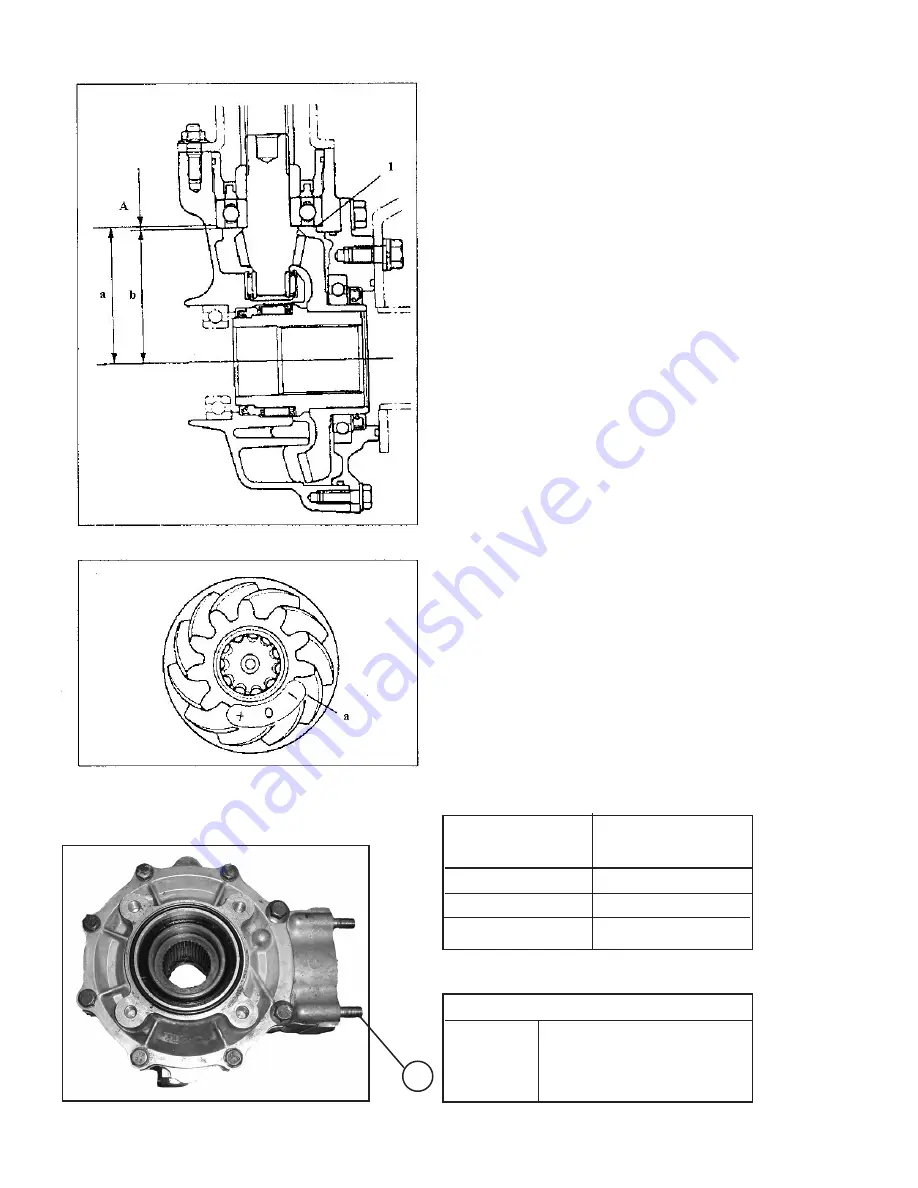
(VI) Choice of main driving and shift gear pad
1. Main driving gear pad (1) choice:
Use “A” = (a) - (b) to work out main driving
gear pad thickness
(a) =84 +/- engraved number on main driving
gear
(b) =83.5 +/- engraved number on driving gear
case body
CAUTION:
The unit of numbers on the main driving gear and
case body =1/100mm
Example:
1) If “+01” is engraved on the main driving gear
then:
(a) is 84+0.01=84.01
2) If “10” is engraved on the main driving gear
then:
(b) is 83.5+0.10=83.60
3) “A”=0.41
4) Chose the proper pad and correct the percent
digit The resulted value in the example is 0.41,
but the meter specifies to change 1 of the per
-
centage digit to 0. The pad thickness will then be
0.40mm
Number on Amending
percent digit
value
0,1,2
0
3,4,5,6,7
5
8,9
10
Pad thickness
Main driving gear pad
Thickness 0.15
0.50
(mm)
0.30
0.60
0.40
1
78
Содержание WD250U
Страница 1: ...WD250U Service Manual For any questions please contact Baja Motorsports at 888 863 2252 ...
Страница 23: ... II Wiring diagram 1 23 ...
Страница 24: ... III Wiring diagram 2 24 ...
Страница 25: ... IV Wiring diagram 1 25 ...
Страница 31: ...Section 8 Lubrication I Lubrication oil way 31 ...
Страница 120: ...119 ...