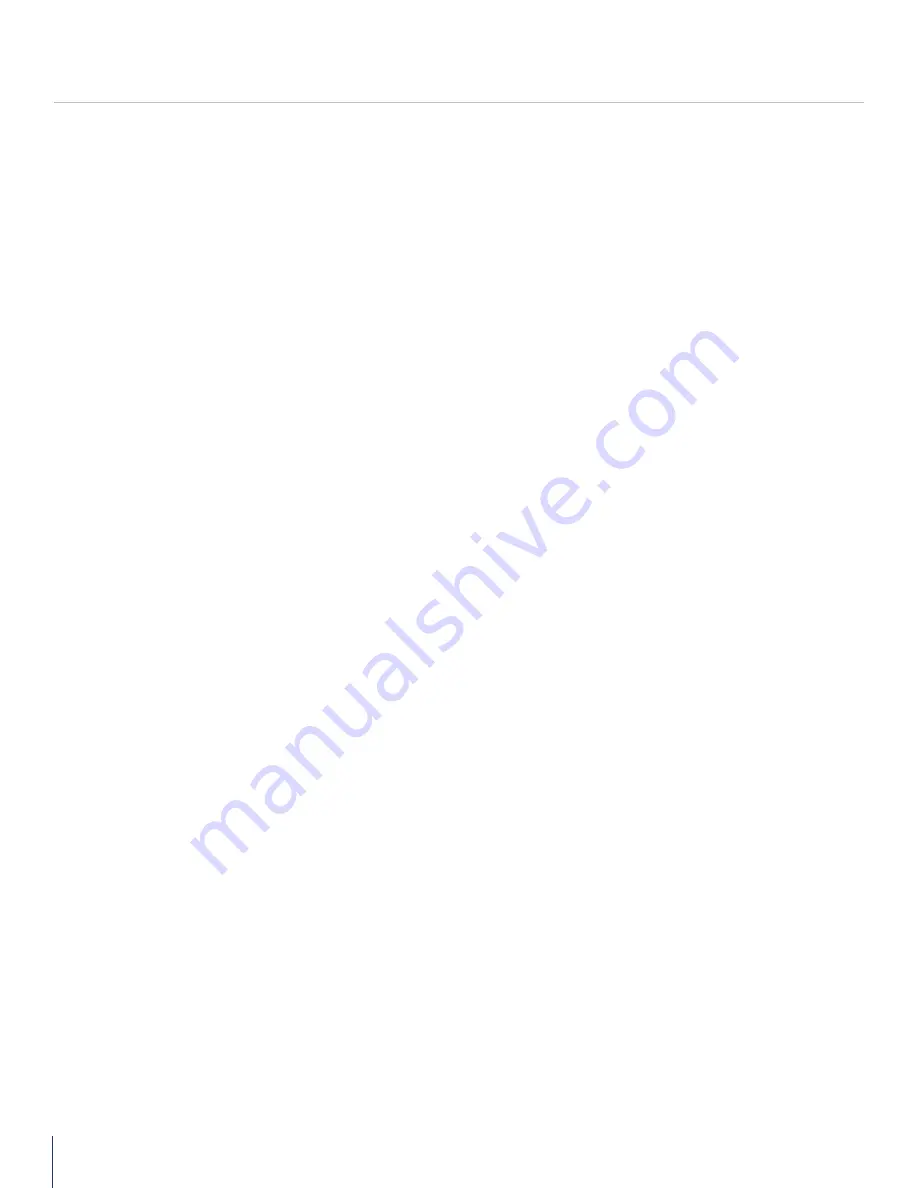
ABP Series |
Blower Purge Desiccant Air Dryer
14
COMPONENT OPERATION
Adsorption
NOTICE:
The heated regenerative desiccant dryer is not
designed to remove bulk liquid, therefore a cyclone separator
or a mist eliminator, not provided with the system, must
be installed to remove bulk-liquid condensate from the air
compressor’s aftercooler.
