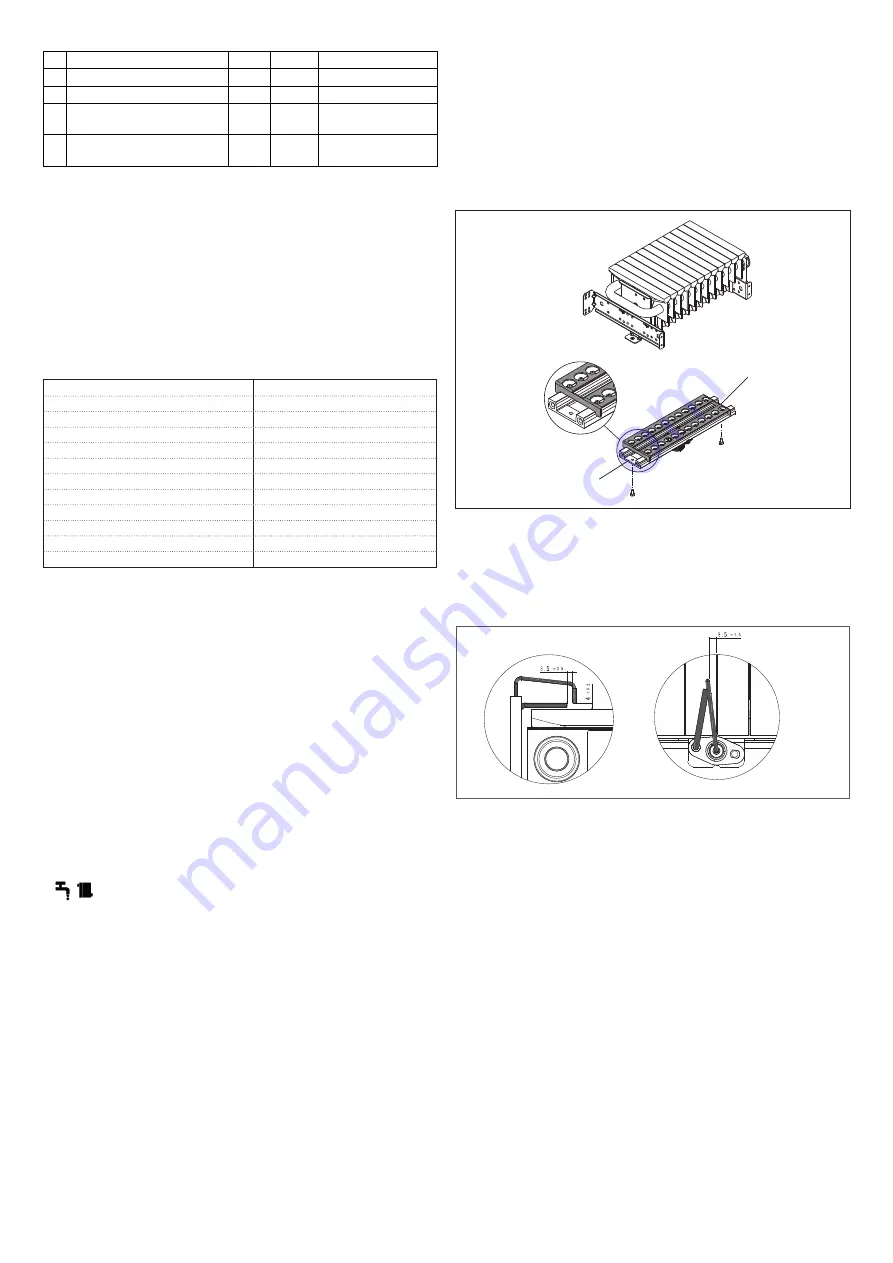
11
ENGLISH
3 Outdoor sensor temperature
°C
-20..70
4 Burner output
%
0..100
5 Not signi
fi
cant
KOhm
0..99
6 Fan speed
--
0..3
0 = Off, 1 = Min, 2 = Med,
3 = Max
7
Interval remaining before mainte-
nance
--
52
weeks
To exit the Info menu press RESET for 1 second, or press RESET for 10 seconds to exit
con
fi
guration mode.
b
By pressing the DHW+ and DHW- buttons simultaneously, it is possible to reset the
remaining service interval.
4.13
Alarms
log
Access the alarm log menu as follows:
-
press the RESET button for 10 seconds to enter the con
fi
guration mode. "tS" starts
fl
ashing on the display
-
press CH+ or CH- buttons to navigate the menu, select the Alarm log menu (Hi) and
press MODE to enter it.
The electronic board records the last 11 error codes from the most recent to the oldest.
b
Access to the menu is not allowed with the boiler in the OF state.
Par. Note
Description
r01
most recent error
r02
r03
r04
r05
r06
r07
r08
r09
r10
r11
oldest error
Press CH+ or CH- buttons to select the error, which is shown on the display with the letter
"A", alternating every 2 sec. with the numerical index of the alarm log (e.g. r01).
