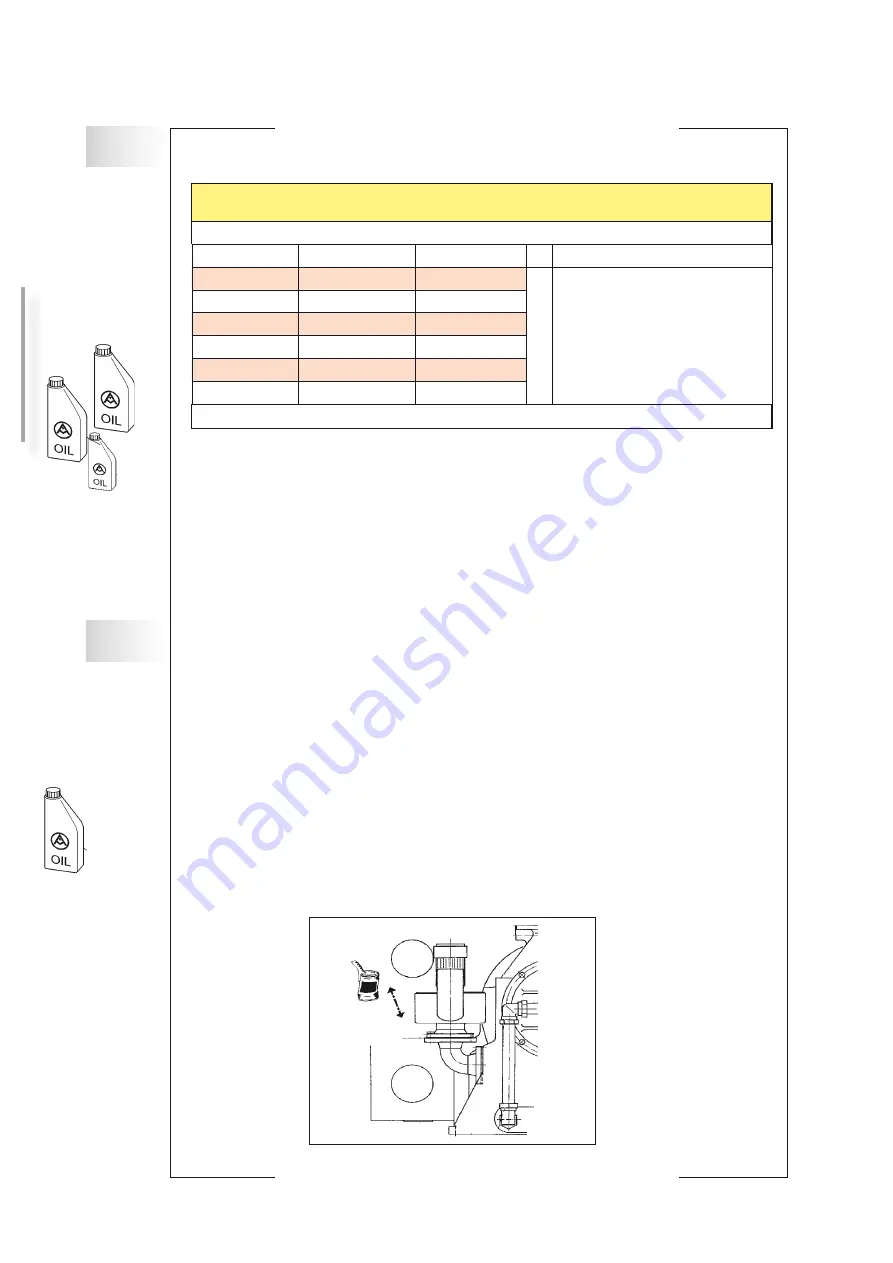
ENGLISH
V4-007 J EN
Originalbetriebsanleitung
28
8.4
Changing lubricants
Refilling oil
Oil drain must be closed / ensure tight fit.
•
Open oil filling ==> dismont the plug.
•
VML 150 / 250 ==> For filling up with oil, dismont the oil demister.==>
Fill up oil/at first not up to center of sight glass/
•
Let oil run down the inside walls.
•
Adjust oil level to center of sight glass.
•
Close oil filling again.
•
VML 150 / 250 ==> mont the oil demister.
Especially after first filling the oil level has to be observed carefully and if
•
necessary to be corrected after short operation time.
8.5
Lubricating oil quantities
NOTE:
The quantities of lubricating oil stated here are guide values.
To determine the quantity of oil to be poured in, it is important to note
the display on the oil sight glass of the compressor, or the display on
the oil sight glass of the acoustic hood.
Total oil fill volume
(approx.) in litres/oil level in centre of upper sight glass on compressor stage
approx. litres
approx. USG
VML 35
VML 210
12 l
3,2
VML 60
VML 310
28 l
7,4
VML 95
VML 410
30 l
7,9
VML 150
VML 510
50 l
13,2
VML 250
VML 610
90 l
23,8
Property of American Airlines