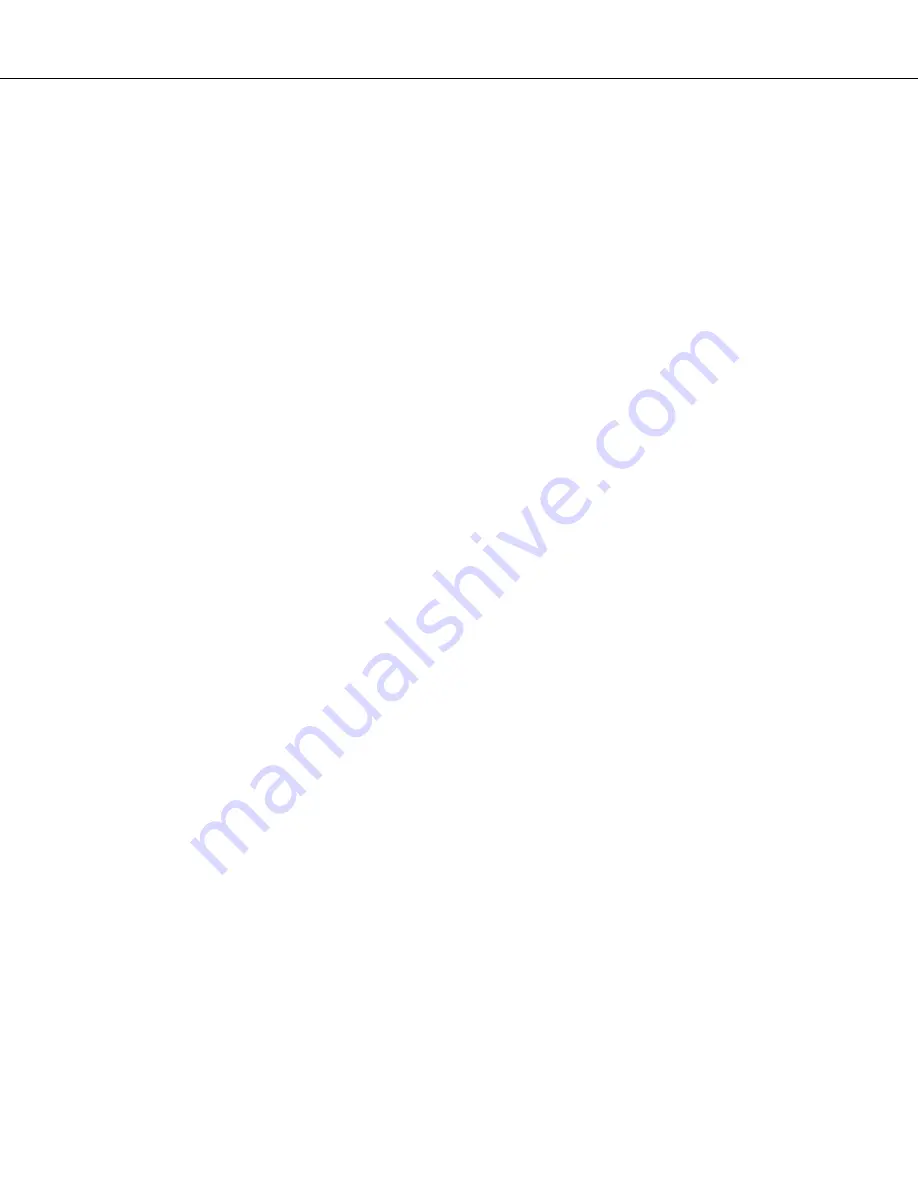
26
The description and function of the sensors are as follows:
a) Air Velocity Sensor – The function of this sensor is to measure the air velocity (mass flow). The working range air
velocity is adjustable up to 20 m/s. Output signal is 0~10V range and transmitted to the microprocessor board which
will in turn send to the VFD for supply fan speed control.
b) Ambient and (5) Supply Air Temperature Sensor – These sensors are PTC type sensors measuring the temperature
of the ambient and supplied air for cooling control. Resistance value is 1Kohm @ 25
0
C.
c) Air Differential Sensor – The function of this sensor is to measure the static pressure (air duct) of the supplied air. The
signal is transmitted to the microprocessor board for cooling and supply fan speed control. Output signal is 0~10V and
differential pressure range is 0~0.1 Bar.
d) Air Flow Switch – This is a SPDT switching type device sensing supply air flow.
e) Discharge Pressure Switch - This is a SPDT switching type device sensing the refrigerant pressure in the discharge
line. It’s function is to stop the compressor from operation at a predetermined pressure (high discharge pressure).
f) Suction and Discharge Pressure Transducers – These are transducer type sensor device with a 4~20ma output
signal. These sensors are fixed in the suction and discharge lines to measure the pressure and transmit the informa-
tion to the processor board. These signals are then processed for safeties function (low suction or high discharge
pressures) and for pressure readings display on the user interface board.
