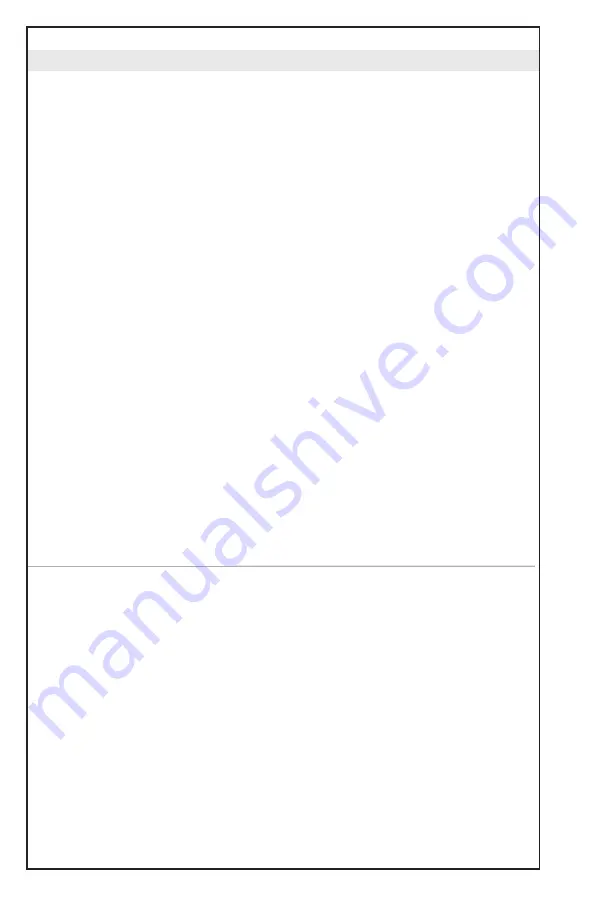
18
TROUBLESHOOTING: GENERAL GUIDE
Possible Solutions
Check that the feed roll size is correct for the wire size being used.
Increase the drive roll pressure until the wire feed is even. Do not apply
excessive pressure as this can damage the wire surface, causing cop-
per coating to loosen from steel wires or metal shavings to be formed
from soft wires like aluminum. These metal fragments or shavings can
be drawn into the wire feed conduit and will rapidly clog the gun liner.
When welding with flux-cored wires, excessive drive roll pressure may
open the wire seam and allow flux or metal powders to escape.
a. Dust, particles of copper, drawing lubricants, metal or flux and
other forms of contamination can all clog the gun liner so that the
wire feed is slowed or impeded. A liner that has been in use for an
extended period of time becomes worn and filled with dirt and
must be replaced.
b. When changing the welding wire, remove the swanneck from the
front end of the gun and blow out the gun liner with clean, dry
compressed air from the back of the gun. Repeat with the neck
liner.
Note: Wear safety goggles when using compressed air to
clean the liners. Make sure proper safety procedures are followed
in order to avoid possible serious eye injury.
Check the lengths of the neck and gun liners and trim or replace if too
long or too short. The efficient feeding of the welding wire is depen-
dent on the liners fitting correctly. Consult the liner installation instruc-
tions on pages 2-4 or contact your local authorized ABICOR Binzel
distributor for additional help.
An unprotected coil of wire quickly collects dust and other airborne
contamination. If grinding is being performed in the vicinity, particles
can become attached to the wire, severely interfering with the wire
feed. Replace with clean wire and keep it protected with a cover. Make
sure spare wire rolls are stored in a clean, dry place.
Set the brake so that the coil immediately stops rotating as soon as
welding is interrupted. If the brake is applied too hard it will cause the
feed rolls to slip, resulting in uneven wire feed. If it is too loose, over-
run of the wire will occur, causing wire tangles, inconsistent tension on
the feed mechanism and irregular arc characteristics.
Set the wire feed in relation to the arc voltage in such a way that the
arc is stable and burns evenly. In spray arc welding, set the wire feed
so that there are no short circuits and the filler metal is transferred in a
spray across the arc.
Find the cause of the interference and correct it. (See above)
When the internal diameter of the contact tip becomes worn from the
passage of wire through it, the wire may no longer stay in continuous
electrical contact with the tip. This results in an unstable arc and an
increase in spatter.
Paint, mill scale, silicon scale, rust or flux deposits from previous weld
runs may form an insulating layer causing an unstable arc. Clean the
surfaces to be welded.
Securely attach the ground cable as close to the point of welding as
possible on the workpiece. Clean the surfaces thoroughly to ensure
good contact.
Check to insure the welding power connection on the power source is
tight, the connection on the wire feeder is tight, the connection to the
adaptor block is tight, and the connection of the gun to the adaptor
block is tight.
Adjust the contact tip to work distance to a minimum of 3/8” for short
arc welding. A more precise distance is 15 times the wire diameter.
Problems/Causes
ERRATIC WIRE FEED
Slipping feed rolls.
Clogged or worn gun
liner.
Liners too long or too
short.
Spatter on wire.
Coil brake incorrectly
adjusted.
UNSTABLE ARC
Incorrect setting of volt-
age and/or current.
Problems in wire feeding.
Worn contact tip.
Impurities on the base
metal.
Poor contact between
ground cable and work-
piece.
Loose power connection.
Stick-out too long.
Содержание ALPHA 1
Страница 1: ...www binzel abicor com ABICOR ALPHA SERIES Instruction Manual ...
Страница 2: ......
Страница 23: ......