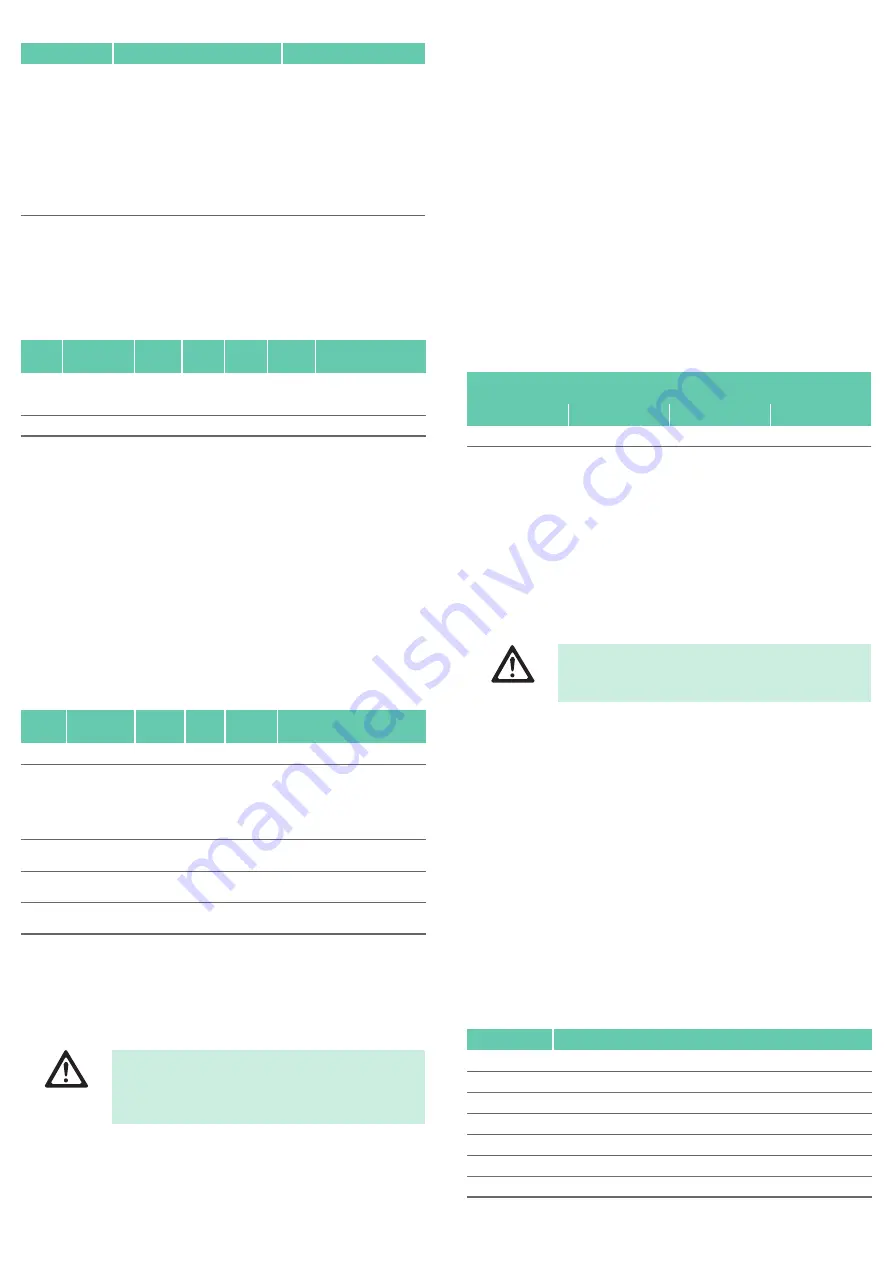
Validated cleaning and disinfection procedure
Mechanical cleaning/disinfection with manual pre-cleaning
Note
The cleaning and disinfection device must be of tested and approved effectiveness (e.g. FDA approval or CE mark
according to DIN EN ISO 15883).
