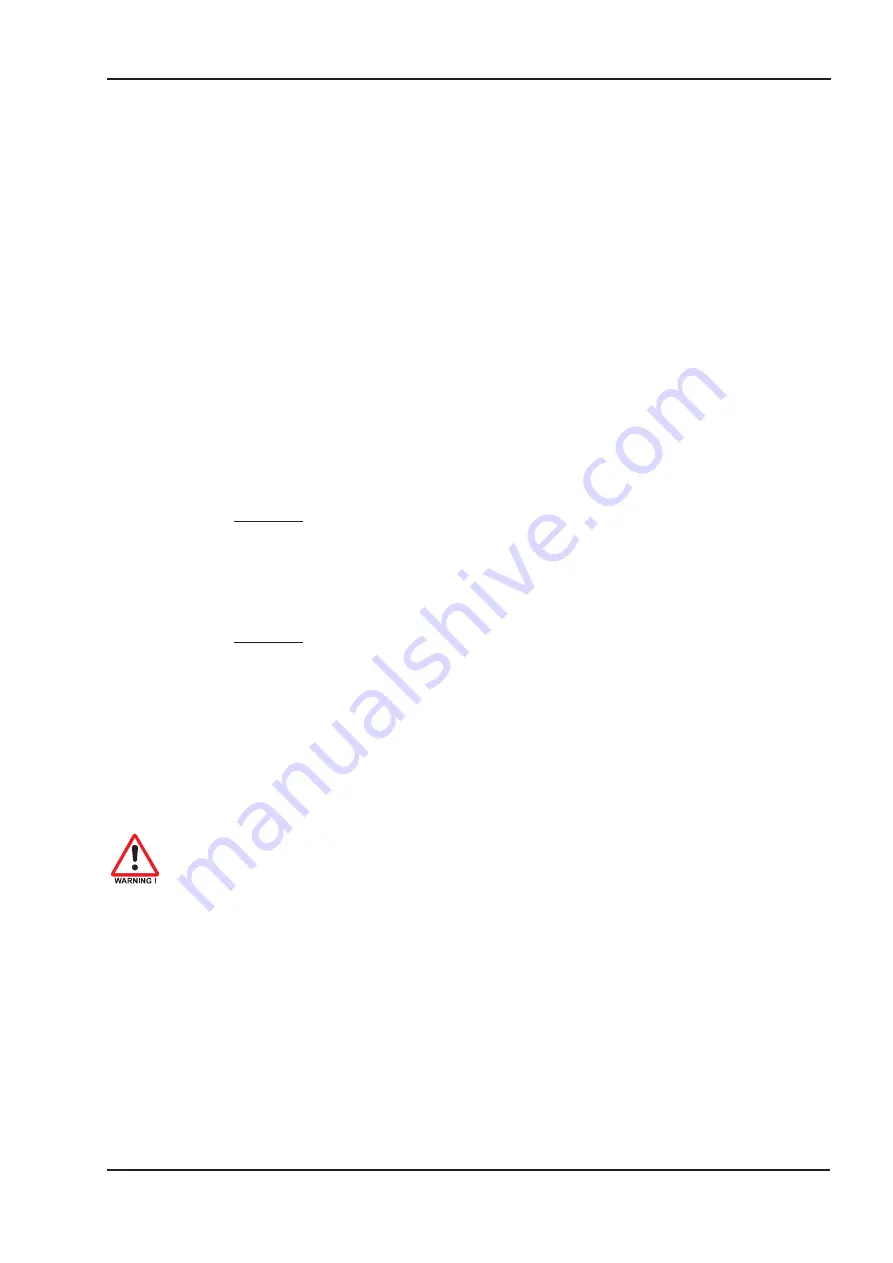
6.8.2
Emergency Stop: Standards
The emergency Stop function is used for the
fastest possible shut-down
of the machine in a dan-
gerous situation. The Emergency Stop function can be triggered by the actions of a single person. It
must be fully functional and available at all times. The user must not have to work out how to ope-
rate this mechanism.
The Emergency Stop function is defined by EN 60204 (VDE 0113), paragraph 9.2.5.4.
In addition
to the requirements for Stop, the emergency Stop must fulfil the following requirements:
l
emergency stop must have priority over all other functions and controls in all operating situa-
tions;
l
the energy supply to any drive machinery that could cause dangerous situations must be
switched off as fast as possible, without causing any further hazards (e.g. by using mechani-
cal latching devices that do not require an external supply of energy, by counter-current bra-
king in Stop Category 1);
l
the reset must not initiate a restart.
If necessary, provision must be made for the additional connection of emergency stop devices (see
EN 60204, "Requirements for emergency stop devices").
The Emergency Stop must be effective as a stop of either Category 0 or Category 1.
The Emergency Stop Category must be determined by a risk evaluation of the machine.
Category 0
Only hard-wired, electromechanical components may be used for the Category 0 Emergency Stop
function. It must not be triggered using switching logic (hardware or software), by transferring com-
mands via a communication network, or via a data link.
The drive must be shut down using an electromechanical circuit. If the connected servo motor has
an integrated brake, this must always be controlled by an electromechanical circuit as well.
Category 1
With the Category 1 Emergency Stop function, there must be absolute certainty in terms of the
power supply for the machine drives being switched off (i.e., secured) using electromechanical com-
ponents. Additional Emergency Stop equipment may be connected. Bringing the motor to a stand-
still by interrupting the mains supply and using controlled electronic braking. The 24 V supply for the
servo amplifier must remain constant. The issue of which circuit should be used is highly dependent
on the requirements of the application at hand.
Usually a brake in a servo motor only has the function of a holding brake. To ensure an emergency
stop function, the braking torque that is required must be checked. If the holding brake fulfills the
dynamic requirements, it must be taken into acount that this application will cause increased wear.
The parameters “STOPMODE” and “ACTFAULT” must be set to 1 in order to
implement the stop categories. If necessary, change the parameters via the
terminal screen of the setup software and store the data in the EEPROM.
AX2040/2070 Product Manual
27
BECKHOFF
06/2007
Technical description
Содержание AX2040
Страница 35: ...7 4 Dimensions AX2040 2070 Product Manual 35 BECKHOFF 06 2007 Mechanical Installation...
Страница 44: ...8 6 Pin assignments 44 AX2040 2070 Product Manual Electrical Installation 06 2007 BECKHOFF...
Страница 108: ...This page has been deliberately left blank 108 AX2040 2070 Product Manual Expansion Cards 06 2007 BECKHOFF...