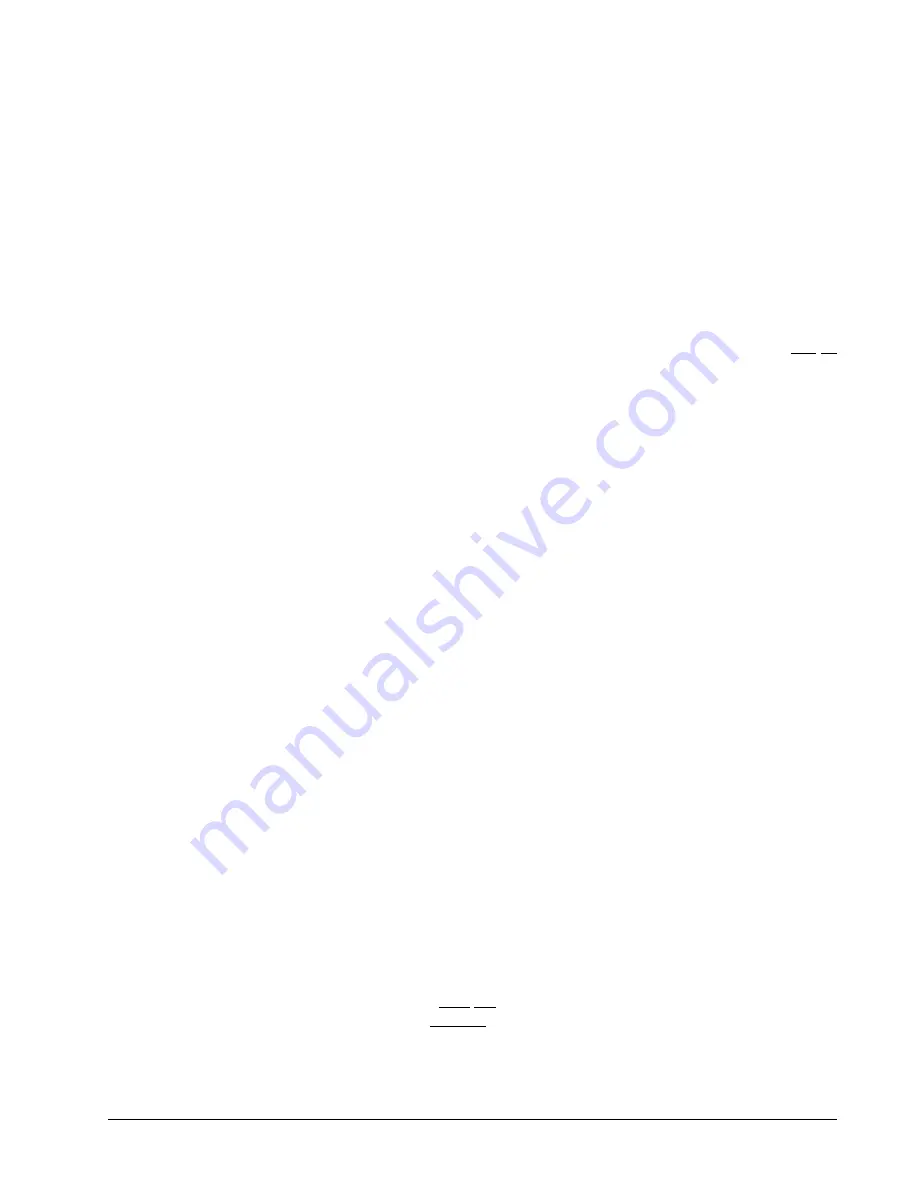
113068 - 10
www.amdry.com
45
Once the flame probe signal is detected by the burner controller module (BCM), it
waits 5-seconds to allow the pilot to stabilize and then opens the main motorized gas
valves (BCM terminal #5) in sequence.
The lower valve opens first. Upon full opening, its’ internal switch closes, enabling
the second motorized valve to open and full flame to be achieved.
If flame failure occurs within a 35-second period, the BCM will recycle the ignition
sequence once. If flame fails a second time, the system will lock out and the “FLAME
FAILURE” pilot will light.
Once main flame is established, the burner will remain in the full fire mode until the
drying set point temperature has been reached. At this point, the dryer computer will
cycle the top motorized gas valve to the closed position. The “OFF” mode will be
maintained until the dryer’s temperature falls below the drying set point temperature.
The motorized valve will then be returned to the full fire position. With voltage applied
to the motorized valve, it moves to the full fire position. “OFF” is achieved when no
voltage is applied to the motorized valve.
7) Gas Burner Start-Up
a) New gas lines are filled with air and
must be
purged before the burner will light. To do this
close the upper manual shutoff valve, but leave the pilot line shutoff open. Push in the Pilot
Test/Reset button on the cover of the BCM. This will “freeze” the ignition sequence when the
pilot flame ignites. This allows time to examine the pilot flame, and measure the flame rod signal
to the BCM.
b) Connect a pressure gauge or water tube to the pilot gas pressure tap. Start the dryer:
Follow the ignition process by referring to the “Sequence of Operation” section of this manual.
c) When the pilot flame is ignited, the pilot gas pressure should measure 3.5 inches (8.70 mb) of
water column (W.C.) for natural gas and 1.5 inches (3.73 mb) of water column (W.C.) for liquid
propane (L.P.) gas. The pilot flame
should be
about as big as a tennis ball.
d) Once the pilot has been properly set, remove the pressure gauge from the pilot line, connect a
differential pressure gauge between the main gas pressure tap (HI port) and the air pressure tap
(LO port) on the side of the gas burner box. The lines connecting the gauge to these taps
must
be
long enough to allow the gauge to sit outside of the dryer so that the burner section access
door can be closed when the dryer runs. Running the dryer with these doors open will give an
incorrect air pressure reading.
e) Once this differential gauge is installed, open the main gas shutoff valve and push the Pilot
Test/Reset button on the BCM so that the button springs out. Restart the dryer. The ignition
process should now continue to the full gas flow state. The differential gauge should read 2.5
inches (6.22 mb) of water column (W.C.) for natural gas and 1.25 inches (3.1 mb) of water
column (W.C.) for L.P. gas. If it does not, adjust the top motorized valve as described in the
Top Motorized Gas Valve
on
page 43
.
Содержание Phase 7 Gas/Steam AD-464
Страница 11: ...113068 10 www amdry com 7 B DIMENSIONS GAS AND STEAM ...
Страница 27: ...113068 10 www amdry com 23 ...
Страница 28: ...24 American Dryer Corp 113068 10 ...
Страница 62: ...ADC Part No 113068 10 05 22 12 ...