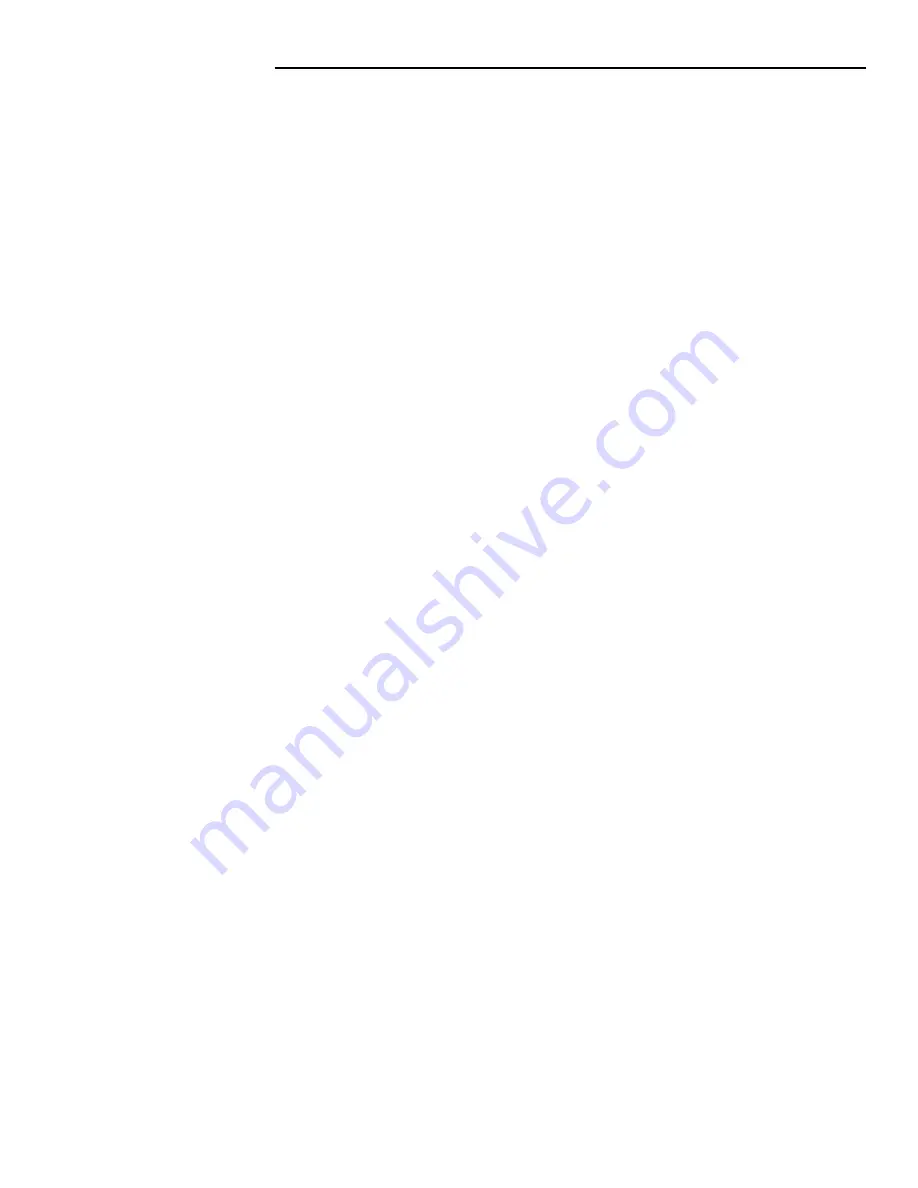
3
PRODUCT DESCRIPTION
THE CONDENSING UNIT CONSISTS OF THE
FOLLOWING COMPONENTS:
Compressor
: A single scroll compressor used in model
sizes RCA051 – RCA201. A tandem scroll is used in
models RCA271-RCA421. All compressors have
crankcase heaters and the motors are equipped with
internal-overload protection
Condenser:
The condenser coils are aluminum plate
finned formed on multiple rows of seamless copper tubing
arranged in a staggered tube configuration.
Condenser Air Fan(s)
: Each condenser air fan is a
propeller type, electronically balanced and direct-driven.
Condenser air is drawn through the coil(s) horizontally and
discharged vertically. Therefore, heated air can not be re-
circulated. A vinyl coated fan guard is provided.
