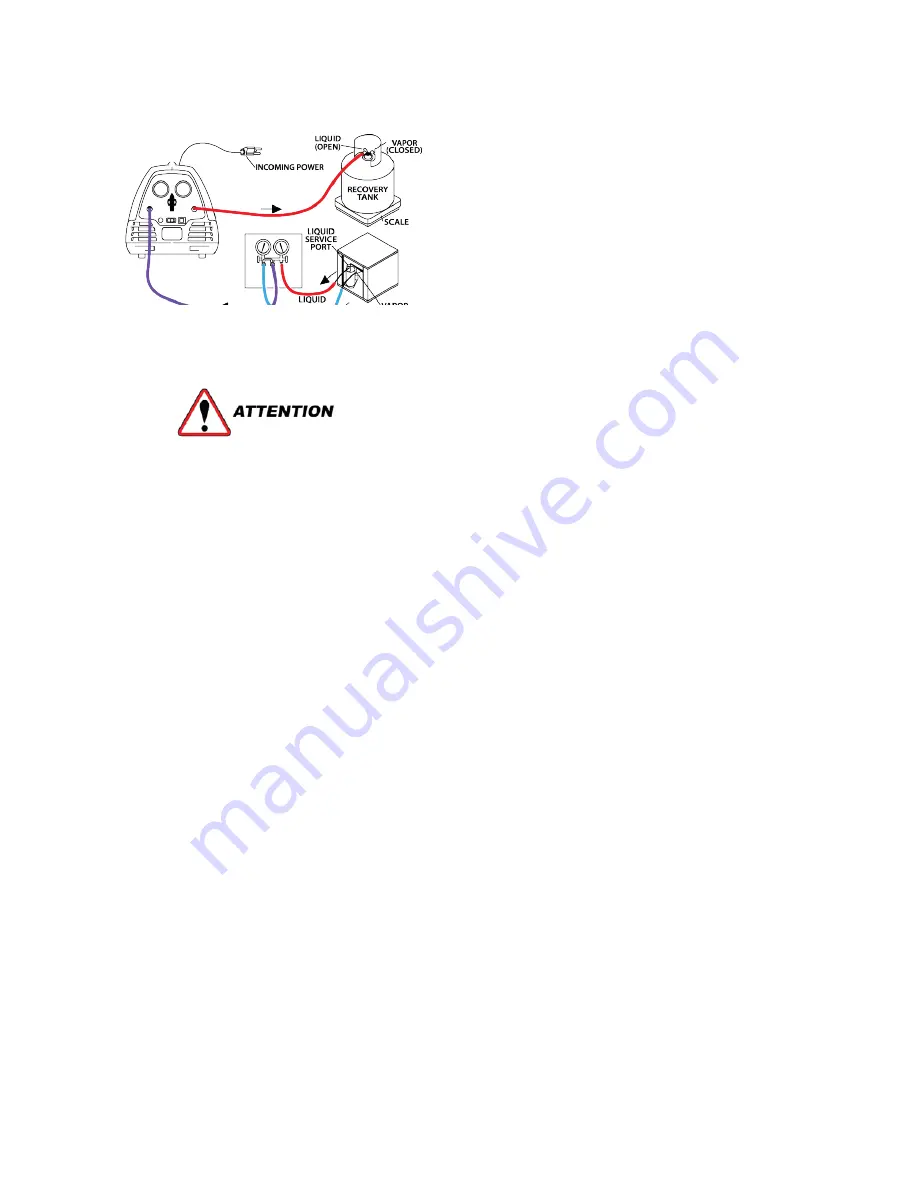
29
4.4 REFRIGERANT LEAK CHECKING
Use only Nitrogen to pressurize the system. Any other
gas or vapor will contaminate the system that will
require additional purging and evacuation.
A refrigerant leak check should always be performed
after the system has been opened to replace or repair
a component. To check for leaks in the refrigeration
system, perform the following procedures
Using a electronic leak detector is a effective way to
isolate areas of the unit for leaks if there are no visible
signs of leaks before using nitrogen.
1.
Charge system with nitrogen to build up
pressure in steps of 50psigg, 150psigg,
300psigg till leak is found.
2.
Remove nitrogen and repair any leaks. Leak
check once more. Evacuate and dehydrate
the unit. (Refer to section 4.5)
4.5 EVACUATION AND DEHYDRAYION
Moisture can seriously damage refrigerant systems.
The presence of moisture in a refrigeration system
can have many undesirable effects. The most
common are copper plating, acid sludge formation,
“freezing- up” of the expansion valve by free water,
and formation of acids, resulting in metal corrosion
4.5.1 Preparation
1.
Evacuate and dehydrate only after pressure
leak test. (Refer to section 4.4)
2.
Essential tools to properly evacuate and
dehydrate any system include a good
vacuum pump (5 cfm= 8m#H volume
displacement) and a good vacuum indicator
such as a thermocouple vacuum gauge
(vacuum indicator).
3.
Keep the ambient temperature above 15°C
(60°F) to speed evaporation of moisture. If
ambient temperature is lower than 15°F
(60°F), ice might form before moisture
removal is complete. Heat lamps or alternate
sources of heat may be used to raise system
temperature.
4.
4.5.2 Procedure for evacuation and dehydrating the
system
1.
Install gauge hoses to unit
2.
Install service hose to vacuum pump
3.
Turn on vacuum pump
4.
Open manifold gauge valves
5.
Run vacuum pump on system for at least 1
hour
6.
Ensure vacuum has reached -30in and 500
microns
Figure 12- Vacuum Pump Connections