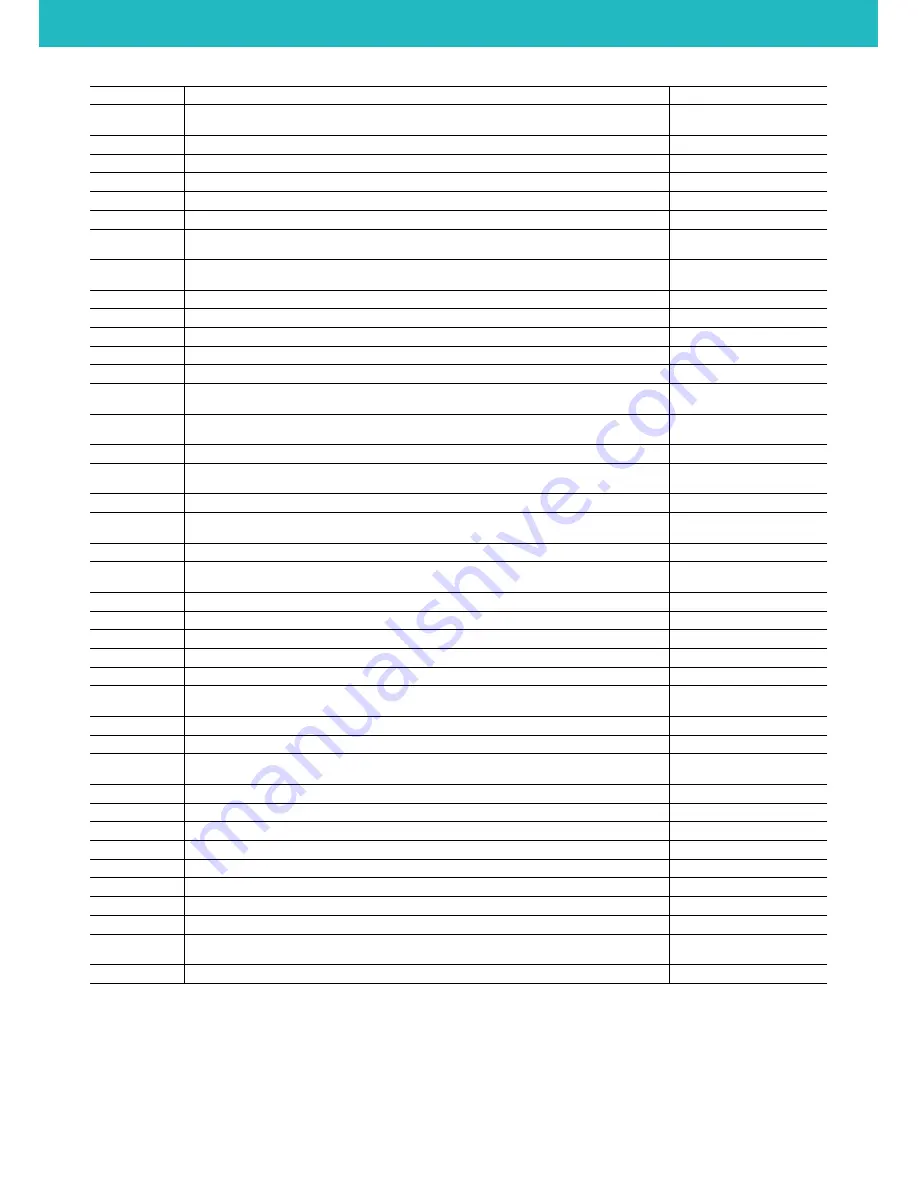
M119
Show limit switch status
M119
M120
"Push" the current feed-rate and seek-rate so that another one can be temporarily used, then the current one can
be restored
M120
M121
"Pop" the current feed-rate and seek-rate, see M120
M121
M140
Set Bed Temperature - S<temperature>
M140 S55
M190
Set Bed Temperature and Wait - S<temperature>
M190 S55
M200
Set E units for volumetric extrusion - D<filament diameter> set to 0 to disable volumetric extrusion
M200 D3.0
M203
Set maximum feedrate your machine can sustain <mm/sec>
M203 X100 Y100 Z100 E10
M204
S<acceleration> Set acceleration in mm/sec^2 Z<acceleration> NB Z only applies to Z only moves E<nnn> Set
extruder only move acceleration
M204 S1000 Z100 E500
M205
X<junction deviation> Z<z junction deviation> S<minimum planner speed>, Z junction deviation only applies to z
only moves, 0 disables junction deviation for Z, -1 uses global junction deviation
M205 X0.05 S30.0
M206
Set homing offsets
M206 X10 Y3 Z0.5
M207
set retract length S[positive mm] F[feedrate mm/min] Z[additional zlift/hop] Q[zlift feedrate mm/min]
M207 S4 F30 Z1
M208
set retract recover length S[positive mm surplus to the M207 S*] F[feedrate mm/min]
M208 S0 F8
M220
S<factor in percent>- set speed factor override percentage
M220 S50
M221
S<flow rate factor in percent>- set flow rate factor override percentage for current extruder
M221 S50
M301
Edit temperature control PID parameters X<i_max> Y<max_pwm>
M301 S0 P30 I10 D10 X255.0000
Y255
M303
Begin PID auto-tune cycle E<hotendid> S<temperature>
M303 E0 S185 - Tune extruder -
M303 E1 S100 - Tune printbed -
M304
Abort PID auto-tuning
M304
M305
Set parameters for the thermistor, where B is beta, R is r0 and X is t0; P is the ID from the thermistors list (use
console command thermistors to get a list).
M305 B4066
M306
Set homing offsets based on current position, subtracts current position from homing offset for specified axis
M306 Z0
M370
Z grid strategy: clears the ZGrid and the bed levelling is disabled until G32 is run again. Specify X and Y values to
change grid size
