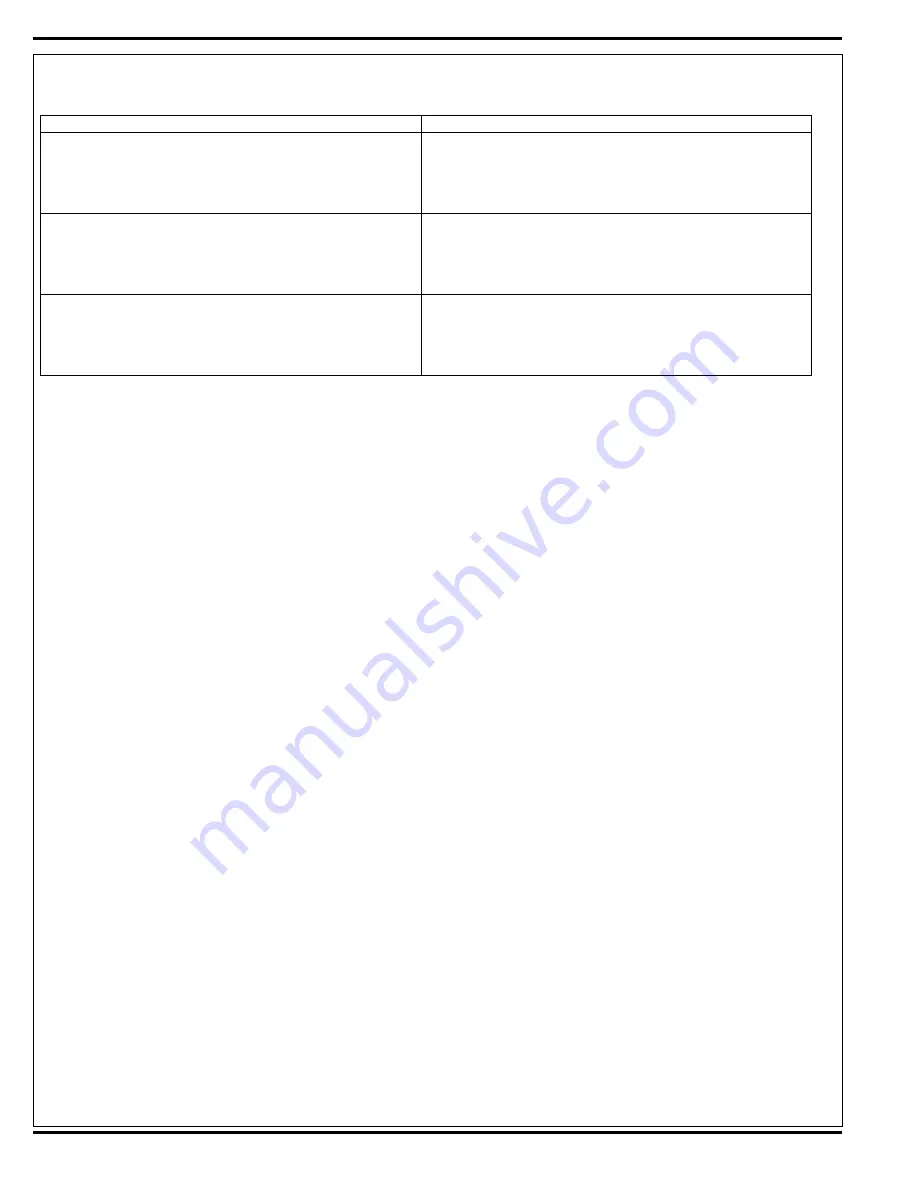
38
- FORM NO. 56043111 - Adhancer
™
WHEEL DRIVE SYSTEM
WHEEL DRIVE TROUBLESHOOTING GUIDE
Problem
Possible Cause
•
Wheel drive motor will not run in forward and reverse.
• Wheel Drive Motor Circuit Breaker (F3) tripped (reset 30A circuit breaker)
• Circuit Breaker for the Control Circuit (F2) tripped (reset circuit breaker)
• Defective Wheel Drive Motor (replace motor) *
• Defective Throttle Potentiometer (R1) (replace) *
• Replace the
(A2)
Speed Control
•
Wheel drive in one direction only, loss of either forward or reverse.
•
Test the Fwd and Rev
(R1)
wiring outputs (pins 3, 4 and 13) at the speed
control for an open. Repair wiring or replace the R1 pot.
•
Controller can’t change electrical polarity to wheel motor. Replace the
(A2)
speed control.
• Display LCD panel
shows an error 03 fault code.
•
Speed controller has sensed an operation error code fault. (see the
Status LED Fault Codes (Table 1)
in the Electrical System)
* See the
Electrical System/Curtis Controller Diagnostics
section.
Содержание Adhancer 56316001(W32-C)
Страница 1: ...7 08 FORM NO 56043111 SERVICE MANUAL Models 56316000 W28 C 56316001 W32 C Adhancer...
Страница 2: ......
Страница 7: ...FORM NO 56043111 Adhancer 5 TECHNICAL SPECIFICATIONS...
Страница 25: ...FORM NO 56043111 Adhancer 23 SCRUB SYSTEM FIGURE 2...
Страница 51: ...FORM NO 56043111 Adhancer 49 FIGURE 4...
Страница 53: ...FORM NO 56043111 Adhancer 51 FIGURE 5 ELECTRICAL SYSTEM...
Страница 59: ...FORM NO 56043111 Adhancer 57 FIGURE 6 ELECTRICAL SYSTEM...
Страница 68: ......
Страница 74: ......