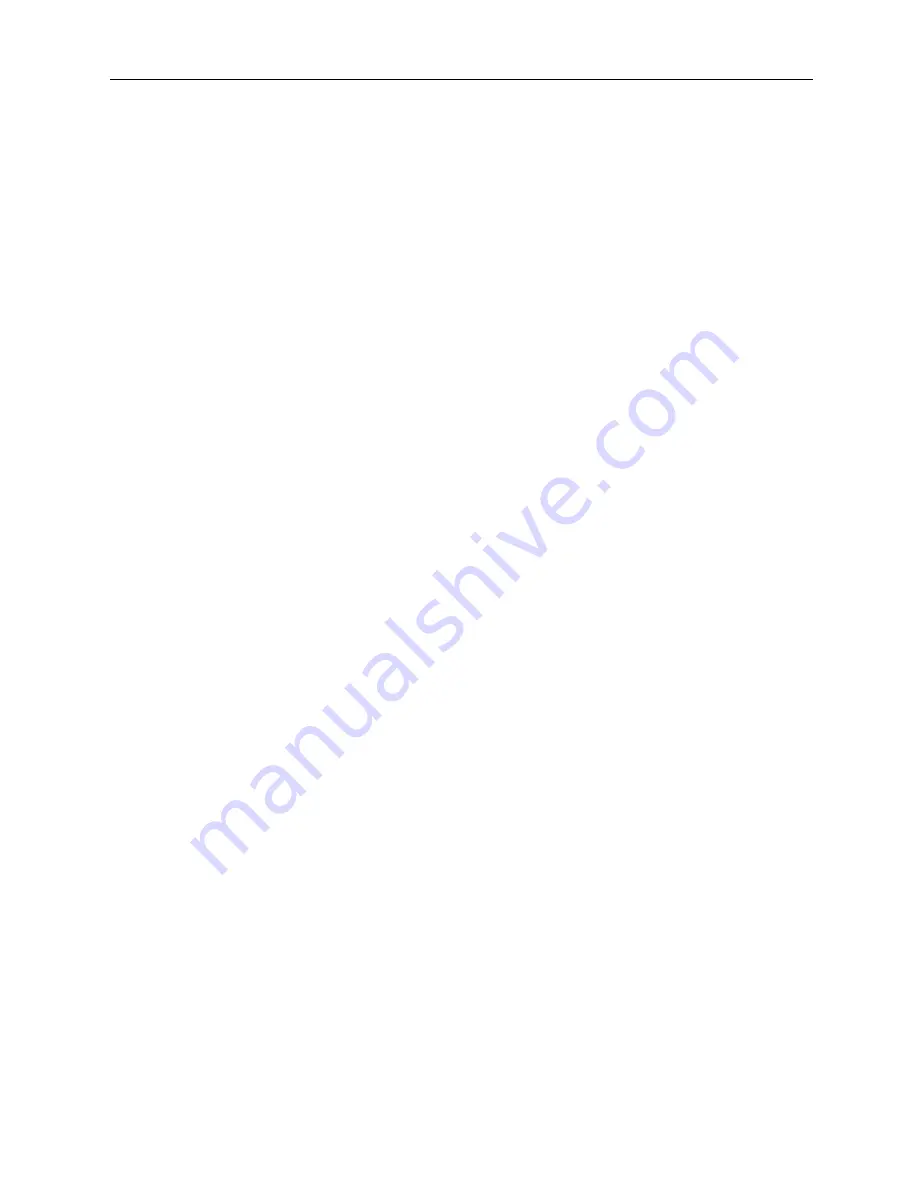
Technical Support 83
4510012 - REV F – 220621
Technical Support
For assistance with installing, operating, or maintaining the STC-WSN GEN-S, contact your
authorized AFM reseller or AFM Technical Support.
Phone: 714-974-9006
Fax: 763-795-8867
Email: [email protected]
Web: www.afmsleeves.com
Thanks again for your purchase of AFM products. We are pleased to be a part of your shrink
sleeving needs.
Содержание STC-WSN300-2M
Страница 1: ...WSN GEN S Steam Heat Shrink Tunnel User Guide ...
Страница 2: ...2 Abbreviations 4510012 REV F 220621 ...
Страница 8: ...8 Abbreviations 4510012 REV F 220621 ...
Страница 28: ...28 Introduction 4510012 REV F 220621 STC WSN600 2M GEN S Top View Front View Exit View Entry View ...
Страница 66: ...66 Troubleshooting 4510012 REV F 220621 ...
Страница 67: ...Electrical Schematics 67 4510012 REV F 220621 Electrical Schematics Complete System WSN GEN S ...
Страница 68: ...68 Electrical Schematics 4510012 REV F 220621 Boiler ...
Страница 72: ...72 Parts List 4510012 REV F 220621 Exploded Diagrams Stand Drawing Number YS130EX2 01 ...
Страница 74: ...74 Parts List 4510012 REV F 220621 Tunnel Drawing Number YS130EX2 02 ...
Страница 78: ...78 Parts List 4510012 REV F 220621 Boiler ...
Страница 79: ...Parts List 79 4510012 REV F 220621 Inside Boiler Electrical Cabinet ...
Страница 84: ...84 Technical Support 4510012 REV F 220621 ...