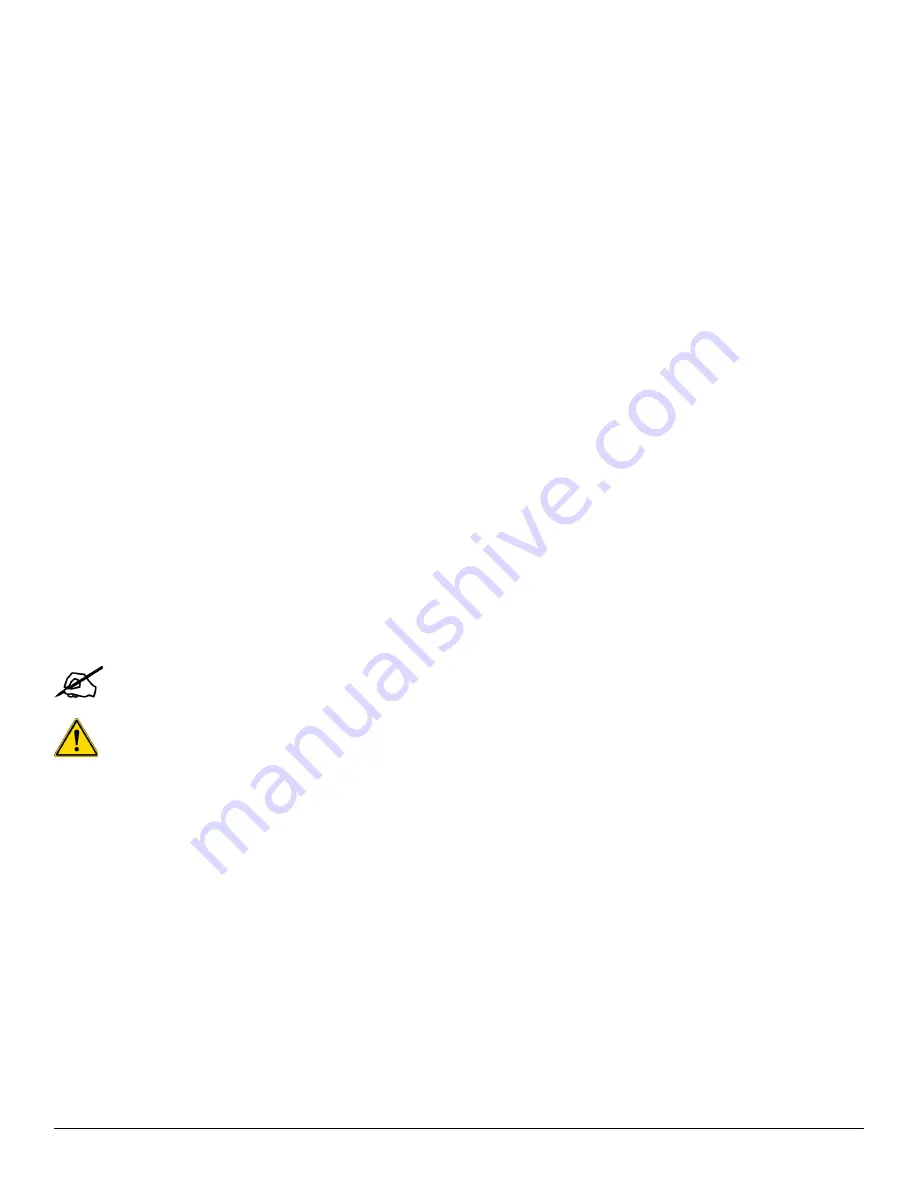
3D Systems, Inc.
26
p/n: 15-D99, rev. C
5.2 Waste Disposal Area
Ability to dispose of waste:
•
Contaminated process filters
• Waste oil from the vacuum pump and blower
• Metal powder
• Clothes and paper towels that are used to clean
• Other items that contain metal powder
Closed metal containers need to be available for waste disposal. These waste containers need to be stored, if possible, in a
closed environment outside the production facility.
Waste materials must be disposed of in accordance with all local, state and federal regulations. Check all applicable laws and
local regulations regarding waste disposal. Refer to
DMP Safety guide (p/n: 80-D0712)
.
5.3 Special Considerations - Reactive Metals
The modifications listed in this section must be followed if you are using reactive metals in your facility. The following are
considered to be reactive metals:
• Titanium and Titanium alloys
• Aluminum and Aluminum alloys
5.3.1 Electrical Equipment
Avoid using standard electrical equipment inside the reactive metal dust zone. Only use equipment that meets the explosion
safety requirements.
5.3.2 Fire Suppression
The facility must have a Class D fire extinguisher or dry sand, or salt and a fire blanket present in the work area.
The automatic sprinkler system must be disabled in areas where reactive metals are used or stored. Several of the materials,
(magnesium, titanium, aluminum, etc.) will react with water to produce hydrogen. With the sprinkler system disabled, local
building code may require the installation of an inert gas system for fire suppression (argon is recommended, halon is
prohibited).
Note: Although a class D is required for metal fires, also consider having a class ABC portable on hand as well
for non-metal fires that a class D is not effective against.
Caution: Personnel must be trained on fire prevention and suppression.
5.3.3 Good Housekeeping
Make sure that dust layers, clouds or dangerous concentrations of dust are avoided by good housekeeping.
Examples of good housekeeping include, but are not limited to:
• Using a wet separator, explosion-proof vacuum cleaner after each use. The RPM and TRM must be throughly cleaned
before moving to the next module, to avoid potential dust clouds.
•
Using a floor cleaning machine at the end of each shift, to avoid dust layers around the modules and on the
production floor.
• Using a dust extraction system to remove airborne dust out of the air any time metal powder is handled.
• Using pure enthanol to wipe down the modules after each use and before transporting the RPM.
Содержание DMP Flex 350
Страница 1: ...DMP Flex 350 Production printer Facility guide Original instructions...
Страница 22: ...3D Systems Inc 18 p n 15 D99 rev C 3665 mm 144 3 4 2 Dimensions of Assembled System Top View...
Страница 28: ...3D Systems Inc 24 p n 15 D99 rev C 120 mm 4 72 120 mm 4 72 829 mm 32 64 35 mm 1 38...