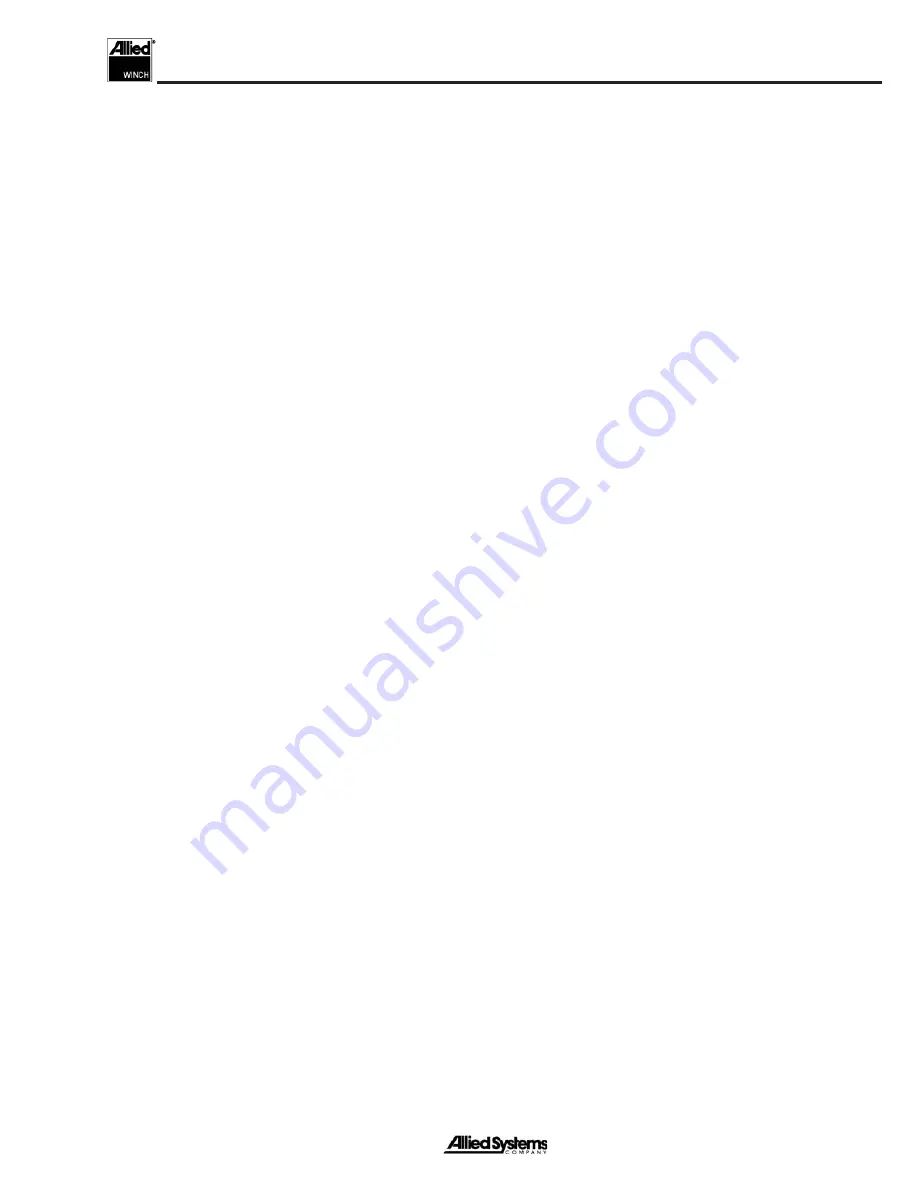
Section 1
1 - 27
Sequence of Operation, High-Performance Winch - HI-
SPEED LINE-OUT
The operator pushes the control lever forward, which
sends pilot control pressure to the direction control valve
and the brake release valve. Oil fl ows from the pump
supply line into the direction control spool cartridge and
continue to the inlet B port of the hydraulic motor. Pres-
sure builds from resistance against the counterbalance
valve, mechanical, and volumetric resistance. This pres-
sure supply communicates through a check valve to pilot
the counterbalance valve open until the inlet pressure
falls below a set value and the counterbalance valve
closes. Similarly, the same pressure is communicated
to the tractor pump load sense controller, and the pump
displacement is increased or decreased depending on
the load induced pressure. Oil fl ows through the motor
back through the direction control spool and to the trac-
tor reservoir. Simultaneously, pilot control pressure at the
brake valve is connected to the brake release port, and the
brake is fully released. Low pressure case drain oil fl ows
from the hydraulic motor back to the tractor reservoir. This
condition drives the winch drum in
LINE-OUT
.