Condenser Fan Motor(s):
On standard RCA units the fan
motors are single phase and are controlled by a low
ambient head pressure control, which cycles the fan, or
fans to maintain high side pressure. Units with optional hot
gas reheat are different. One condenser fan is direct-
driven by a 1075 rpm single phase PSC fan motor, and it is
controlled by a variable speed head pressure control. This
electronic device is factory set for proper operation. The
inherently protected motor has sealed ball bearings that do
not require lubrication. On dual and multiple fan units, the
other condenser fan motor(s) are three phase and are
controlled by a separate low ambient control.
REFRIGERANT CIRCUIT COMPONENTS
Accumulator:
A storage tank located in the suction line of
the system. It separates the liquid refrigerant to protect the
compressor from liquid slugging by allowing small amount
of liquid refrigerant to boil away before entering the
compressor.
Filter-Drier (liquid)
: A filter used in the refrigerant line to
remove moisture and small particles.
High Pressure Safety Control
: A manual-reset high
pressure control switch will stop the compressor if the
system pressure exceeds 400 PSIG. This protects the
compressor in case of blockage in the high side of the
system.
Low Pressure Control/Loss of Charge Protector:
An
automatic-reset low pressure control switch will stop the
compressor if the low side of the system pressure drops
below 60 PSIG. This is to protect the compressor in case
of blockage in the low side of the system or loss of charge.
This control is also used as an operating control-recycling
pump-down.
Dual Service Connections:
Used for high and low
pressure readings.
24 Volt Pump Down Solenoid Valve:
Shipped loose with
the condensing unit and is to be field installed in the liquid
line as close to the evaporator, at the air handling unit, as
possible. The liquid line solenoid is factory installed on
units with hot gas reheat.
Hot Gas Bypass Circuit:
Provided for capacity control by
maintaining a constant suction pressure at the
compressor. It consists of an adjustable pressure regulator
which introduces compressor discharge gas into the
evaporator, providing a false load.
ELECTRIC CONTROLS
Internally wired controls include;
Compressor Anti-Short Cycle Timer: Prevents the
compressor from rapid starting and stopping due to power
interruptions.
Fan and Compressor Motor Contactors or Starters:
These controls are rated for the connected load.
24 Volt Transformer:
Mounted in the sheet metal control
panel. The 24 Volt control circuit includes a low voltage
terminal board.
Condenser Fan Cycling Head Pressure Control:
The
standard RCA unit utilizes this control to assure adequate
head pressure control during low ambient conditions. This
head pressure control system cycles the condenser fans
off at 290 PSIG and on at 400 PSIG. This setting will be
adequate for most systems. If trim adjustment is made,
maintain wide differential to prevent rapid cycling of the fan
motor.
On systems with optional hot gas reheat this low ambient
control is only used for the additional fan motor(s). The
recommended settings are as follows; cut-off at 375 PSIG,
and cut in at 455 PSIG.
Variable Speed Condenser Head Pressure Control:
(furnished with hot gas reheat) Condenser head pressure
is controlled by a variable speed control located in the
compressor section. Through sensing of compressor
discharge pressure, the voltage to the fan motor is
adjusted to speed up or slow down the condenser fan
speed. This action produces relatively constant discharge
pressure at varying load and ambient conditions. The
control is factory set to ensure consistent performance.
(See Supplemental Instructions for Hot Gas Reheat for
more information).
Adjustable Ambient Thermostat (Compressor Lockout
Thermostat):
A remote field supplied and installed system
switch, such as time clock or exhaust fan interlock, is
required to start-stop the air handler blower motor and
energize the controls. The compressor adjustable ambient
lock-out thermostat controls the cooling operation at a
setting between 65 and 70 degrees F. Operation of the
compressor is thus limited to outside air temperatures
above the setpoint.
Typically, blower operation is continuous. The leaving air
temperature will be maintained by compressor capacity
control, accomplished through suction-pressure sensing,
thus tracking the outside air temperature variations. The
use of discharge air or space sensing devices (duct or
room thermostats) to control the compressor will produce
unpredictable results and is not recommended.
Содержание RCA051
Страница 8: ...8 DIMENSIONS...
Страница 9: ...9 DIMENSIONS Continued...
Страница 10: ...10 DIMENSIONS...
Страница 11: ...11 DIMENSIONS Continued...
Страница 14: ...14 TYPICAL FIELD WIRING DIAGRAM...
Страница 17: ...17 FIELD WIRING DIAGRAM...
Страница 24: ......
Страница 26: ...26 NOTES...
Страница 27: ...27 NOTES...
Страница 28: ...28...