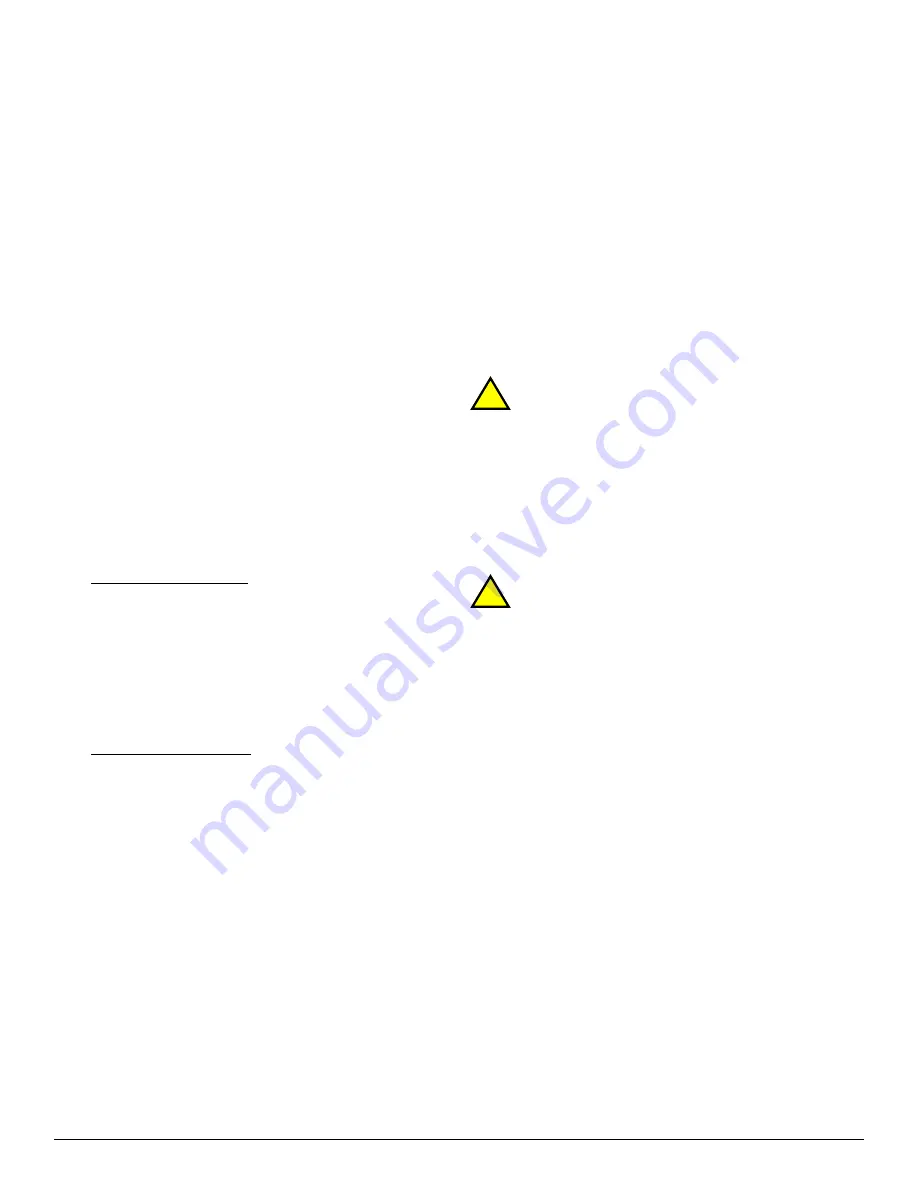
Page 8
000744MAN-02
25 MAY 2009
values can be found in
APPENDIX A
.
Units are shipped with the
MED
position selected for
nominal air flow. The air flow can be further reduced by 15% by
making a dry contact across AR
1
and AR
2
on the terminal strip.
This can be used for applications that have multiple zones, or
retrofits with undersized ductwork, to help reduce air flow noise
in the ductwork. It is recommended that airflow reduction only
be used with the High or Max air flow setting. Care should be
taken to ensure that the unit does not trip a safety control in
heating or cooling mode if the 15% reduction is used in conjunc-
tion with the Med or Low air flow setting.
CONTROL TRANSFORMER
The low voltage controls for all models are powered by a
100VA transformer with primary and secondary fuses for circuit
protection. Should a fuse blow, determine the problem and rec-
tify it before replacing the fuse.
SAFETY CONTROLS
The heat pump has two built in safety controls which are
designed to protect the unit from situations which could damage
it should the operation of the refrigeration circuit fall outside the
allowable operating range.
A. Low Pressure Control
The low pressure control monitors the compressor suction
pressure and will shut the compressor down if the refrigerant
evaporating pressure becomes too low.
There only reason this control would activate in response
to the operating conditions of the unit in the heating mode
would be due to a ruptured loop, causing a low refrigerant
charge. Any other low pressure trips would be due to a fault in
the unit.
B. High Pressure Control
The high pressure safety control monitors the compressor
discharge pressure and will shut the compressor down if the
condensing pressure becomes too high.