When the winch is operated in
LINE-OUT
, and a load
pulls line from the winch, pressure builds on the A port
of the motor up to the load sense relief setting. When
pressure on the A port of the motor exceeds 3500 psi,
the load sense relief valve opens. The load sense pres-
sure signal decreases, and the tractor pump strokes back
reducing displacement so pressure at the hydraulic motor
decreases a corresponding amount. If pressure on the
inlet B side of the hydraulic motor drops below the pilot
setting of the counterbalance valve, the counterbalance
valve closes and acts as a relief valve on the A port of the
hydraulic motor. The valve relieves when pressure on the
A port reaches 4500 psi.
When the winch is operated in
LINE-OUT
, and a load
pulls line from the winch, pressure builds on the A port
of the motor up to the load sense relief setting. When
pressure on the A port of the motor exceeds 3500 psi,
the load sense relief valve opens. The load sense pres-
sure signal decreases and the tractor pump strokes back
reducing displacement so pressure at the hydraulic motor
decreases a corresponding amount. If pressure on the
inlet B side of the hydraulic motor drops below the pilot
setting of the counterbalance valve, the counterbalance
valve closes and acts as a relief valve on the A port of the
hydraulic motor. The valve relieves when pressure on the
A port reaches 4500 psi.
When the operator depresses the
HI-SPEED
switch, the
HI-SPEED
solenoid valve in the logic manifold opens, and
pilot control pressure is communicated to the
HI-SPEED
spool in the hydraulic motor. The spool shifts to close half
of the vein ports in the motor. Full pump fl ow now fl ows
through the motor at half displacement thus increasing
the output rpm.
Pressure on the A port of the hydraulic motor is sensed by
a pressure switch in the direction control manifold. When
pressure at the switch reaches 1750 psi, the switch opens,
and the circuit to the
HI-SPEED
solenoid valve is broken.
Pressure at the
HI-SPEED
spool in the hydraulic motor is
vented back to the reservoir, and the spool spring biases
back to the standard speed position. The winch remains
in standard speed until the operator depresses the
HI-
SPEED
switch again and load induced pressure on the
motor remains below 1750 psi.
Содержание Allied H6G Series
Страница 8: ...vi Notes...
Страница 25: ...Section 1 1 17 Intentionally Blank...
Страница 26: ...General 1 18 Figure 1 19 Sequence of Operation BRAKE ON...
Страница 28: ...General 1 20 Figure 1 20 Hydraulic System LINE IN...
Страница 30: ...General 1 22 Figure 1 21 Hydraulic System HI SPEED LINE IN...
Страница 32: ...General 1 24 Figure 1 22 Hydraulic System LINE OUT...
Страница 34: ...General 1 26 Figure 1 23 Hydraulic System HI SPEED LINE OUT...
Страница 36: ...General 1 28 Figure 1 24 Hydraulic System BRAKE OFF...
Страница 38: ...General 1 30 Figure 1 25 Hydraulic System FREESPOOL...
Страница 40: ...General 1 32 Notes...
Страница 41: ...Section 1 1 33 Figure 1 26 H6GH B Schematic High Performance Winch H6GH B...
Страница 42: ...General 1 34 Figure 1 27 H6GH E Schematic High Performance Winch H6GH E...
Страница 43: ...Section 1 1 35 H6GH J Figure 1 28 H6GH J Schematic High Performance Winch...
Страница 44: ...General 1 36 H6GT E Figure 1 29 H6GT E Schematic Rescue Winch...
Страница 51: ...Section 2 2 7 Notes...
Страница 52: ...Troubleshooting 2 8 Notes...
Страница 60: ...Service 3 8 Notes...
Страница 83: ...Section 4 4 23 12 Remove the spool asssembly...
Страница 119: ...Section 4 4 59 Notes...
Страница 120: ...Repairs 4 60 Notes...
Страница 121: ......