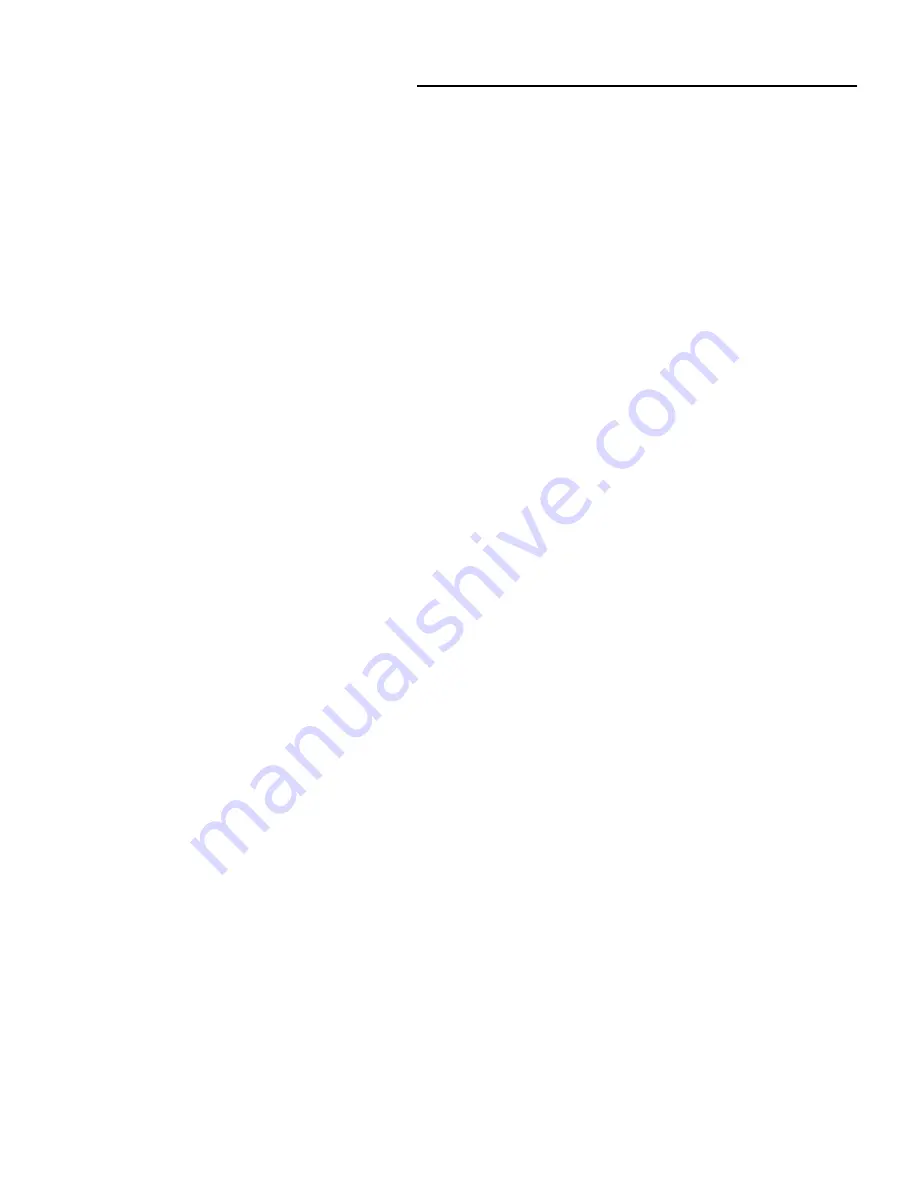
18
PREPARING EQUIPMENT FOR OPERTION
PRE-START CHECKLIST
Is the condenser and air handler unit properly located and
level with proper clearance? See page 4.
Is the ductwork correctly installed?
Is the condensate line properly sized, run, trapped, pitched
and primed?
Is the air filter of the correct size and number, clean and in
place?
Is the wiring properly sized and connected according to the
unit wiring diagram?
Are all wiring connections tight including those in the unit
and compressor electrical boxes?
Has the unit been properly grounded and fused with the
recommended fuse size? See wiring data.
Has the unit been leak tested? See page 14.
Do the condenser fans and indoor blower turn free without
rubbing and are they tight on the shafts?
Have all of the set screws been tightened on the blower
motor and fan?
Has the belt tension in the blower been checked and pulley
aligned?
Has all work been done in accordance with applicable local
and national codes?
Are all covers and access panels in place to prevent air
loss and safety hazards?
