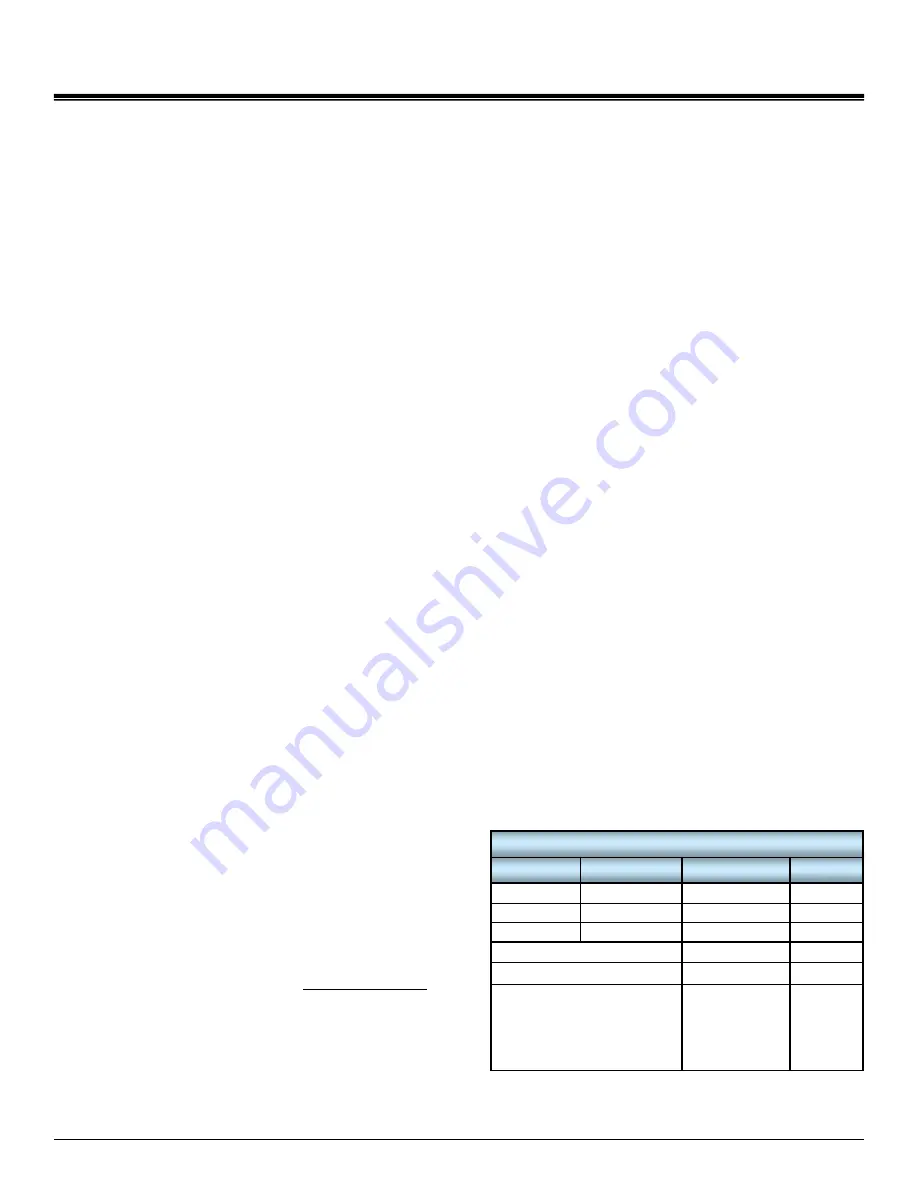
25 MAY 2009
Page 21
000744MAN-02
LINE SET INTERCONNECT TUBING
Once the outside loops have been installed and run into
the building, the piping to the ports on the unit can be
constructed. Each line set has a liquid line and a vapour line.
The vapour line is 1/2” (OD) and the liquid line is 1/2” (OD). For
horizontal loops, both lines are 1/2” (OD), reduce one of the
lines in each line set down to 3/8” (OD) before running the lines
over to the heat pump. These reduced lines will be the liquid
line for each line set.
Do a final pressure check on each line set and then
remove the pressure and cut the ends off the lines. The heat
pump has ports labeled Liquid 1 to 5 and Vapour 1 to 5. Run
each line set over to the designated ports on the heat pump.
Refer to
Diagram 000769CDG
for more information on how to
connect to the heat pump.
The tubing used for this procedure must be refrigeration
tubing (cleaned & dehydrated) suitable for the job. Every effort
must also be made to insure that the tubing does not become
contaminated during installation. We recommend that caps be
placed on the open ends of tubing immediately after cuts are
made and that these caps are only removed after all bends have
been made and the pipe fixed in its permanent location ready to
make the silver soldered joints. It is very important to keep a
refrigeration system perfectly clean and dry. Removing the caps
just prior to silver soldering will ensure minimum exposure to
the humidity in the atmosphere.
