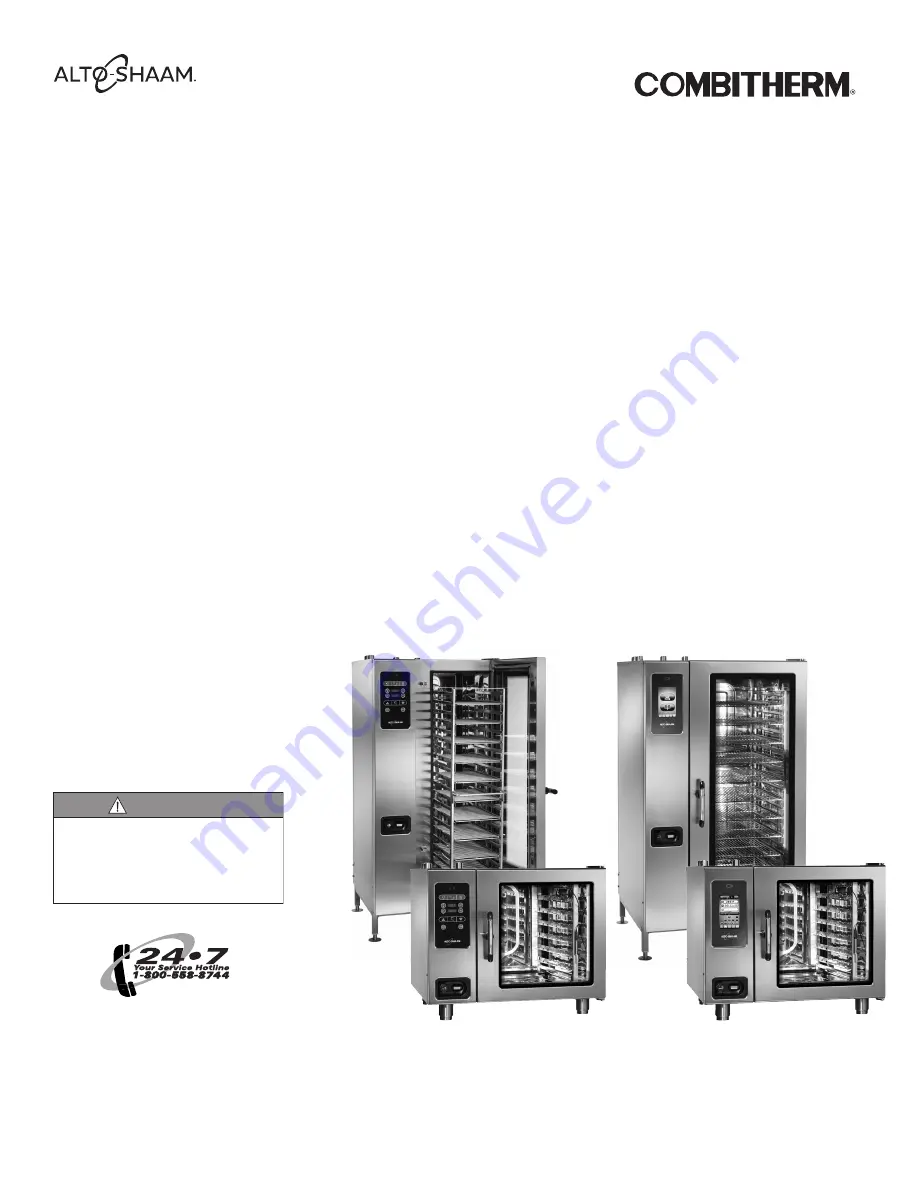
MN-35949
•
Rev 07
•
01/20
•
Combitherm® CT PROformance™ and CT Classic™ Series Technical Service Manual
SERVICE MANUAL
Operation, Maintenance, Troubleshooting, and Wiring Diagrams
WARNING
Improper installation, alteration, adjustment, service,
cleaning, or maintenance could result in property
damage, severe injury, or death.
Read and understand the installation, operating and
maintenance instructions thoroughly before installing,
servicing, or operating this equipment.
CTC6-10E
CTC10-10E
CTC7-20E
CTC10-20E
CTC20-10E
CTC20-20E
CTC6-10G
CTC10-10G
CTC7-20G
CTC10-20G
CTC20-10G
CTC20-20G
CTP6-10E
CTP10-10E
CTP7-20E
CTP10-20E
CTP20-10E
CTP20-20E
CTP6-10G
CTP10-10G
CTP7-20G
CTP10-20G
CTP20-10G
CTP20-20G
CT CLASSIC™
CT PROFORMANCE™
Содержание COMBITHERM CTP6-10e
Страница 4: ...4 MN 35949 Rev 07 01 20 Combitherm CT PROformance and CT Classic Series Technical Service Manual ...
Страница 100: ...100 MN 35949 Rev 07 01 20 Combitherm CT PROformance and CT Classic Series Technical Service Manual Service Log Notes ...
Страница 101: ...MN 35949 Rev 07 01 20 Combitherm CT PROformance and CT Classic Series Technical Service Manual 101 Service Log Notes ...