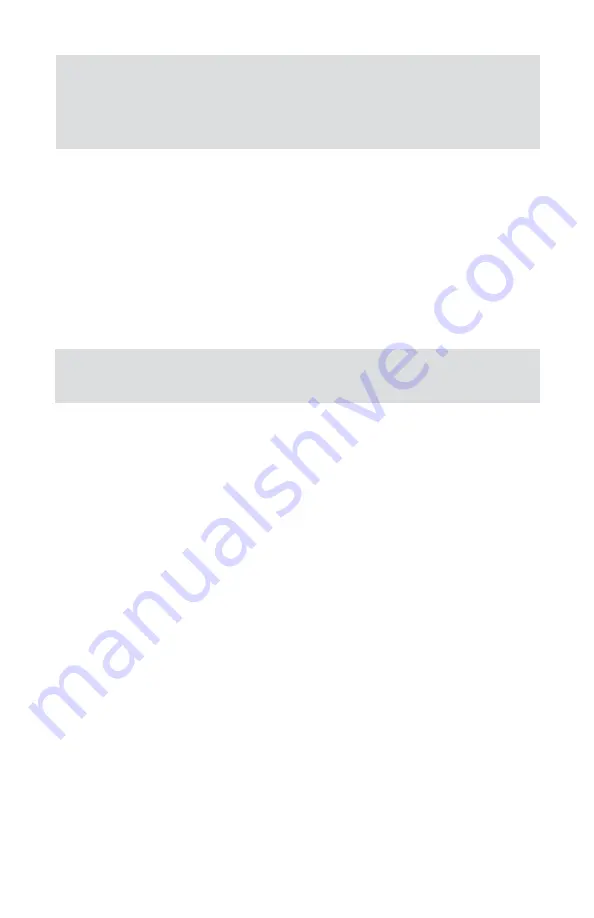
42
5.3.16 Submenu “Program Set Point”
The Program Set Point Control allows execution of custom, user-preset pro-
grams of up to sixteen steps. During execution of the program, the user can
activate or deactivate the LOOP mode and pause program execution. Various
flow configurations may be preprogrammed: ramping, pulsing, linearized
increasing and/or decreasing of the flow. Before executing, the program should
be entered in the program table in the format: SETPOINT [% F.S.] - TIME [sec.].
TIME means: time it takes for the value of the set point signal for the flow con-
troller, to linearly approach the SETPOINT value (ramping).
Following settings are available for “Program Set Point” (see Figure 5.7):
a) Program Set Point Mode (Tabular Entry)
This function determines whether the Program Set Point is Enabled or
Disabled. The following selections are available: Enabled or Disabled. The
default entry is Disabled. Program Set Point Mode selections can be set with
the
UP
and
DN
buttons and are accepted by pressing
ENT
button.
b) Program Set Point Loop Mode (Tabular Entry)
This function determines whether the Program Set Point Loop is Enabled
or Disabled. If Loop is enabled as the program reaches the last step it
wraps around and again starts execution from the first enabled step. The
following selections are available: Enabled or Disabled. The default entry
is Disabled. Program Set Point Loop Mode selections can be set with the
UP
and
DN
buttons and are accepted by pressing
ENT
button.
c) PSP Steps Mask (Tabular Entry)
Using PSP Steps Mask settings the user can enable (unmask) or disable
(mask) any step in the program. If the step is masked, the program will
skip it and move to the next enabled step. By default the unit is shipped
from the factory with all program steps enabled (unmasked). A typical
display with PSP Steps Mask selection is shown below.
Note: Program Set Point feature will work only if “Device Function”
parameter is set to Controller.
,
Note: It is recommended to use Aalborg
7
supplied calibration and
maintenance software for linearization table calibration. This software
includes an automated calibration procedure which may radically
simplify reading and writing for the EEPROM linearization table.
,
Содержание TIO
Страница 14: ...10 Figure 4 3 RS 485 Multidrop Half Duplex Two Wire System...
Страница 55: ...51 Figure 6 2 Connecting TIO to the GFM using 0 5 Vdc output from DB9 connector...
Страница 56: ...52 Figure 6 3 Connecting TIO to the GFM using 5 10 Vdc output from RJ11 connector...
Страница 57: ...53 Figure 6 4 Connecting TIO to the GFM using 4 20 mA output from DB9 connector...
Страница 61: ...58 Figure 6 6 Connecting TIO to the GFC Using 0 5Vdc Input Output from DB15 Connector...
Страница 62: ...59 Figure 6 7 Connecting TIO to the GFC Using 4 20mA Input Output from DB15 Connector...
Страница 68: ...65 Figure 6 9 Connecting TIO to the Generic Flow Meter...
Страница 69: ...66 Figure 6 10 Connecting TIO to the Generic Flow Controller...
Страница 95: ...92 APPENDIX D Mechanical Drawings...
Страница 96: ...93 APPENDIX E Circuit Layout Diagrams Circuit Layout Top...
Страница 97: ...94 Circuit Layout Bottom Mirror...