Note
The cleaning and disinfection device used for processing must be serviced and checked at regular intervals.
Manual pre-cleaning with a brush
D–W:
Drinking water
RT:
Room temperature
*Recommended: BBraun Stabimed
►
Note the information on appropriate cleaning brushes and disposable syringes, see Validated cleaning and dis-
infection procedure.
Phase I
►
Fully immerse the product in the cleaning/disinfectant for at least 15 min. Ensure that all accessible surfaces are
moistened.
►
Clean the product with a suitable cleaning brush in the solution until all discernible residues have been removed
from the surface.
►
If applicable, brush through non-visible surfaces with an appropriate cleaning brush for at least 1 min.
►
Mobilize non-rigid components, such as set screws, links, etc. during cleaning.
►
Thoroughly rinse through these components with the cleaning disinfectant solution (at least five times), using a
disposable syringe.
Phase II
►
Rinse/flush the product thoroughly (all accessible surfaces) under running water.
►
Mobilize non-rigid components, such as set screws, joints, etc. during rinsing.
Mechanical alkaline cleaning and thermal disinfecting
Machine type: single-chamber cleaning/disinfection device without ultrasound
D–W:
Drinking water
FD–W:
Fully desalinated water (demineralized, low microbiological contamination: drinking water quality
at least)
*Recommended: BBraun Helimatic Cleaner alkaline
►
Check visible surfaces for residues after mechanical cleaning/disinfecting.
Inspection, maintenance and checks
►
Allow the product to cool down to room temperature.
►
After each complete cleaning, disinfecting and drying cycle, check that the product is dry, clean, operational, and
free of damage (e.g. broken insulation or corroded, loose, bent, broken, cracked, worn, or fractured components).
►
Dry the product if it is wet or damp.
►
Repeat cleaning and disinfection of products that still show impurities or contamination.
►
Check that the product functions correctly.
►
Immediately put aside damaged or inoperative products and send them to Aesculap Technical Service, see Tech-
nical Service.
►
Assemble dismountable products, see Assembling.
►
Check for compatibility with associated products.
Packaging
►
Appropriately protect products with fine working tips.
►
Place the product in its holder or on a suitable tray. Ensure that all cutting edges are protected.
►
Pack trays appropriately for the intended sterilization process (e.g. in Aesculap sterile containers).
►
Ensure that the packaging provides sufficient protection against recontamination of the product during storage.
Steam sterilization
Note
The product can be sterilized either in disassembled or in assembled condition.
►
Check to ensure that the sterilizing agent will come into contact with all external and internal surfaces (e.g. by
opening any valves and faucets).
►
Validated sterilization process
–
Steam sterilization using fractional vacuum process
–
Steam sterilizer according to DIN EN 285 and validated according to DIN EN ISO 17665
–
Sterilization using fractional vacuum process at 134 °C/holding time 5 min
►
When sterilizing several products at the same time in a steam sterilizer, ensure that the maximum load capacity
of the steam sterilizer specified by the manufacturer is not exceeded.
Sterilization for the US market
■
Aesculap advises against sterilizing the device by flash sterilization or chemical sterilization.
■
Sterilization may be accomplished by a standard prevacuum cycle in a steam autoclave.
To achieve a sterility assurance level of 10
-6
, Aesculap recommends the following parameters:
*Aesculap has validated the above sterilization cycle and has the data on file. The validation was accomplished in an
Aesculap sterile container cleared by FDA for the sterilization and storage of these products. Other sterilization cycles
may also be suitable, however individuals or hospitals not using the recommended method are advised to validate
any alternative method using appropriate laboratory techniques. Use an FDA cleared accessory to maintain sterility
after processing, such as a wrap, pouch, etc.
WARNING for the US market
If this device is/was used in a patient with, or suspected of having Creutzfeldt-Jakob Disease (CJD), the device
cannot be reused and must be destroyed due to the inability to reprocess or sterilize to eliminate the risk of
crosscontamination.
