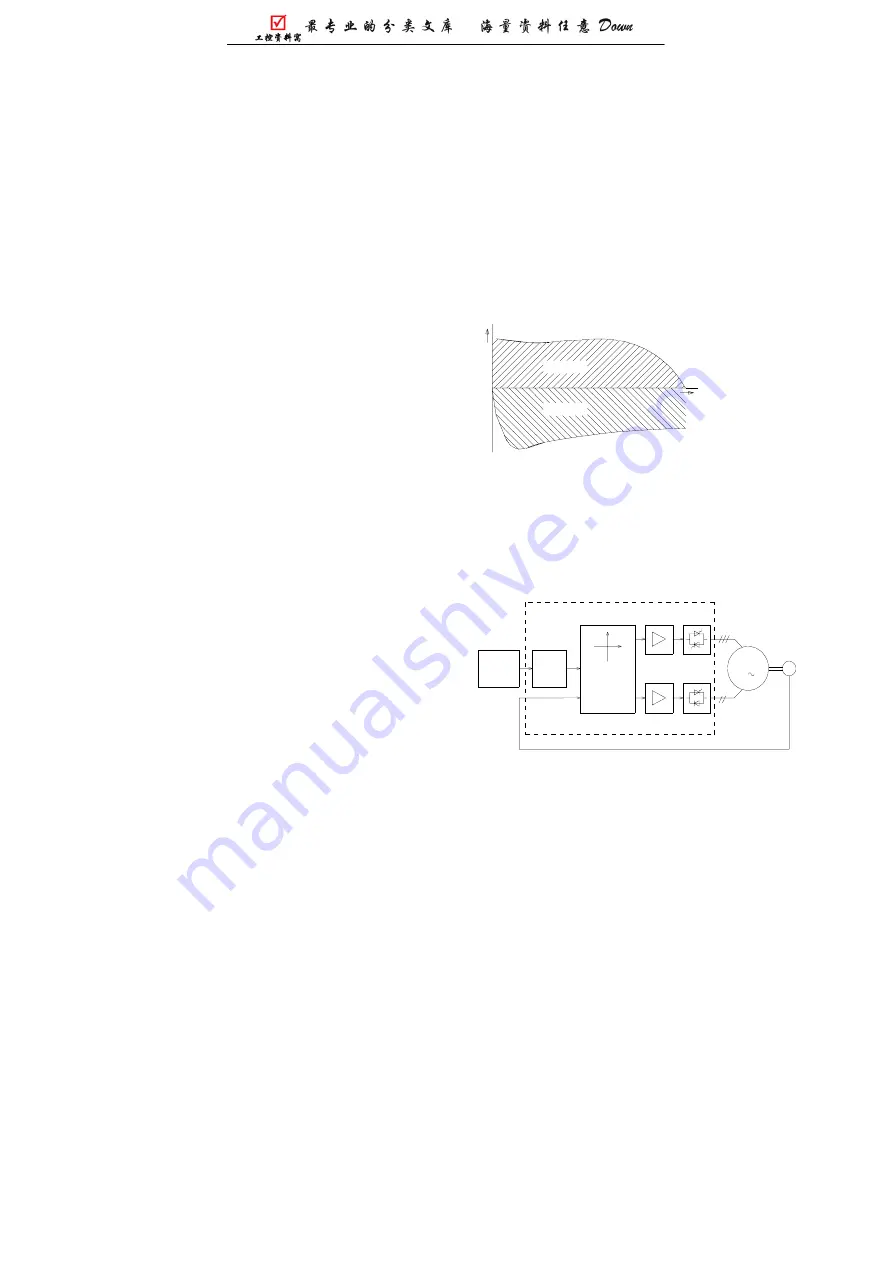
System information ZETADYN 1DV 7
The logic design allows the equipment to be easily adapted to various applications.
1. Controls
The superior control system communicates with
the controller through floating inputs and
outputs. Time and distance related control
programs are selected by activating optically
coupled inputs. The operating condition of the
drive is continually signalled back to the controls
through floating relay outputs.
2. Parameterizing
Commissioning, service and documentation are
supported by digital computer technique:
speeds, accelerations and other parameters
specific to the system can be entered through
text dialogue by using the integral display and
operating unit. A password protects the system
against misadjustments. It is also possible to
parameterize through a PC or the ZETAMON
software with user guide, which is available as
one of the accessories.
3. Regulation
All programs are run at regulated speeds and
independent of the load. The regulating control
system can be used for speeds up to 3.5 m/s.
The regulating range up to 1:100 allows a high
degree of positioning accuracy.
4. Drive
A high degree of stability of a drive at low load
torques can only be achieved by continuous
transition of drive and braking conditions.
ZIEHL-ABEGG asynchronous motors for
variable drives have two electrically separated
windings.
The AC winding produces the drive torque
and the DC winding the braking torque
.
Figure 1.2 Torque generation
Both windings in the motor are activated
separately, a three-phase thyristor speed
controller feeds the AC winding, a semi-
controlled DC bridge the DC winding (see Figure
1.3).
Figure 1.3 Schematic diagram control circuit
This ensures perfect running response in all load
situations.
No brake wear occurs in control operation up to
STOP. The drive operates very quietly.
n
drive
brake
M
Zetadyn 1DV
M
3
T
B
T B
Digital
4-Q-
speed
controller
PLC
brake
drive
Encoder
set point
generator