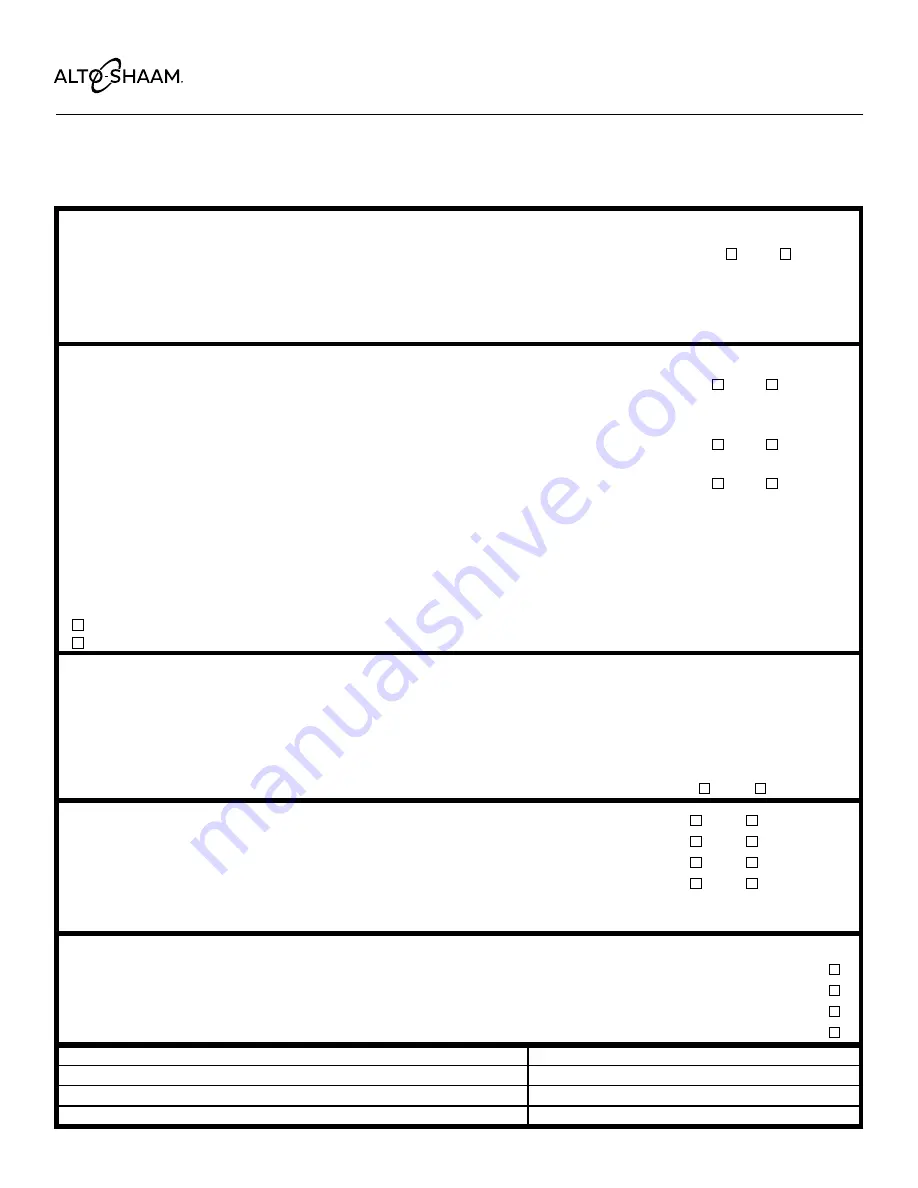
MN-29805 • Rev 10 • 06/17 • Combitherm CT Express Installation Manual
19
Installation
Use this list as a final check of appliance installation conformance
Damage directly attributed to improper set up, installation, or cleaning can invalidate warranty claims
Clearances:
Left: 4" (102mm) — 18" (457mm) recommended service access
8" (203mm) from heat or steam producing equipment
Right: 4" (102mm) non‑combustible surfaces
Rear: 4" (102mm) for plumbing
Top: 20" (508mm) for air movement
Bottom: 4" (102mm) for air movement
Are all clearance
requirements met?
Yes
No
If no, explain: ____________________________
____________________________________________
Water Supply And Drains:
Verify hook up of two (2) cold water lines: treated and untreated
water with a 3/4" (19mm) G inside diameter connection supply line
Verify inlet water pressure is at a minimum of 30 PSI (200 kPa)
dynamic Maximum water pressure is not to exceed 90 PSI (600 kPa)
static Verify drain diameter of 1‑1/2" (40mm) with a positive
descending slope, and with a 2" (51mm) air gap which is free of
obstructions before connection to the site drain Verify 1/8" (3 2mm)
pitch to 10' (305cm) of drain line Materials must withstand
temperatures up to 200°F (93°C)
NOTICE:
Alto‑Shaam has listed Water Quality Requirements in the installation manual for this equipment It is the
responsibility of the end user to have the water connected to this appliance tested to ensure these standards
are met before putting the appliance into use Failure to meet these standards will void the warranty if
damage to the appliance is found to be related to water quality
Inspect water connections inside the combi
Check all lines and connections for leaks, both inside and outside the combi
Are both water supply lines
properly connected?
Yes
No
If no, explain: ________________________________
Is a filter system installed
on this appliance?
Yes
No
Store has seen this
recommendation:
Yes
No
Signature of store representative:
________________________________________________
Physical Condition:
*Reference installation instructions for complete information
✓
Bottom of appliance has been checked for damage due to improper positioning on site
Verify all gaskets and hoses are in place and function properly
Verify the installation of drip pans*, racks, shelves, drain screen, spray hose*
Verify the appliance is level and installed on a solid, water resistant surface
Electrical Connections:
Verify electrical power requirements for appliance
Verify voltage at terminal block
Check all terminals for tightness
Line voltage at terminal block (to ground):
Line 1: __________ Line 2: __________ Line 3: __________
Line voltage (phase to phase): Line 1 to 2: __________
Line 2 to 3: __________
Line 3 to 1: __________
Electrical supply line size: _____________________________
All electrical terminals tight:
Yes No
Voltage:
______________
Phase:
______________
Breaker size:
______________
Control Board Connections & Operation:
ExpressTouch
: With the power on, press the Tool Box
icon, then the Settings icon to access software version
in the upper left corner
All board connections tight: Yes No
All functions are displayed: Yes No
All functions on control operate: Yes No
Appliance operates in all modes: Yes No
If no, explain: _______________________________________________
_______________________________________________________________
RB__________________
Record software version: DB__________________
Service Agency:
Start‑Up Date:
Installation Name:
Model No :
Serial No :
Tech Signature:
Customer Signature:
CT Express™ Checklist