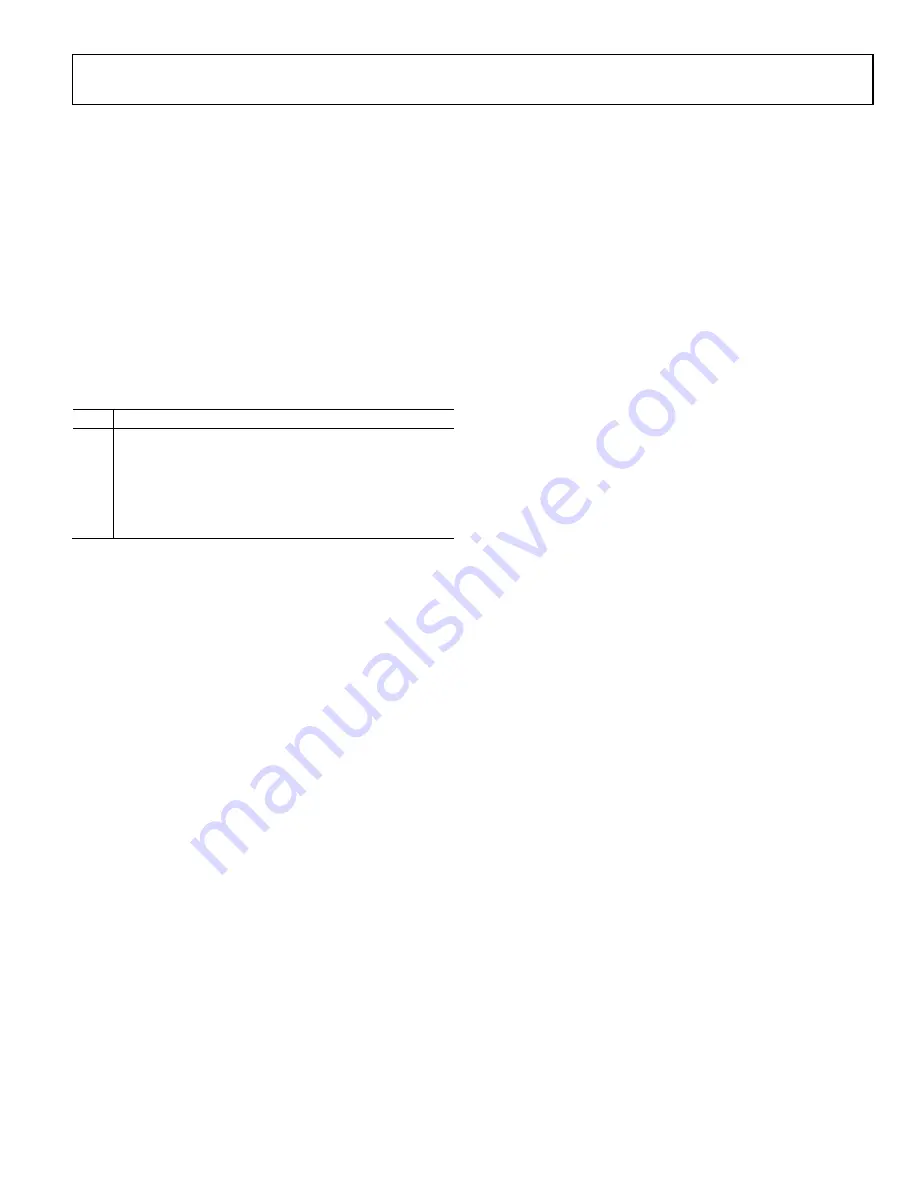
AD9361 Reference Manual
UG-570
| Page 71 of 128
FACTORY CALIBRATIONS
OVERVIEW
Factory calibrations are necessary to limit the amount of
variation seen across a large quantity of circuit boards. Some
calibrations are used to increase the accuracy of the
AD9361
device, while others are needed to calibrate non-linearities of
external components in the RF front-end. The factory
calibrations described in Table 42 are suggested calibrations.
The number of calibration points for a specific design is
dependent on the temperature stability and linearity of the RF
components. The actual factory calibrations necessary might
vary from Table 42 depending on the accuracy and
performance of the desired system.
Table 42. Suggested Factory Calibrations
#
Factory Calibration
1
Internal DCXO (AFC tune range)
2
Tx RSSI (Tx monitor)
3
Rx RSSI
4
Rx GM/LNA gain step error
5
Tx power out vs. Tx attenuation
6
Tx power out vs. frequency
INTERNAL DCXO
If using an external clock into the REF_CLK_IN pin, ignore this
calibration.
The
AD9361
device can use a crystal oscillator (XO) to clock
the chip. In this mode, the
AD9361
has an internal DCXO
(digitally control oscillator) that can pull the XO frequency.
This is necessary to cancel out carrier frequency offset and
Doppler shift due to mobility. Carrier frequency offset can also
occur due to the XO changing temperature.
The DCXO tune registers consist of a coarse tune value and a
fine tune value. During factory calibration, the coarse tune
setting should be found such that the fine tune range is centered
evenly around the desired XO frequency. This would ensure the
widest usable DCXO range.
If necessary by the system, the factory calibration could also
sweep the DCXO fine tune codes to produce a LUT of
frequency error vs. fine tune code to allow quick updates of
the XO tuning. The temperature sensor could also be read to
aid in correcting for the frequency variation across temperature
of the XO.
Tx RSSI (Tx MONITOR)
If the power detector is used, at minimum, a single point Tx
RSSI measurement must be made to correlate the absolute
output power after the PA to the Tx RSSI value reported by the
AD9361
device. Typically, a coupler is used to sample the power
after the PA back into the Tx monitor input of the
AD9361
device. During this measurement, transmit a typical burst. A
signal with constant power (such as a preamble) would give the
most accurate results. Once a single point measurement has
been measured, the Tx RSSI for other Tx power out levels can
be calculated with the assumption that the assumption that the
Tx path is linear, the power detector path is linear and all
external RF components in the path are operating in their linear
regions. If the system requires a higher precision of power
control, multiple points across the
AD9361
Tx attenuation
range and carrier frequency range can be measured during this
factory calibration to generate a matrix of Tx RSSI correction
values.
The factory calibration should be completed using the
corresponding transmitter on the
AD9361
device to transmit a
known reference signal while the Tx RSSI is read across the SPI
port for each desired output power point. Refer to the Tx Power
Monitor section for detailed information on this process and
the different power control modes.
Rx RSSI
The receive signal strength indicator (RSSI) measurement
occurs after the Rx gain is set (manual gain)/frozen(AGC). For
the power measurement to be meaningful to the BBP, the RSSI
code must be related to an absolute Rx input level (dBm) during
factory calibration. Depending on the RSSI accuracy desired,
this calibration can be a signal point calibration at a single
frequency and input power level, or can consist of a matrix of
frequencies and input power levels. The calibration signal
should be a typical burst of the associated standard. For each
receiver, there are two different RSSI read back registers. One
register stores the first power measurement (RSSI preamble).
The second register updates the power measurement at the
symbol rate (RSSI Symbol). If a calibration signal has a
preamble or symbol with constant power, the RSSI will be more
accurate and repeatable. For more details, see the Received
Signal Strength Indicator (RSSI) section. The function
ad9361_rssi_setup configures the RSSI measurement. The
AD9361
automatically takes into account the Rx gain step used
and factors it into the RSSI value. For improved RSSI accuracy
over frequency, run the Rx GM/LNA gain step calibration
before the RSSI factory calibration.
Rev. A