5. STARTING-UP AND SHUTTING DOWN SEQUENCE
Before initiating the start-up sequence, ensure that the emergency stop push button switches are in “pulled” position. The
following steps are to be taken in starting the mobile AC equipment.
5.1 VISUAL INSPECTION OF EQUIPMENT (CHECK LIST)
Before initiating start-up sequence of the unit please check the following points to ensure safe and reliable operation:
a) Check generator engine oil level. Remove engine oil dipstick and check oil level mark on it. Add oil to bring it to “full level” mark.
CAUTION: NEVER OPERATE THE ENGINE WITH THE OIL LEVEL BELOW THE LOW MARK OR ABOVE HIGH
MARK. WAIT AT LEAST 5 MINUTES AFTER SHUTTING OFF THE ENGINE TO CHECK THE OIL. THIS ALLOWS
TIME FOR THE OIL TO DRAIN TO THE OIL PAN.
b) Visually inspect fuel lines and fittings for evidence of fuel leakage. Inspect valve covers, oil pan, and cylinder block for
evidence of oil leakage. Do the necessary correction if leakage is observed.
c) Remove any storage cover, loose hardware or debris found inside the generator and compressor section of the
equipment that may be drawn into the exhaust or condenser fans during operation.
d) Check the engine fuel level (press the fuel level switch and observe the fuel gauge).
WARNING: CHECKING THE FUEL LEVEL IS ADVISED TO BE DONE ONLY WHEN GENERATOR ENGINE IS IN
“STAND-BY” MODE – GENERATOR NOT RUNNING AND DC BATTERY SWITCHED “ON”. IN CASE THE OPERA-
TOR DECIDES TO CHECK THE FUEL LEVEL WHILE THE GENERATOR IS IN OPERATION, THE CONTROLS MAY
STOP THE ENGINE IF THE PUSH-TO-CHECK SWITCH IS NOT PRESSED PROPERLY.
e) Inspect the air conditioning lines and fittings for evidence for breaks or potential failure.
f) Inspect the compressor unit and system components for evidence of oil leakage.
g) Inspect the air conditioner duct for loose connections, leaks, cuts or abrasion that may lead to premature failure during operation.
NOTE: TO CHECK THE REFRIGERANT CHARGE LEVEL FOR THE AIR CONDITIONER, THE UNIT MUST BE
OPERATING. THIS REQUIRES PERFORMING ALL OTHER PREOPERATIONAL CHECKS PRIOR TO START-
ING THE UNIT TO CHECK THE REFRIGERANT CHARGE. IF DESIRE, CHECK THE REFRIGERANT CHARGE
DURING THE FIRST USE OF THE UNIT EACH DAY.
h) Inspect the sight glasses for proper charge level with the unit running, the liquid line sight glasses should show full liquid.
i) Close all the unit access doors.
WARNING: NEVER ENTER THE INTERIOR OF THE UNIT WHILE UNIT IS IN
OPERATION. DO
NOT STEP ON OR
GRAB HOLD OF WIRING OR REFRIGERANT PIPING.
Summary of Contents for MAC-240
Page 1: ...MOBILE AIR CONDITIONING SYSTEM Model MAC 240 INSTALLATION OPERATION MAINTENANCE MANUAL...
Page 9: ...8 D Alarms Shutdowns...
Page 15: ...14 SCHEMATIC REFRIGERATION DIAGRAM...
Page 44: ...43 10 EQUIPMENT DIMENSIONAL DETAILS Model No MAC240FZ600...
Page 45: ...44 11 MAIN CONTROL PANEL COMPONENT LAYOUT...
Page 46: ...45 12 MAIN CONTROL PANEL COMPONENT PARTS LIST...
Page 56: ...55 16 UNIT OVERALL VIEW...
Page 57: ...56 UNIT REAR SIDE GENERATOR SECTION...
Page 58: ...57 OPTIONAL DOWN DISCHARGE PLENUM EXTENSION FLEXIBLE DUCT STORAGE BOX...
Page 59: ...58 DIESEL FILLING POINT FUEL GAUGE...
Page 60: ...59 COIL SECTION...
Page 61: ...60 FAN MOTOR ASSEMBLY...
Page 62: ...61 CONDENSER SECTION...
Page 63: ...62 OPERATIONAL PANEL...
Page 64: ...63 MAIN CONTROL BOX...
Page 65: ...64 VFD GENERATOR...
Page 66: ...65 GENERATOR DISPLAY PANEL...
Page 67: ...66 GENERATOR SECTION...