Press the RESET button for 1 second to exit alarm log mode or press the RESET button for
10 seconds to exit the con
fi
guration mode.
Reset alarm log
In con
fi
guration mode, press the CH+ or CH- button to navigate the menu and select the
Reset Alarm Log menu (rE).
While the display shows "rE", by pressing the MODE button for 3 seconds, it is possible to
reset the whole alarm history. After resetting the history information, the system automatically
exits installation mode.
4.14
Combustion
analysis
To activate the combustion analysis function:
-
remove the casing by undoing the fastening screws
-
undo the
fi
xing screw of the instrument panel and rotate it to a horizontal position
-
remove the screw (
A
-
fi
g. 13) and the
fl
ue gas analysis take-off plug (
B
-
fi
g. 13) and
insert the analyser
-
loosen the screw of the pressure test take-off downstream from the gas valve by roughly
two turns, then connect the pressure gauge
-
reposition the control panel and
fi
x it in place with the screw
-
place the boiler in winter mode
-
press the RESET and MODE buttons simultaneously for 5 seconds
-
the boiler will switch on at max. power; the display will show the value 100 and the
symbols will be
fl
ashing
-
read the CO and CO
2
values on the
fl
ue gas analyser. If they are different from the
values in the multigas table, check the gas pressure on the pressure gauge; if they are
correct, quit the procedure by pressing the RESET and MODE buttons simultaneously
for 5 seconds
-
if the gas pressure values read on the gauge differ from the multigas table indications,
make the adjustment by following the procedure explained in paragraph "4.16.2 Limited
range adjustment" , if on the other hand they are correct, it means the problem is not related
to the gas valve adjustment and must instead be located on the combustion components.
The combustion control function is automatically disabled after 15 minutes, or by pressing
RESET and MODE for 5 sec.
In the case of a zone system or heat dispersal in the heating system, the procedure can be
followed in DHW mode by turning on at least one hot water tap after activating the function
as explained previously, making sure that the DHW setpoint is set to the maximum value.
Remember to set it to the user desired value when
fi
nished the sequence.
When the checks have been carried out:
-
remove the pressure gauge
-
remove the
fl
ue gas analyser, close the pressure point, replace the
fl
ue gas analysis
socket cap and reposition the previously removed components.
4.15 Gas
convertion
The transformation from a gas of one family to a gas of another family can be easily done
even with the boiler installed.
The boiler is supplied for natural gas (G20) or LPG (G31) as indicated on the product plate.
- Empty the system completely, disconnect the power supply and close the gas tap.
- Access the internal parts of the boiler.
- Extract the burner completely with the collector connected, being very careful not to
damage the gas train cable gland.
CONVERTION FROM NG TO LPG
- Disconnect the NG manifold from the burner by unscrewing the appropriate
fi
screws.
- Take the LPG manifold and the
fl
ange from the appropriate conversion kit and, using the
screws previously removed, fasten both to the burner.
CONVERTION FROM LPG TO NG
- Disconnect the LPG manifold from the burner by unscrewing the appropriate
fi
xing screws.
- Remove the LPG
fl
ange.
- Take the NG manifold from the appropriate conversion kit and, using the screws
previously removed, fasten both to the burner.
LPG
fl
ange
manifold
- Reposition the burner in its seat,
fi
xing the two support brackets with the 4 screws
previously removed to the bottom of the air box.
- Reposition the spark plug and the support bracket, with the relative screws.
- Reassemble carefully following the reverse procedure.
- Pay attention to the good condition of all seals and OR, making a general tightness
check.
- Reassemble the bracket with the spark plug, checking the correct position of the
electrode as shown in the
fi
gure.
- Set parameter P01 as follows:
P01= 0 NG
P01= 1 LPG.
- After the gas transformation operations, proceed with a calibration of the gas valve as
described in paragraph "4.16.1 Auto-setting".
b
The transformation must be carried out only by quali
fi
ed personnel.
b
At the end of the transformation, apply the new identi
fi
cation plate contained in the kit.
4.16 Adjustments
The boiler is supplied for operation with methane gas (G20) or LPG (G31) and is factory set
as shown on the data plate.
b
Adjustments must be made in the sequence indicated and exclusively by the
Technical Assistance Service.
b
Adjustments cannot be made if the boiler is in the OFF state.
-
Remove the casing by loosening the fastening screws.
-
Undo the
fi
xing screw of the instrument panel.
-
Loosen the screw of the pressure test point downstream from the gas valve by roughly
two turns, then connect the pressure gauge.
4.16.1
Auto-setting
THIS PROCEDURE SHOULD ONLY BE CARRIED OUT IN THE FOLLOWING CASES:
GAS VALVE REPLACEMENT, BOARD REPLACEMENT, GAS CONVERSION.
The gas valve does not provide for mechanical calibration: valve adjustments are therefore
carried out electronically through two parameters q02 and q01.
-
Place the boiler in winter mode.
-
Referring to paragraph "4.11 Parameter access procedure (tS)" set parameter
P19 = 1
,
then exit the procedure.