The bulk-liquid free compressed air from the customer-
supplied cyclone separator is delivered to the dryer through
a coalescing pre-filter located upstream of the dryer. The pre-
filter (optional with dryer) cleans by removing particles and
liquid mist down to a residual oil content of 0.03 ppm, based
on an inlet concentration of 3 ppm. The coalesced liquid is
removed from the pre-filter housing by the zero air-loss drain
valve.
The airflow continues through the inlet control butterfly
valve into the bottom of the on-line desiccant chamber. A
desiccant support and distribution screen at the chamber inlet
distributes the flow evenly throughout the desiccant bed. The
moist air flows upward through the desiccant bed where it is
dried. The dried air exits the desiccant chamber through the
upper flow distributor and retaining screen at the top of the
vessel. Before leaving the system to enter the compressed
air distribution system, the air is purified further by an after
filter (optional with dryer) that removes fine dust and abraded
desiccant.
Regeneration
While one desiccant chamber is on-line drying compressed air,
the other chamber is off-line and depressurized for desiccant
regeneration. The inlet valve to the off-line chamber closes
and the vessel depressurizes through an exhaust valve and
silencer to the atmosphere.
When the vessel low pressure switch indicates successful
depressurization, an atmospheric pressure blower is started
to provide regeneration air to the off-line desiccant bed. The
ambient regeneration air, heated to 400° F by an electric
resistance heater, is controlled by a manual valve installed at
the blower discharge or a slide gate damper at blower intake.
The heated air is directed downward through the off- line
wet desiccant bed and vented from the system through the
regeneration air outlet valve in the lower piping manifold.
When the desiccant bed is fully regenerated, 175 minutes
maximum heating time, the electric heater is turned off. The
blower is then turned off 6 minutes later, for heater cool-
down, and isolated by check valves.
The regeneration air heater outlet temperature is monitored
by a thermocouple and PLC control system. A thermocouple is
also installed in the regeneration air outlet manifold. If preset
temperature of 200°F is sensed at the regeneration air outlet
prior to the end of the maximum heating time, the heater will
be turned off early to save energy.
A heater sheath over-temperature switch is provided on each
heater circuit to protect the heater elements in the event of a
control fault or heating element failure.
After the desiccant is thermally regenerated, a portion of dry
outlet air, controlled by the manual purge flow adjusting valve,
is expanded to atmospheric pressure and passed through the
off-line vessel to cool the desiccant. The airflow direction is
downward through the off-line vessel during depressurization,
heating and cooling which prevents fluidization of the
desiccant and greatly reduces abrasion and attrition of the
desiccant granules. The cooling phase continues for 45
minutes (maximum) or until the temperature switch in the
lower manifold detects 120°F. The regeneration outlet valve is
closed and the vessel is re-pressurized with dry air. When full
line pressure is achieved in the regenerated vessel, which is
verified by pressure sensors, the inlet valve is opened and the
two chambers run in parallel mode for 10 minutes.
The two vessels are switched-over at the end of the drying
period. The regenerated bed is placed on-stream and
the water laden bed of desiccant is taken off-stream for
regeneration.
The manual purge flow adjusting valve must be set at start-
up to allow the dryer to re-pressurize in 4 minutes. This will
ensure that the correct purge flow is being used for cooling
and that full system pressure is achieved prior to change over.
Содержание ABP Series
Страница 48: ...ABP Series Blower Purge Desiccant Air Dryer 48 SERVICE NOTES DATE SERVICE PERFORMED NOTES ...
Страница 49: ...Blower Purge Desiccant Air Dryer ABP Series 49 SERVICE NOTES DATE SERVICE PERFORMED NOTES ...
Страница 50: ...ABP Series Blower Purge Desiccant Air Dryer 50 SERVICE NOTES DATE SERVICE PERFORMED NOTES ...