There are (3) main reasons why this control would activate
in response to the operating conditions of the unit while operat-
ing in heating mode:
1. Low or no airflow (or water flow).
2. High return air temperature (or water temperature).
3. Dirty air coil due to poor filter maintenance.
Each of the controls are auto-reset controls. There is also
a manual reset high pressure control should the control board
be faulty and fail to disengage the compressor. It can be reset
by pressing the rubber button on the end of it. It is electrically
located between the Y output of the control board and the com-
pressor contactor coil.
The control board (see next section) monitors the pressure
controls and shuts the compressor off immediately for a set pe-
riod of time (adjustable) should there be a fault. The counter for
the safety control in question will be increased by 1. The LED
indicator for the control will flash until the control is reset as the
pressures equalize in the unit. The unit may restart after the
timer period has expired. Should the unit trip on the safety con-
trol again , the compressor will once again shut down and the
counter will be incremented by one again. Each time this occurs
the count is incremented until the counter reaches the max
value (default is 3) at which point a permanent lockout will occur
if this occurred within a set period of time (default 6 hours) and
the compressor cannot be started again until the control board is
reset by shorting the reset pins together or turning the power off
and on again. The lockout count is decreased after a set period
of time (default 6 hours) if there are no more occurrences.
If the control board enters permanent lockout mode there
is a serious problem with the system and it must be rectified if
the unit is to maintain good service.
DOMESTIC HOT WATER
CONNECTIONS
A typical piping diagram for a pre-heat tank configuration
can be found in
drawing 000484PDG
at the end of this
section. Be sure to note the position of the check valve
and the direction of water flow. Other configurations are possi-
ble, and there may be multiple units tied together in larger build-
ings.
WARNING: USE ONLY COPPER LINES TO
CONNECT THE DESUPERHEATER. TEMPERATURES
COULD REACH 200F SHOULD THE DHW
CUTOUT SWITCH FAIL, POTENTIALLY RUPTURING
PEX PIPING.
Ensure the tank is filled with water and under pressure
before activating the heat pump. Slightly loosen the boiler
drain on the DHW Out pipe to allow air to escape from the
system before the unit is started. This step will make certain that
the domestic hot water circulator in the unit is flooded with water
when it is started.
CAUTION: the domestic hot water pump is water lubricated;
damage will occur to the pump if it is run dry for even a
short period of time.
Connect the brown wire with the blue insulated terminal to
L1 of the compressor contactor.
Ensure the power is off
when connecting the wire.
The DHW loop may have to be purged of air several times
before good circulation is obtained. A temperature difference
between the DHW In and DHW Out can be felt by hand when
the circulator pump is operating properly.
For the pre-heat tank setup, the final tank should be set to
140°F(60°C),
unless local code requires a higher setting.
The
pre-heat tank does not require electric elements. This setup
takes full advantage of the desuperheater as it is the sole heat
provider to the pre-heat tank. The desuperheater remains active
during the compressor runtime until the pre-heat tank has been
completely heated by the desuperheater alone. This setup is
more energy efficient than a single tank setup.
CAUTION: If two (2) shut-off valves are located on the do-
mestic hot water ines as shown in the diagram, a pressure
relief valve must be installed to prevent possible damage to
the domestic hot water circulator pump should both valves
be closed.
!
!
Содержание Copper Series
Страница 9: ...25 MAY 2009 Page 9 000744MAN 02...
Страница 10: ...Page 10 000744MAN 02 25 MAY 2009...
Страница 13: ...25 MAY 2009 Page 13 000744MAN 02...
Страница 16: ...Page 16 000744MAN 02 25 MAY 2009...
Страница 18: ...Page 18 000744MAN 02 25 MAY 2009...
Страница 19: ...25 MAY 2009 Page 19 000744MAN 02...
Страница 20: ...Page 20 000744MAN 02 25 MAY 2009...
Страница 22: ...Page 22 000744MAN 02 25 MAY 2009...
Страница 45: ...25 MAY 2009 Page 45 000744MAN 02 REFRIGERATION CIRCUIT DIAGRAMS...
Страница 46: ...Page 46 000744MAN 02 25 MAY 2009 REFRIGERATION CIRCUIT DIAGRAMS continued...
Страница 47: ...25 MAY 2009 Page 47 000744MAN 02 REFRIGERATION CIRCUIT DIAGRAMS continued...
Страница 53: ...25 MAY 2009 Page 53 000744MAN 02 ELECTRICAL DIAGRAMS 230 1 60...
Страница 54: ...Page 54 000744MAN 02 25 MAY 2009 ELECTRICAL DIAGRAMS 230 1 60 continued...
Страница 55: ...25 MAY 2009 Page 55 000744MAN 02 CASE DETAILS Front View Back View Left Side View Right Side View...
Страница 56: ...Page 56 000744MAN 02 25 MAY 2009 Top View Size 2 3 4 Ton CASE DETAILS continued Top View Size 5 Ton...
Страница 58: ...Page 58 000744MAN 02 25 MAY 2009...
Страница 59: ...25 MAY 2009 Page 59 000744MAN 02...