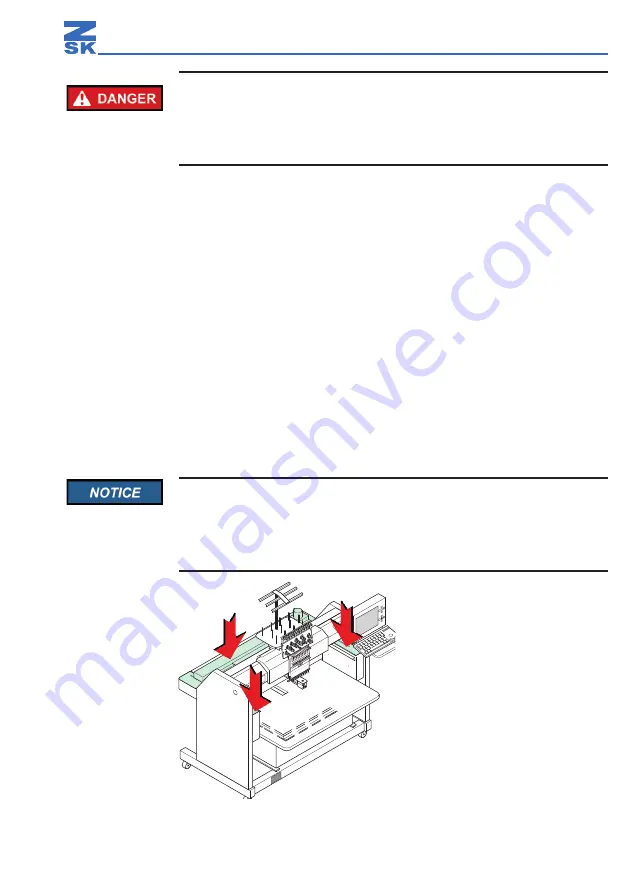
17
Grease linear guide
BACK
00012V40-GB-W
AR
TUNG FREIARM-FLACHBETTMASCHINEN_-_2022-09-27 - DC
Make certain that no grease is applied to the toothed belt; this can give
rise to malfunctions.
Do not restart the machine until all covers have been properly
reinstalled.
Machines with several transverse drives
The several transverse drives on some machines are connected by way of a crossarm, so
that the covers cannot be removed.
• Unscrew and remove the screws in the covers
q
(Fig. 12).
• Move the border frame
w
(Fig. 12) to the right end position. The plates can then be
moved to the right.
• After greasing the guide, slide the covers back to their original positions.
• Move the border frame
w
to the left end position. Slightly raise the covers
q
.
• Grease the guides underneath the panel with a brush.
Cylinder arm machines
For cylinder arm machines, lubrication of the linear guides is required
in both axis directions (X and Y axis).
For free-arm machines with 8 heads or 6 heads with 495 mm head
spacing, the center guide (X axis) must also be lubricated.
• Slacken off screws.
• Raise cover at front first, then at back;
Fig. 16: Pantograph drive, (illustrated on 1Head-Cylinder arm machine)
Pantograph - 1x Drive (side to side)
Pantograph - 2x Drive (front to back)
JF
011
15
00