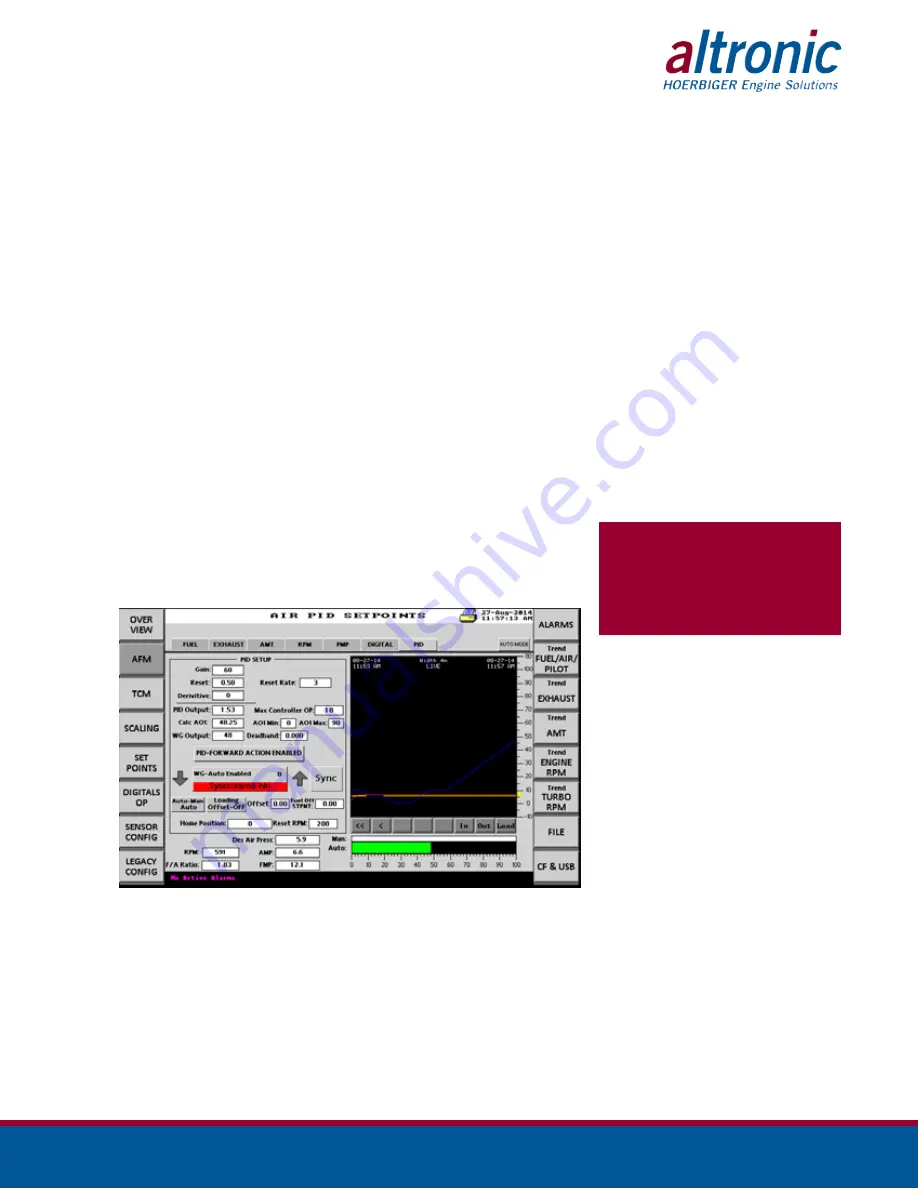
EPC-250 IOI 6-18 All rights reserved © ALTRONIC, LLC 2018
18
10.0 AIR PID SETPOINTS
PID control continuously compares the process variable to the control setpoint
and calculates an error value. The error is used to calculate the value of the
control variable.
The control variable has three components:
P
roportional Control,
I
ntegral Control, and
D
erivative Control
PID
control is developed from complex mathematics; a full explanation is
beyond the scope of this manual, but the theory can be simplified as in the
following subsections.
Proportional Control (Gain)
The proportional component of the control variable is the main output of the
PID control. It calculates an output amount that is proportional to the error.
The larger the error, the larger the proportional component will be (in an at-
tempt to make the process variable equal to the control setpoint). Proportional
control alone cannot eliminate all the error.
Integral Control (Reset)
The integral control component is proportional to both the error and the length
of time the error exists. The larger the error and the longer the error exists,
the larger the integral component will be (in an attempt to make the process
variable equal to the control setpoint). The integral control component is used
to eliminate all remaining error.
Derivative Control
The derivative control component is proportional to the rate of the change
of the error. The faster the process variable moves away from the control
setpoint, the larger the derivative control component will be (in an attempt to
quickly return the process variable to equal the control setpoint).
10.1
Gain
The EPC-250 uses proportional control, which is the inverse of gain. Lowering
the proportional value decreases the controller output. Inversely, increasing
the gain value increases the controller output. A typical starting gain value is
60 to 100.
10.2
Reset
The Reset value adds to the gain control value. A typical reset value is 0.5.
10.3
Derivative
The Derivative helps to minimize over shoot. The typical derivative range is 0
to 10. Increasing the number increases controller sensitivity.
CAUTION: It is recommended that all
changes to the PID parameters be
done by a qualified instrument techni-
cian. Incorrect settings can cause
faulty operation or unit malfunction/
damage.