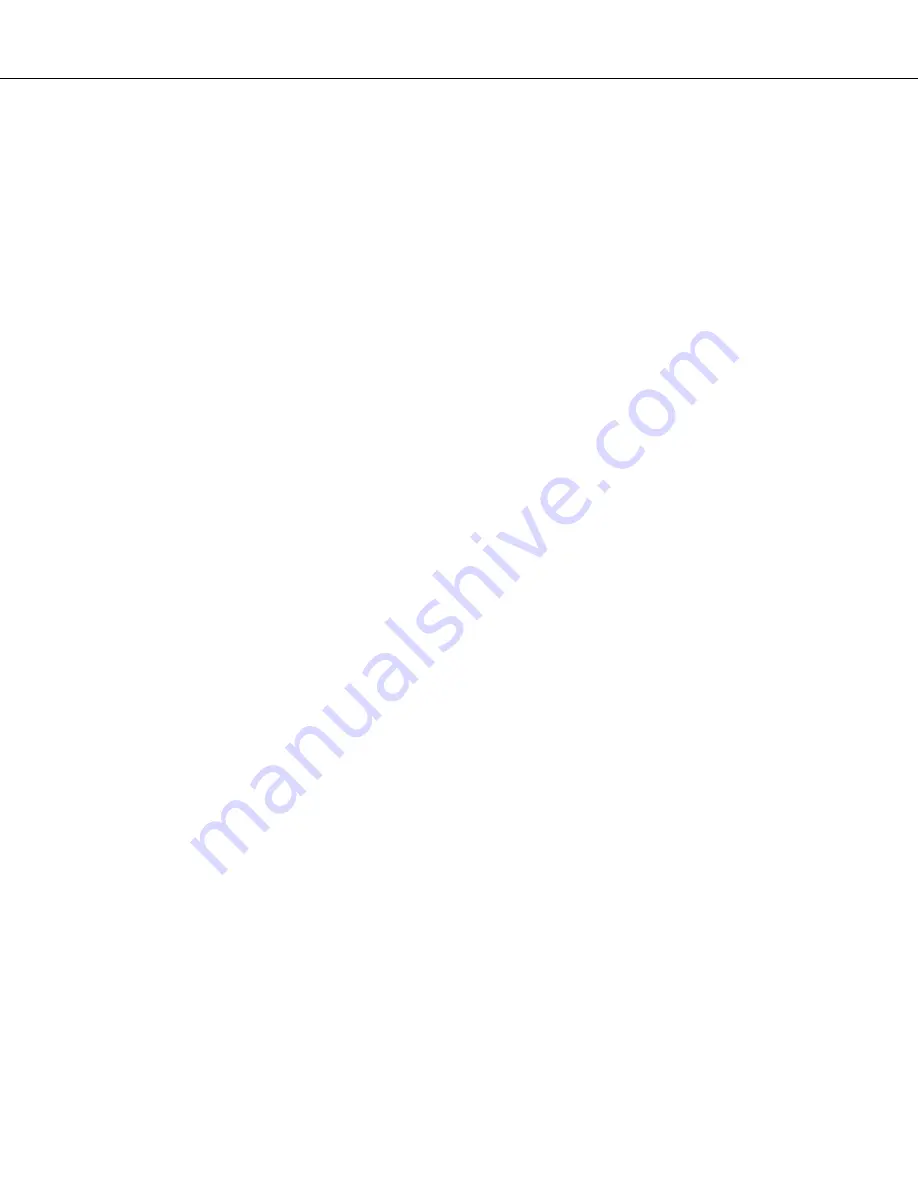
41
(
1) TESTING METHODS
(a) Electronic Leak Detector:
This is the easiest method for leak detection. Electronic leak detectors can be used in areas where an open flame is not
permitted. Pass the detecting probe over the area of the suspected leak. If a leak is present, the detector sounds a high
frequency alarm or signals by a flashing light, depending on the model used.
