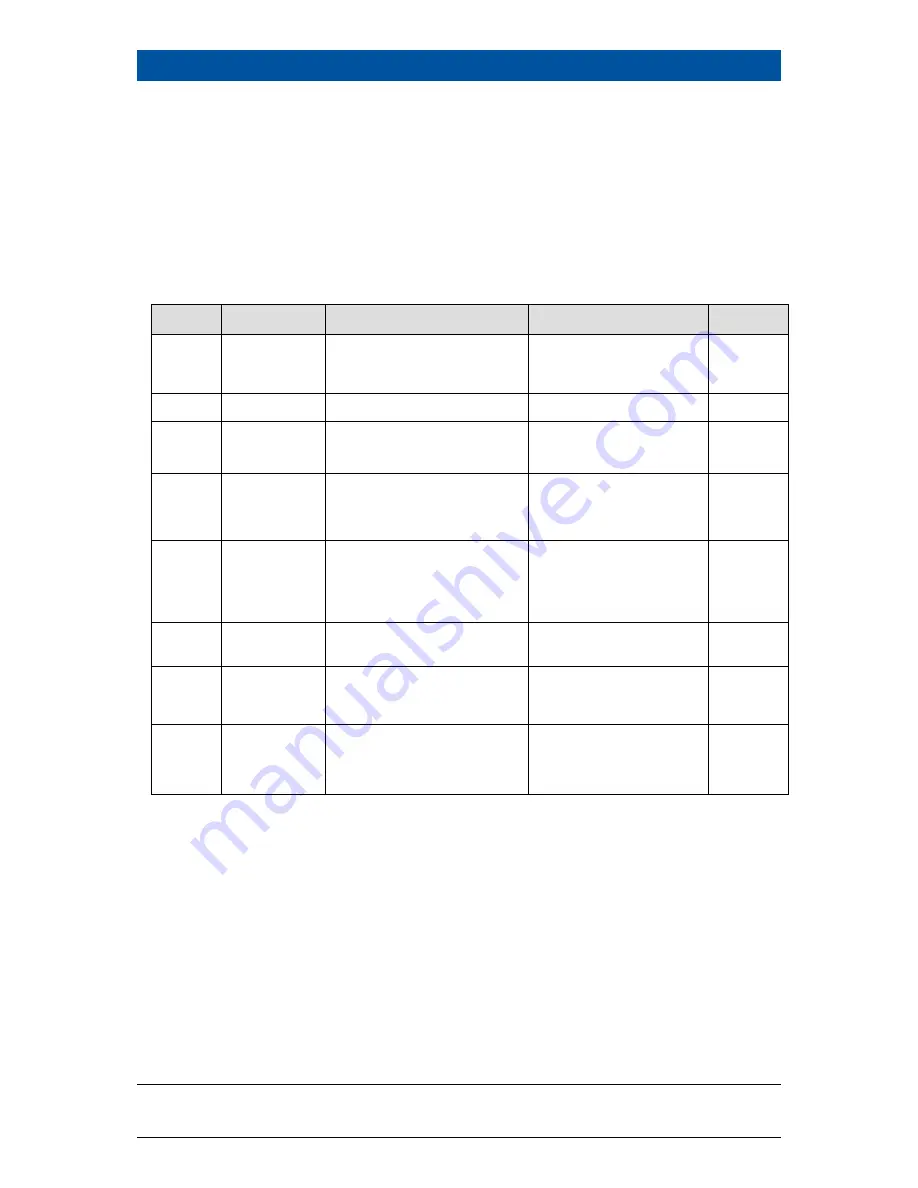
c
8 Troubleshooting
122
Rev. 04, 03/2015
b
8.2
Error Codes of the Evaluation Unit
In the following tables you can find the EVU error codes which give you exact in-
formation on how to fix them. All castXpert LB 452 errors have the prefix "M", all
GAMMAcast LB67xx errors the prefix "D".
The detector error codes can be seen in the "48452BA1" manual in chapt. 7.1.
8.2.1
System
Code
Text
Description
Correction
Class
101
HW module
corrupted
Missing circuit board or incom-
patible test header
Carry out software up-
date
Contact service
Error
102
Device data
Data inconsistency found
Carry out factory reset
Error
103
RAM, Flash or
CPU
Error in main memory
Hardware error
Contact service
Error
104
WD reset
The system has been reset by
the watch dog (WD)
Hardware error
Contact service
Warning
105
WD failure
The watch dog (WD) was acti-
vated but the system was not
reset
Hardware error
Contact service
Error
106
WD off
The debug jumper is sticking,
the watchdog is disabled
Remove debug jumper
Error
107
RTC date/time
Error in the actual time clock or
invalid time
Check the date and
time settings
Contact service
Warning
108
Software ex-
ception
Software exception
Carry out software up-
date. If the error still re-
mains, contact the ser-
vice.
Error
Содержание castxpert LB 452
Страница 2: ......
Страница 4: ......
Страница 10: ......
Страница 14: ...c 2 Safety 14 Rev 04 03 2015 b ...
Страница 22: ......
Страница 40: ......
Страница 120: ......
Страница 138: ......
Страница 140: ...c 10 Decommissioning 140 Rev 04 03 2015 b ...
Страница 146: ...c 11 Technical Information 146 Rev 04 03 2015 b 11 4 c LB 452 Connections Rear Overview ...
Страница 147: ...c 11 Technical Information b Rev 04 03 2015 147 11 5 c LB 452 Connections Measuring channel base module ...
Страница 148: ...c 11 Technical Information 148 Rev 04 03 2015 b 11 6 c LB 452 Connections Measurement ChannelEx tension Module ...
Страница 151: ...c 12 Declaration of Conformity b Rev 04 03 2015 151 12Declaration of Conformity ...
Страница 152: ...c 12 Declaration of Conformity 152 Rev 04 03 2015 b ...
Страница 155: ...c 13 Index b Rev 04 03 2015 155 ...