Storage
►
Store sterile products in germ-proof packaging, protected from dust, in a dry, dark, temperature-controlled area.
Technical Service
►
For service and repairs, please contact your national B. Braun/Aesculap agency.
Modifications carried out on medical technical equipment may result in loss of guarantee/warranty rights and for-
feiture of applicable licenses.
Service addresses
Aesculap Technischer Service
Am Aesculap-Platz
78532 Tuttlingen / Germany
Phone:
+49 (7461) 95-1602
Fax:
+49 (7461) 16-5621
E-Mail:
Or in the US:
Attn. Aesculap Technical Services
615 Lambert Pointe Drive
Hazelwood
MO, 63042
Aesculap Repair Hotline
Phone:
+1 (800) 214-3392
Fax:
+1 (314) 895-4420
Other service addresses can be obtained from the address indicated above.
Accessories/Spare parts
For MINOP inVent tubular shaft instruments FH635R, FH636R, FH637R, FH638R,
FH639R
Validated procedure
Specific requirements
Reference
Manual pre-cleaning
with brush and subse-
quent mechanical
alkaline cleaning and
thermal disinfection
■
Cleaning brush: e.g., TA012889
■
20 ml disposable syringe
■
Place the product in a tray that is suitable
for cleaning (avoiding rinsing blind
spots).
■
Connect components with lumens and
channels directly to the rinsing port of
the injector carriage.
■
Keep working ends open for cleaning.
■
Place products in the tray with their
hinges open.
Chapter Mechanical cleaning/disin-
fection with manual pre-cleaning
and sub-chapter:
■
Chapter Manual pre-cleaning
with a brush
■
Chapter Mechanical alkaline
cleaning and thermal disinfecting
Phase
Step
T
[°C/°F]
t
[min]
Conc.
[%]
Water
quality
Chemical
I
Disinfec-
tant
cleaning
RT (cold)
>15
2
D–W
Aldehyde-free, phenol-free,
and QUAT-free concentrate,
pH ~ 9*
II
Rinsing
RT (cold)
1
-
D–W
-
Phase
Step
T
[°C/°F]
t
[min]
Water
quality
Chemical
I
Prerinse
<25/77
3
D–W
-
II
Cleaning
55/131
10
FD-W
■
Concentrate, alkaline:
–
pH = 13
–
<5 % anionic surfactant
■
0.5 % working solution
–
pH = 11*
III
Intermediate
rinse
>10/50
1
FD-W
-
IV
Thermal disin-
fecting
90/194
5
FD-W
-
V
Drying
-
-
-
According to the program for cleaning
and disinfection device
CAUTION
Damage (metal seizure/friction corrosion) to the product caused by insufficient
lubrication!
►
Prior to function checks, lubricate moving parts (e.g. joints, pusher compo-
nents and threaded rods) with maintenance oil suitable for the respective ster-
ilization process (e.g. for steam sterilization: Aesculap STERILIT® I oil spray
JG600 or STERILIT® I drip lubricator JG598).
Aesculap Orga Tray/Sterile container (perforated bottom)
Minimum cycle parameters*
Sterilization method
Temp.
Time
Minimum drying time
Prevacuum
270 °F/275 °F
4 min
20 min
WARNING
Risk of injury and/or malfunction!
►
Do not modify the product.
Art. no.
Designation
FH633R
MINOP inVent hand grip for tubuluar shaft instruments
FH635200
MINOP inVent tubuluar shaft instruments outer tube
FF435R
Jaw part with MINOP mirco-scissors Sh/Sh
FF436R
Jaw part with MINOP mirco-scissors Bl/Bl
FF437R
Jaw part with MINOP micro cupped biopsy forceps
FF438R
Jaw part with MINOP micro grasping and preparation forceps
FF439R
Jaw part with MINOP toothed micro forceps