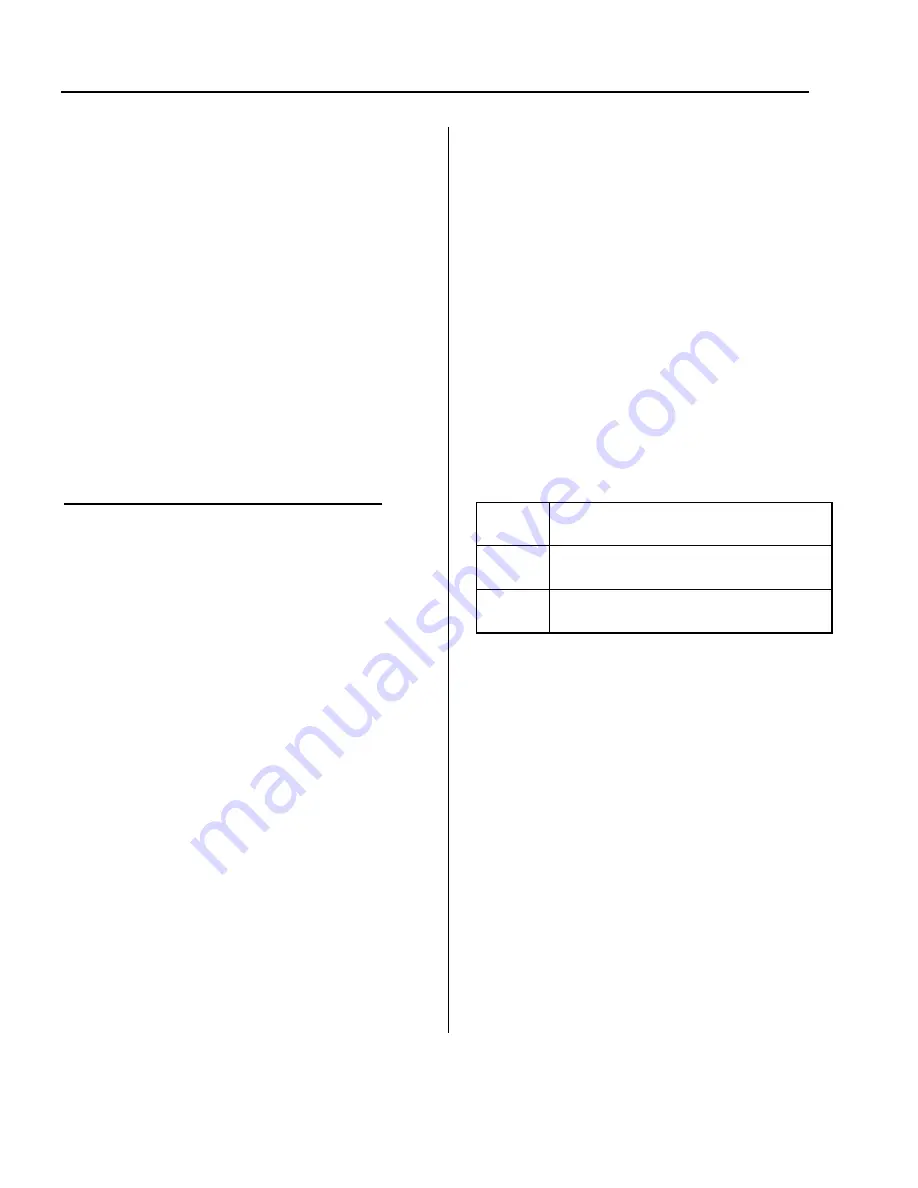
Chapter 6 - Parameter Description [APP]
6-62
[PI control]
This control is stable in many systems. If
“D control” is added, it becomes the 3
rd
order system.
In some systems this may lead to system instability.
[D Control]
The D control is the derivative part of
the feedback loop. Its primary purpose is to remove
“hunting” in the control. The D control typically is
more complicated to implement, but will result in a
more stable system. This control does not affect the
steady state error directly, but increases the system
gain because it has an attenuation effect on the
system. As a result, the differential control
component has an effect on decreasing the steady
state error. Since the D control operates on the error
signal, it cannot be used alone. Always use it with the
P control or PI control.
Parameter setting example for PID operation
①
Set APP-02 [PID operation selection] to “Yes.”
②
Select the set-point source if different from keypad
in APP-04~05 (Aux. Ref. Signal). Refer to the
following PID block diagram.
Note:
When APP-04 is set to “No,” DRV-04 [Freq
Mode] becomes PID set point source. The default
setting for DRV-04 is Keypad-1. Program the set
point via the keypad at the main screen (DRV-00). If
APP-04 is set to “Yes”, the selection set in APP-05
becomes PID set point source.
③
Set APP-06 [PID feedback selection] to I, V1 or
Pulse.
④
Select the desired units (default PSI) of the
process signals in I/O-86 [User unit selection]. This
changes the units of the parameters related to the
process (Target, Set Point, Feedback). They can be
set to Percent, Bar, mBar, kPa, Pa, or PSI.
⑤
Select the maximum value of the sensor (units) in
I/O-87.
⑥
Select the maximum value of the feedback signal
in APP-31 (default 20 mA for “I”), APP-32 (default
10V for “V1”) or APP-33 (default 100kHz for “P”).
⑦
Select frequency limits of the drive output (if
required) with APP-10 and APP-11.
⑧
Select the polarity of the PID output with APP-15.
“No” is direct (normal)
Feedback increase, Speed decrease.
“Yes” is indirect (inverse)
Feedback increase, Speed increase.
⑨
Adjust P and I gains (APP-07 and APP-08) as
necessary to obtain stable operation.
⑩
Viewable parameters are:
DRV-15
TAR 0.00 Hz
OUT 0.00 Hz
DRV-16
REF 0.00 PSI (Units per I/O-86)
FBK 0.00 PSI
DRV-18
R 0.0 Hz T 0.0 Hz
F 0.0 Hz O 0.0 Hz
Open Loop function
: To disable PID control,
program one of the multi-function input terminals
(I/O-20 through 27) to the “Open loop” function. In
Open Loop Mode, parameter DRV-04 will be the
source of the drives speed reference. To change to
another source for speed reference in Open Loop, use
the Loc/Rem function. See I/O-20 ~ I/O-27,
Loc/Rem function.
Note:
The accumulated integrator value used by I-
Gain can be set to ‘0’ by setting a multi-function
input terminal (M1 ~ M8) to ‘iTerm Clear’ in I/O-20
~ I/O-27.
Note:
The P-Gain 2 can be selected for PID
controller by setting a multi-function input (I/O-20 ~
I/O-27) to ‘P Gain 2’.
Содержание RSi SG Series
Страница 10: ......
Страница 35: ...Notes...
Страница 36: ......
Страница 56: ...3 1 Notes...
Страница 65: ...Notes...
Страница 66: ......
Страница 87: ...Notes...
Страница 88: ......
Страница 96: ...6 8 NOTES...
Страница 112: ...6 24 NOTES...
Страница 148: ...6 60 NOTES...
Страница 172: ......
Страница 188: ...Notes...
Страница 198: ...Notes...
Страница 212: ...iv...
Страница 217: ......