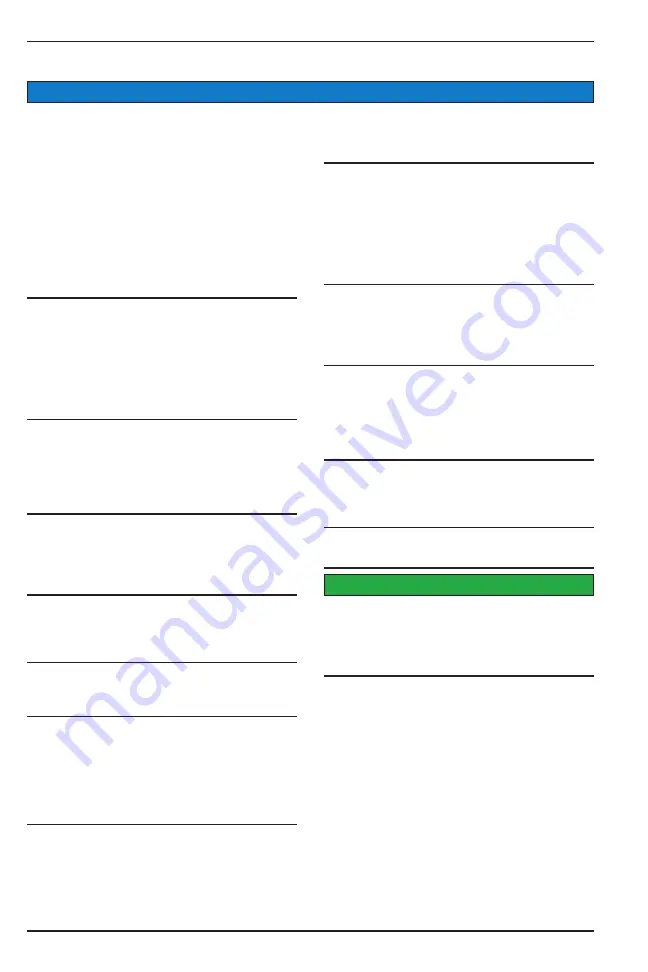
10
3/19
SAFETY PROCEDURES
MODEL 12XP CE
Do not attempt to start the engine or engage the
engine PTO (power‑take‑off) system on this machine
if the chipper drum is jammed or frozen in place. If
you do, you will damage or ruin the drive system
which will not be covered under warranty and will
cost you down time and money.
SAFETY PROCEDURES
NOTICE
Clean machine of all debris. Do not leave this
machine unattended until all potential flammable
debris is removed, no fire or smoldering exists, and
hot spots are cold. The engine creates many hot
spots including: exhaust manifold, exhaust, turbo
(if equipped), etc. Remove all flammable debris
such as wood, chips, leaves, oils, fuels from engine
exhaust, engine turbo (if equipped), beside, around,
and under engine, around and under tanks, inside
belt shields and guards, inside battery and tool
boxes, inside cabinets (if equipped), and anywhere
materials collect. Always keep several type A:B:C fire
extinguishers operational and on the job at all times.
It is very important after you have operated a new
machine for approximately an hour to shut down the
machine and recheck all nuts and bolts. It is normal
for nuts and bolts to loosen once on a new piece of
machinery. If you tighten them now, there is a good
possibility they won’t loosen again. All nuts and bolts
should be checked daily, especially the anvil and
knife nuts and bolts for torque and fit.
Every time the engine is started, let the chipper
drum turn at the lowest RPM’s possible. Listen for
any type of noise that is foreign. Any steel on steel
noise is foreign. If you hear a noise, stop the engine,
find the problem and fix it.
Most of the nuts used on the machine are self
locking. After a nut or bolt has been removed five
times, it must be replaced to ensure proper tightness.
This is especially critical on the chipper knife nuts
and bolts. Anvil hardware must be replaced when
the anvil is replaced.
In cold weather situations let your hydraulic
system idle for approximately 15 minutes to allow
the system to warm up to operating temperature.
It is very important after you have operated a new
machine for approximately an hour to shut down the
machine and recheck all hydraulic fittings. Relieve
all pressure and retighten as needed.
The patented Last Chance Stop is a means of
stopping/ reversing the feedwheels if a negligent
operator does not follow the safety rules and finds
themselves in trouble! Do not rely on the Last Chance
Stop to disobey the operator rules! The Last Chance
Stop does nothing for the foolish operator who kicks
into the infeed hopper area.
With engine shut off and all moving parts stopped,
daily pull last chance cables to ensure they freely
disengage and reverse feed wheel hydraulic valve.
Do not operate this machine unless all hydraulic
control devices operate properly. They must function,
shift and position smoothly and accurately at all
times.
Make sure the machine is in good operating
condition and that all safety devices, including
guards and shields are installed and functioning
properly. Visually inspect the machine daily before
starting the machine. Refer to the “Daily Start Up
& Maintenance”. Make no modifications to your
equipment unless specifically recommended or
requested by Bandit Industries Inc.
This chipper is designed to be hand fed only. Do
not feed wood with any type of knuckle boom loader,
front end loader, or mechanical device. It will cause
damage to the machine. If this happens, the machine
will not be covered under warranty.
Check laws and regulations. Know and obey all
federal, state, and local laws and regulations that
apply to your work situation and the transportation
of a machine this size.
The winch line hook must be sized properly so
that it will not fit through the winch fairlead or rollers.
SAFETY INSTRUCTIONS
Before attempting any type of maintenance,
disengage clutch, wait for the drum to come to a complete
stop, turn off engine, remove the ignition key, make
sure the ignition key is in your possession, install the
drum lock pin, and disconnect the battery.
Always install the drum lock pin to prevent
inadvertent rotation. Insert the lock pin through the
lock pin tube on the drive side of the drum housing.
This is to ensure the chipper drum cannot be started
while you are working inside the machine. If, for some
reason, the drum started to turn, it would simply hit
the lock pin.
Содержание Intimidator 12XP
Страница 2: ......
Страница 18: ......
Страница 80: ...66 3 19 Replacement Parts Model 12XP CE HYDRAULIC FUEL TANK ASSEMBLY 4 5 10 6 7 9 8 7 11 3 2 2 1...
Страница 82: ...68 3 19 Service Record Model 12XP CE SERVICE RECORD DATE DESCRIPTION AMOUNT...
Страница 106: ...Bandit Controls CE 3 19 92 24 245840062970 8Oct2018 Program Notes Thr dn btn overrides thr up input...
Страница 108: ...Bandit Controls CE 3 19 94 SERVICE RECORD DATE DESCRIPTION AMOUNT...