M370 M370 X9 Y11
M371
Z grid strategy: moves the head to the next calibration position without saving for manual calibration
M371
M372
Z grid strategy: move the head to the next calibration position after saving the current probe point to memory -
manual calbration
M372
M373
Z grid strategy: completes calibration and enables the Z compensation grid
M373
M374
Z grid strategy: save calibration grid. optional S parameter saves a custom file with numerical extention
M374 S123
M375
Z grid strategy: load calibration grid. optional S Parameter loads a pre saved custom grid
M375 S123
M400
Wait for the queue to be empty before answering "OK"
M400
M500
Save some volatile settings to an override file
M500
M501
Load config-override file optionally specifying the extension
M501 - loads config-override, M501
test1 - loads config-override.test1
M502
Delete the override file, reverting to config settings at next reset
M502
M503
Display overridden settings if any
M503
M504
Save the settings to an override file with specified extension
M504 test1 - saves to config-
override.test1
M557
Defines probe points
M557 P1 X30 Y40.5
M561
clears the plane and the bed leveling is disabled until G32 is run again
M561
M565
defines the probe offsets from the nozzle or tool head
M565 X3 Y4.5 Z-2.37
M600
Suspend print in progress (use console command resume to continue)
M665
Set arm solution specific settings: Delta - L<arm length> R<arm radius> Z<max height>
M665 L341.0 R350 Z430
M666
On a delta sets trim values for the endstops. (Positive values will crash physical endstops.)
M666 X-0.1 Y-0.2 Z-0.3
M1910.x
Move a given number of steps, without acceleration ( for testing only ) M1910.1 will stop the motor
M1910 X100 F100
M957
(with Spindle module enabled) Report the current spindle speed and PWM value
M957
M958
(with Spindle module enabled) Report the current spindle PID parameters. M958 Px.xx Ix.xx Dx.xx will set them (to
save the new values, you need to edit config file manually).
M958 P0.1
M999
Reset from a halted state caused by limit switch, M112 or kill switch
ATLAS SERIES
Supported Commands
28