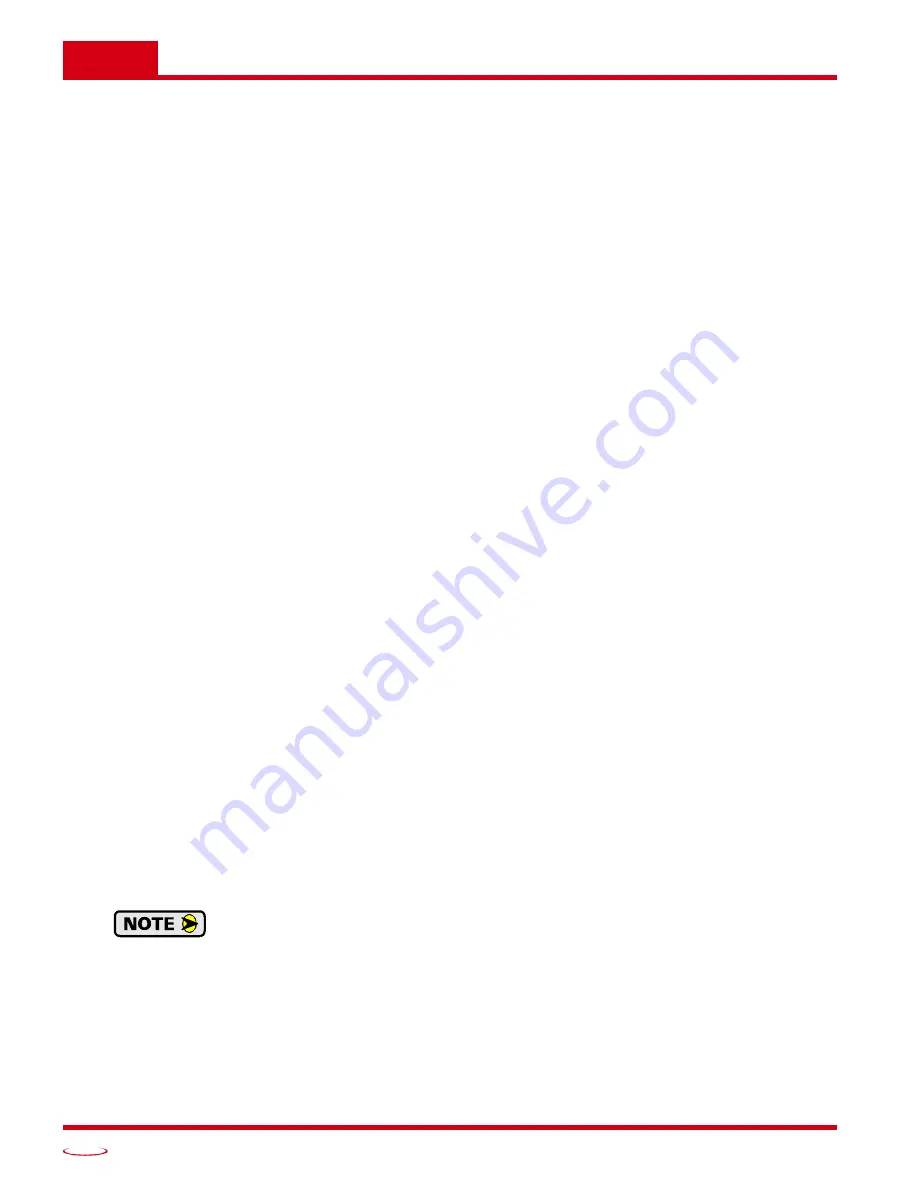
MOTION CONTROL
ADVANCED MICRO CONTROLS INC.
2
24
Electronic Gearing (continued)
How It Works (continued)
Encoder position data can be trapped while in Electronic Gearing mode by configuring Input 3 as a Capture
Encoder Position input.
Controlled Stop Conditions
h
The encoder stops moving.
h
Electronic Gearing moves cannot be brought to a controlled stop by using the Hold Move control bit in
the Network Input Data.
Immediate Stop Conditions
h
The Immediate Stop bit makes a 0
p
1 transition in the Network Input Data.
h
A positive transition on an input configured as a E-Stop Input.
h
A CW or CWW Limit Switch is reached.
Advanced Ratio Control
The ELGearing Multiplier and Divisor values give you a great deal of control over the ratio of motor turns per
encoder turn, but you can achieve even finer control by adjusting the Encoder Pulses per Turn parameter and
the Steps per Turn parameter.
The Z pulse is not used to correct the encoder position once per turn, so you can actually program the encoder
Pulses per Turn to any value you want within its valid range. For example, if your encoder outputs 4,096
pulse per turn and you set the Encoder Pulses per Turn parameter to 8,192, you will have built a 2:1 gear
down into your system before applying the ELGearing Multiplier and Divisors. (Two rotations of the
encoder = 8,192 counts = 1 motor rotation) Similarly, you can adjust the Steps per Turn value to adjust the
ratio as well.
This technique allows you to set a median gear ratio in your system that you can adjust on-the-fly by using the
ELGearing Multiplier and Divisor parameters.
Stall Detection
The final feature available when using an encoder is stall detection. The encoder must be mounted on the
motor controlled by the SD17060E, which means that you cannot use Stall Detection when using the Elec-
tronic Gearing feature. When Stall Detection is enabled, the SD17060E monitors the encoder inputs for
changes while a move is in progress. If the encoder inputs do not change as expected, the move stops and an
error bit is reported to your host controller.
Idle Current Reduction
Idle Current Reduction allows you to prolong the life of your motor by reducing its idling temperature. Val-
ues for this parameter range for 0% (no holding torque when idle) to 100%.
Idle current reduction should be used whenever possible. By reducing the current, you are reducing the I
2
R
losses in the motor. Therefore, the temperature drop in the motor is exponential, not linear. Therefore, even
a small reduction in the idle current can have a large effect on the temperature of the motor.
Note that the reduction values are “to” values, not “by” values. Setting a motor current to 4
amps and the current reduction to 25% will result in an idle current of 1 amp.