(b) Soap Bubble Testing:
Applying a generous amount of common dish washing detergent to the suspected areas creates tell-tale bubbles if a
large leak is present.
CAUTION:
DO NOT USE THE COMPRESSOR TO BUILD UP PRESSURE IN THE SYSTEM. DO NOT OVERCHARGE THE
SYSTEM.
(2) TESTING PROCEDURES
(a) Charge the system to 10 psig with refrigerant. Add dry nitrogen (do not use oxygen) until the system pressure is 150
psig. Check for leaks with a halide electronic leak detector (Preferred method).
OR
(b) Charge the system with dry nitrogen (do not use oxygen) to 150 psig and use the soap- bubbles test to find large leaks
(Alternate method).
9.7 REFRIGERANT LEAK REPAIR
WARNING:
ENSURE ADEQUATE VENTILATION DURING REPAIRS. PHOSGENE GAS, A DEADLY POISON, IS GENERATED
WHEN REFRIGERANT IS EXPOSED TO FLAME.
(1) Locate leak as described above.
(2) Using a refrigeration recovery system compatible with R22, pump refrigerant from the system and dispose.
(3) Replace drier if necessary, see sight glass for moisture indication.
(4) Correct leak as described below.
(5) If no leaks are present, pump out system and then evacuate system to at least 500 microns, hold for 30 minutes.
Break vacuum with R22 and raise system pressure to 0 to 5 psig. Re-evacuate system to 500 microns.
Repeat this for a total of three (3) times, then charge the system with R22 as per unit name plate or refer the below
paragraph.
(6) Leak Repair Procedure:
(a) Thoroughly clean paint, dirt and oil film from adjacent piping. Use a wire brush, sand cloth or sandpaper.
(b) Wrap nearby parts with water-soaked cloths to protect them from heat damage during repairs.
(c) If a solder joint requires repair, disassemble the joint and clean away any refrigerant oil which may be present;
oil traces prevent making leak-proof solder repair. After cleaning, reassemble the parts and solder.
d) Reassemble and tighten any connections previously loosened.
(e) After opening the plumbing system for repair, evacuate the system previously open to a vacuum of 750 microns.
Add refrigerant gas until pressure within the system is at least 5 psig. Follow with dry nitrogen to raise pressure
to 150 psig.
(f) Open all previously closed valves.
(g) Perform a pressure check for leaks as previously discussed.
Summary of Contents for MAC-240
Page 1: ...MOBILE AIR CONDITIONING SYSTEM Model MAC 240 INSTALLATION OPERATION MAINTENANCE MANUAL...
Page 9: ...8 D Alarms Shutdowns...
Page 15: ...14 SCHEMATIC REFRIGERATION DIAGRAM...
Page 44: ...43 10 EQUIPMENT DIMENSIONAL DETAILS Model No MAC240FZ600...
Page 45: ...44 11 MAIN CONTROL PANEL COMPONENT LAYOUT...
Page 46: ...45 12 MAIN CONTROL PANEL COMPONENT PARTS LIST...
Page 56: ...55 16 UNIT OVERALL VIEW...
Page 57: ...56 UNIT REAR SIDE GENERATOR SECTION...
Page 58: ...57 OPTIONAL DOWN DISCHARGE PLENUM EXTENSION FLEXIBLE DUCT STORAGE BOX...
Page 59: ...58 DIESEL FILLING POINT FUEL GAUGE...
Page 60: ...59 COIL SECTION...
Page 61: ...60 FAN MOTOR ASSEMBLY...
Page 62: ...61 CONDENSER SECTION...
Page 63: ...62 OPERATIONAL PANEL...
Page 64: ...63 MAIN CONTROL BOX...
Page 65: ...64 VFD GENERATOR...
Page 66: ...65 GENERATOR DISPLAY PANEL...
Page 67: ...66 GENERATOR SECTION...