PIPE INSULATION
All line set piping inside the structure (between the
structure entry point and the heat pump) should be insulated
with 3/8” thick closed cell pipe insulation to prevent
condensation and dripping onto floors or walls during the
heating season. It can be slid onto the capped tubing without
having to slice it down the side. Ensure that any joints in in the
line sets are accessible for leak testing.
Liquid and Vapour ports and any remaining exposed tubing
should be insulated with 3/8” thick closed cell pipe insulation
once the silver soldering and pressure testing is complete.
Ensure that all individual pieces of pipe insulation are glued to
each other so there are no air gaps.
SILVER SOLDERING LINE SETS
Once all the line sets have been routed, insulated and
fastened in place, the connections to the heat pump ports can
be made. Remove the pressure from the heat pump and cut the
ends off of the Liquid and Vapour ports. Remove the caps from
the line set tubing. The line sets can be connected to the ports
on the heat pump using couplings, or alternately the tubing can
be "swaged". The joints should be silver soldered with 5%
silfos.
AMERICAN DREAM Geothermal absolutely requires
that dry nitrogen be bled through the system during all
silver soldering procedures so that no oxidation occurs on
the inside of the copper tubing.
The service ports on the unit
can be used to connect the nitrogen with a refrigeration
manifold.
If necessary, a damp clothe can be wrapped around the
each of the ports to prevent melting the grommet when silver
soldering. Ensure that no water enters any of the ports or
tubing.
PRESSURE TESTING
Once all connections are complete, the system should be
pressure tested to
100PSIG (690kPa)
with dry nitrogen. Check
all joints at the unit and any made in the interconnect tubing for
leaks using soap suds, Spray nine, etc. It is important not to
bypass this step as vacuuming the system with a leak will be
impossible and attempting to do so will introduce moisture into
the system, making the vacuum process take much longer than
if the leak had been found and repaired first.
VACUUMING THE SYSTEM
Remove the pressure from the system and connect the
vacuum pump to the refrigeration manifold. Tighten all hose
connections, open the valves on the manifold and start the
vacuum pump.
Vacuum the system until the reading on an electronic
vacuum gauge remains below 500 microns for a period of 5
minutes after the vacuum pump is shut off and the system
sealed.
CHARGING THE SYSTEM
Once the system has been vacuumed, refrigerant can be
added by weighing in 1/3 of the prescribed refrigerant charge
into the low side of the system. Start the heat pump in the
heating mode and continue to add refrigerant as a liquid at a
rate of no more than 1 lb. per minute until the prescribed charge
is reached.
Alternately, before the machine is started, the entire
charge can be weighed into the system through the high side of
the system.
TABLE 16
shows the typical charge per unit size.
This allows for:
20ft of distance (40ft of pipe) interconnect tubing from
the unit to the wall,
20ft of distance from the wall to the borehole /trench,
a standard loop (100ft borehole or 150ft trench).
Additional refrigerant is required as per
TABLE 16
if the
installation exceeds these parameters.
Loop Connection & Charging
TABLE 16 - Charge Chart
Model
Size (tons)
Lbs.
kg
45
3
12
5.4
55
4
16
7.3
65
5
20
9.1
Extra loop (borehole)
1
0.5
Extra loop (trench)
1.5
0.7
Extra distance to borehole
Extra depth of borehole
Extra distance to trench
Extra length of trench
Extra distance in structure
0.1oz per foot
0.003
Содержание Copper Series
Страница 9: ...25 MAY 2009 Page 9 000744MAN 02...
Страница 10: ...Page 10 000744MAN 02 25 MAY 2009...
Страница 13: ...25 MAY 2009 Page 13 000744MAN 02...
Страница 16: ...Page 16 000744MAN 02 25 MAY 2009...
Страница 18: ...Page 18 000744MAN 02 25 MAY 2009...
Страница 19: ...25 MAY 2009 Page 19 000744MAN 02...
Страница 20: ...Page 20 000744MAN 02 25 MAY 2009...
Страница 22: ...Page 22 000744MAN 02 25 MAY 2009...
Страница 45: ...25 MAY 2009 Page 45 000744MAN 02 REFRIGERATION CIRCUIT DIAGRAMS...
Страница 46: ...Page 46 000744MAN 02 25 MAY 2009 REFRIGERATION CIRCUIT DIAGRAMS continued...
Страница 47: ...25 MAY 2009 Page 47 000744MAN 02 REFRIGERATION CIRCUIT DIAGRAMS continued...
Страница 53: ...25 MAY 2009 Page 53 000744MAN 02 ELECTRICAL DIAGRAMS 230 1 60...
Страница 54: ...Page 54 000744MAN 02 25 MAY 2009 ELECTRICAL DIAGRAMS 230 1 60 continued...
Страница 55: ...25 MAY 2009 Page 55 000744MAN 02 CASE DETAILS Front View Back View Left Side View Right Side View...
Страница 56: ...Page 56 000744MAN 02 25 MAY 2009 Top View Size 2 3 4 Ton CASE DETAILS continued Top View Size 5 Ton...
Страница 58: ...Page 58 000744MAN 02 25 MAY 2009...
Страница 59: ...25 MAY 2009 Page 59 000744MAN 02...