Has the voltage been checked? See pages 10 and 11.
Has the crankcase heater been energized for 8 hours? Be
sure the system switch is “OFF”.
START-UP AND REQUIRED FIELD ADJUSTMENTS
Do not attempt to start-up system below 50°F. ambient
temperature.
Be sure the crankcase heater has been energized for a
minimum of 8 hours.
Break the vacuum with liquid R-410A. Add to the liquid line
at the condenser until pressures are equalized.
Turn system switch on and operate unit. Now add
refrigerant vapor in the suction side until the liquid sight
glass is clear of bubbles. It is recommended the system be
charged initially by clearing the sight-glass. Do not
overcharge, verify subcooling.
On systems with optional hot gas reheat it may be
necessary to adjust the reheat thermostat to 50 degrees F.
This setting will de-energize the reheat circuit. If not
disconnect the reheat thermostat.
On units with tandem compressors, capacity control is
accomplished with a adjustable pressure switch. The
unloading pressure switch MUST be field adjusted. It
should be set to cut in at 140 PSIG and cut out at 108
PSIG. This will maintain a refrigerant temperature in the
evaporator of approximately 40 degrees F.
The hot gas bypass valve should be energized and this
should be the maximum charge required for these units.
Units with reheat will require additional charge for the
reheat circuit.
Adjusting the hot gas bypass valve. This bypass valve
Must be field adjusted. The valve must open at 115 PSIG.
It may be necessary to simulate a light load if the outdoor
temperature is above 70-75 degrees F. Reduce the
evaporator load (lower entering airflow) until the suction
pressure lowers to the point at which bypass is desired
(115 PSIG). If the hot gas bypass was de-energized to
stop hot gas flow, make sure it is now energized. Turn the
power assembly adjusting stem on top of the regulator in a
clockwise direction until bypass occurs (you will hear the
gas flowing or feel the hot gas line, it will be warm when
the unit starts to bypass).
Check or ensure suction pressure does not fall below the
predetermined set point (95 PSIG). A clockwise turn of the
adjusting stem will increase the pressure setting; a
counterclockwise turn will decrease it. Adjustments should
be made in small increments, allowing the system to
stabilize after each turn. Vary the evaporator load to test at
various conditions to ensure the suction pressure does not
drop below the predetermined setpoint. Replace the seal
cap on the adjusting stem.
Check the airflow by checking the external static pressure.
Verify the airflow is within the ratings. Check blower motor
amperage. Make adjustments as needed to ensure airflow
is correct and to specifications. On RCA units without hot
gas reheat, the low ambient head pressure control should
be factory set to cut-in at 400 PSIG and cut-out at 290
PSIG. Check calibration of this control. If trim adjustment is
required maintain a wide differential.
On systems with optional hot gas reheat, Verify the
operation of the reheat system by turning the reheat
thermostat to a temperature 5-10 degrees F. above the
leaving air temperature. The reheat solenoid will be
energized and will cycle as the temperature changes. Set
the reheat thermostat at the desired leaving air
temperature. Adjustment should also include a calibration
check of the head pressure control for the other fan
motor(s) .The recommended settings are to cut in at 450
PSIG and cut-out at 375 PSIG. Disregard these steps if
the unit is not equipped with hot gas reheat. These units
utilize an electronic variable speed head pressure control
for one condenser fan motor. It is factory set to maintain a
minimum head pressure of 330 PSIG. For more
information on the reheat control valve, See Supplemental
Instructions for Hot Gas Reheat. Readjust the reheat
thermostat to 65-70 degrees F. The hot gas reheat circuit
should be energized. Again clear the sight glass. This
would be the maximum charge required for this system.
The final adjustment of the refrigerant charge should be by
subcooling. The recommended subcooling at the
condensing unit should be around 15 degrees at 75
degrees F. and as low as 5 degrees at 105 degrees F.
Verify proper operation of the thermostatic expansion valve
by checking the superheat. The superheat should be 18-20
degrees at the suction line in the condensing unit.
Содержание RCA051
Страница 8: ...8 DIMENSIONS...
Страница 9: ...9 DIMENSIONS Continued...
Страница 10: ...10 DIMENSIONS...
Страница 11: ...11 DIMENSIONS Continued...
Страница 14: ...14 TYPICAL FIELD WIRING DIAGRAM...
Страница 17: ...17 FIELD WIRING DIAGRAM...
Страница 24: ......
Страница 26: ...26 NOTES...
Страница 27: ...27 NOTES...
Страница 28: ...28...