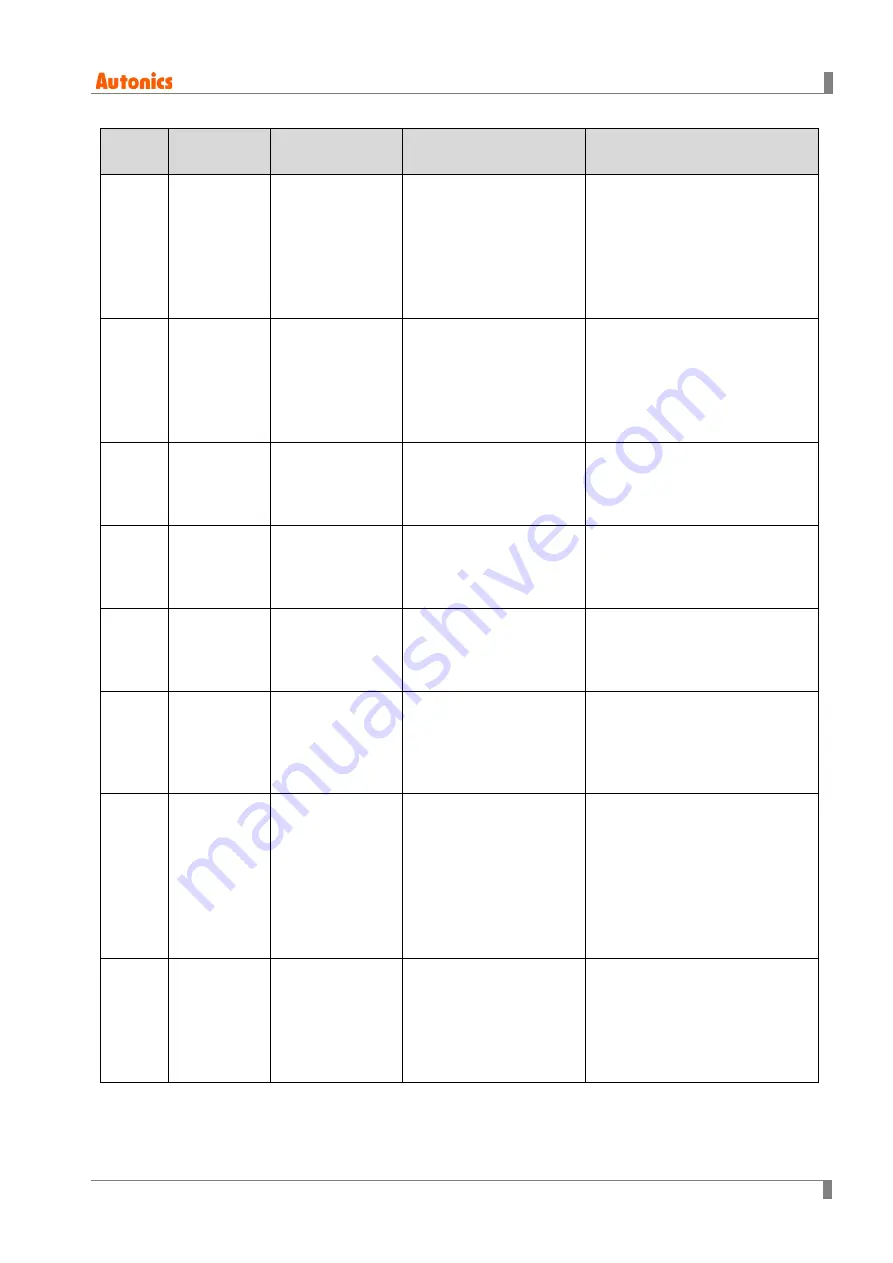
13 Protection Function
© Copyright Reserved Autonics Co., Ltd.
125
No. of
flashing
Alarm type Desctiptions
Causes
Troubleshooting
4 (
E4
)
Over load
error
When applying
load over the
rated load for over
1 sec.
1. Over load
2. Insufficient SMPS
capacity
1. Change operation condition or
reduce load so that sudden load
fluctuation does not occur.
2. Check that less than the
recommended SMPS capacity is
used.
3. Check driver break.
5 (
E5
)
Over heat
error
When driver inner
temperature is
over 85
℃
1. Installed in an enclosed
space
1. Change the installation
environment.
-Air flow around driver
installation.
-Heat dissipation (heat sink or
fan)
6 (
E6
)
Motor
connection
error
When motor cable
connection error
occurs at driver
1. Motor connector and
cable connection error
2. Burnout of the inverter
in the driver
1. Check motor connector and
cable connection.
2. Replace burned parts of the
inverter in the driver.
7 (
E7
)
Encoder
connection
error
When encoder
cable connection
error occurs at
driver
1. Motor connector and
cable connection error
2. Burnout of line driver IC
in encoder
1. Check motor connector and
cable connection.
2. Replace the line driver IC in
encoder.
8 (
E8
)
Over voltage
error
When input
voltage is over
24VAC +10%
1. Over load
2. Counter electromotive
force overflow due to
rapid deceleration
1. Change operation condition or
reduce load so that sudden load
fluctuation does not occur.
9 (
E9
)
Under
voltage error
When input
voltage is under
24VAC-10%
1. Low voltage
1. Change operation condition or
reduce load so that sudden load
fluctuation does not occur.
10 (
EA
)
Motor
mis-
alignment
When motor is in
misalignment
1. Motor connector and
cable connector error
2. Burnout of line driver IC
in driver
3. Burnout of line driver IC
in encoder
4. Burnout of the inverter
in the driver
1. Check motor connector and
cable connection.
2. Replace the line driver IC in
driver.
3. Replace the line driver IC in
encoder.
4. Replace burned parts of the
inverter in the driver.
11 (
EB
) Input pulse
error
When input pulse
is over 3,500rpm
When input pulse
is input befor
initial motor
alignment
1. Enter error of user
command speed input
1. Use recommended
specifications. (max. 3,000rpm
input)
2. Enter the speed value (PPS) by
checking the resolution.
Содержание AiCA Series
Страница 2: ...ii Copyright Reserved Autonics Co Ltd ...
Страница 35: ...6 Characteristics Copyright Reserved Autonics Co Ltd 35 ...
Страница 70: ...10 Drive 70 Copyright Reserved Autonics Co Ltd ...
Страница 72: ...10 Drive 72 Copyright Reserved Autonics Co Ltd ...
Страница 74: ...10 Drive 74 Copyright Reserved Autonics Co Ltd ...
Страница 76: ...10 Drive 76 Copyright Reserved Autonics Co Ltd ...
Страница 84: ...10 Drive 84 Copyright Reserved Autonics Co Ltd ...
Страница 130: ...14 Troubleshooting 130 Copyright Reserved Autonics Co Ltd ...
Страница 131: ... Dimensions or specifications on this manual are subject to change and some models may be discontinued without notice ...