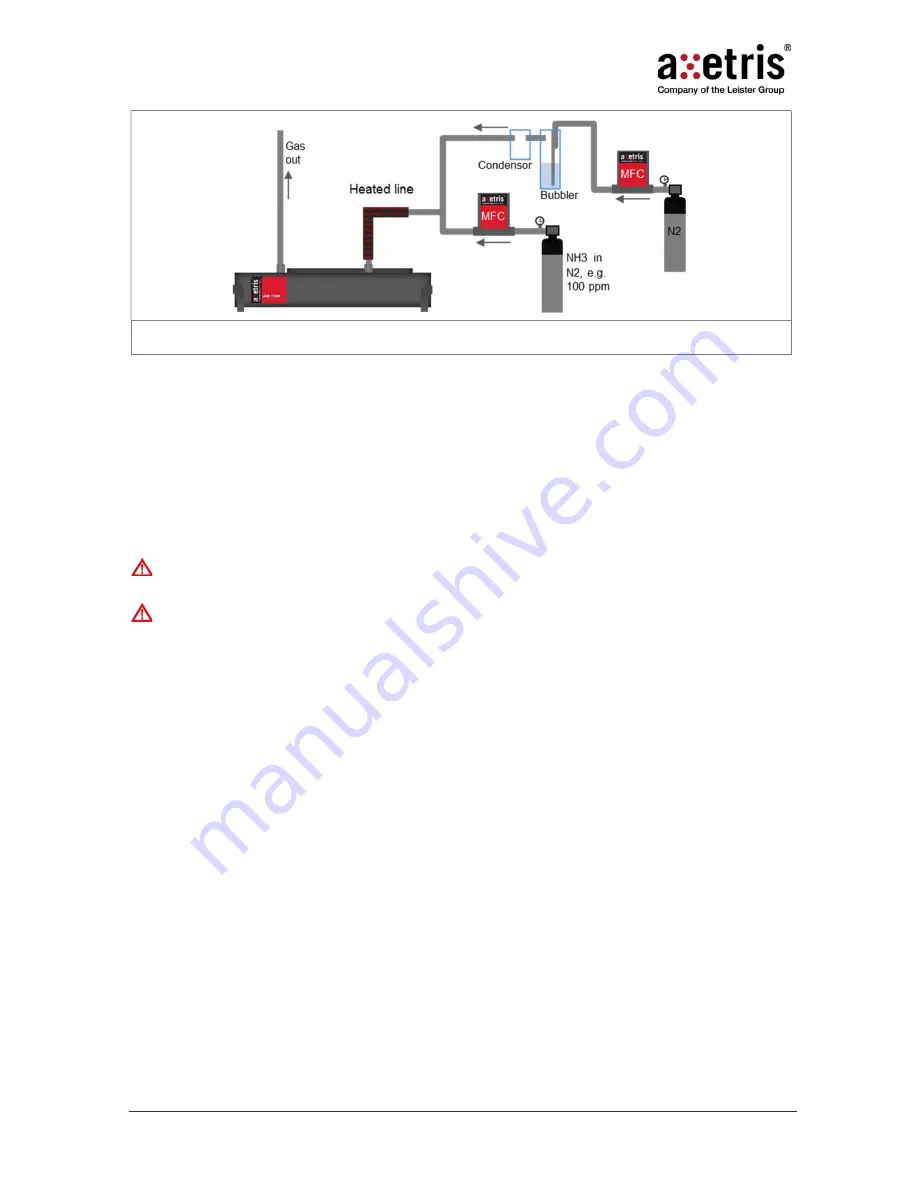
Axetris AG
LGD F200P2 Operating Instructions - Rev D
19.09.2018
17/60
Figure 12
Schematic of a simple test setup for hot-gas ammonia measurements
Guiding the ready mixed sample gas flow through a humidifier can lead to a significant wash
out of the ammonia. Place the humidifier into the nitrogen stream only.
The temperature displayed in the LGD Graphic User Interface (GUI) indicates the
measurement cell temperature, NOT the gas temperature.
The sensor is calibrated to a certain pressure in the 800 – 1100 mbar interval. Deviations
from this calibration pressure within the interval can lead to measurement errors of up to 20
percent, dependent on gas matrix and temperature.
In order to obtain the best possible performance concerning response time we recommend a
flow rate of 3 l/min through the sensor. Significantly larger flows than 5 l/min can lead to
turbulences and degradation of measurement precision. Smaller flows do not lead to errors
or misreadings, but simply increase the response time.
Each heater power supply must be limited to 12 Vcc max or 4 A max. Higher values can lead
to destruction of the sensor (or to 12 Vcc/8A in case only one supply is used).
The LGD F200P2 cell (heated version) is protected with an internal safety switch which shuts
off the heating elements if the cell temperature exceeds 250°C / 482°F.
2.6 Gas conditioning and filtering information
The LGD F200P2 Gas Sensor Modules are based on an optical measurement technique where
performance is directly linked to optical transmission through the measurement cell. Sample gas
containing particles and aerosols are likely to contaminate the optical windows of the measurement cell
and degrade the optical transmission more or less quickly. Contamination strongly depends on particle
size, material, charging effects, etc. which can vary considerably across different applications. It is
therefore generally very difficult to give a precise specification concerning the purity of the gas in order to
avoid contamination on a reasonable time scale.
Filtration setups can be as simple as a PTFE in-line syringe filter in environmental applications, or as
complicated as three-stage filtering solutions of exhaust gas in high dust-load and high SO
2
emission
control applications. According to different companies providing filter technology for analytical instruments
used in exhaust gas sensing, proper filtering can solve the problem of contamination completely.
However, filtering needs to be application-specific and hence we advise our customers to get in touch with
experts in that field (list of references available upon request).
Hot-gas filter solutions offer a wide variety of different gas treatment technologies including filters in
different sizes and qualities. Typically, up to three filter stages are used with a high efficiency of particles
as low as 0.1 μm (sinter ceramic filters, sinter metal filters, quartz glass wool and quartz glass fiber filters,
etc). When discussing the appropriate filter technology with these companies, great care also should be
taken that the used filter technology does not alter the measurement outcome.
In case of hot sample gases, it is important that the filters are heated as well in order to avoid
condensation and the creation of droplets in the gas stream. In addition, aerosols in the sensor module
can be avoided by an adequate filter, at the inlet of the sensor in particular, when pressure reducers are
used up-stream. When a significant amount of humidity is in the sample gas, it also is important that the
Содержание LGD F200P2
Страница 1: ...Operating Integration Instructions Laser Gas Detection OEM Module LGD F200P2 Axetris AG...
Страница 57: ...Axetris AG LGD F200P2 Operating Instructions Rev D 19 09 2018 57 60 Notes...
Страница 58: ...Axetris AG LGD F200P2 Operating Instructions Rev D 19 09 2018 58 60 Notes...
Страница 59: ...Axetris AG LGD F200P2 Operating Instructions Rev D 19 09 2018 59 60 Notes...
Страница 60: ...Axetris AG LGD F200P2 Operating Instructions Rev D 19 09 2018 60 60 Notes...