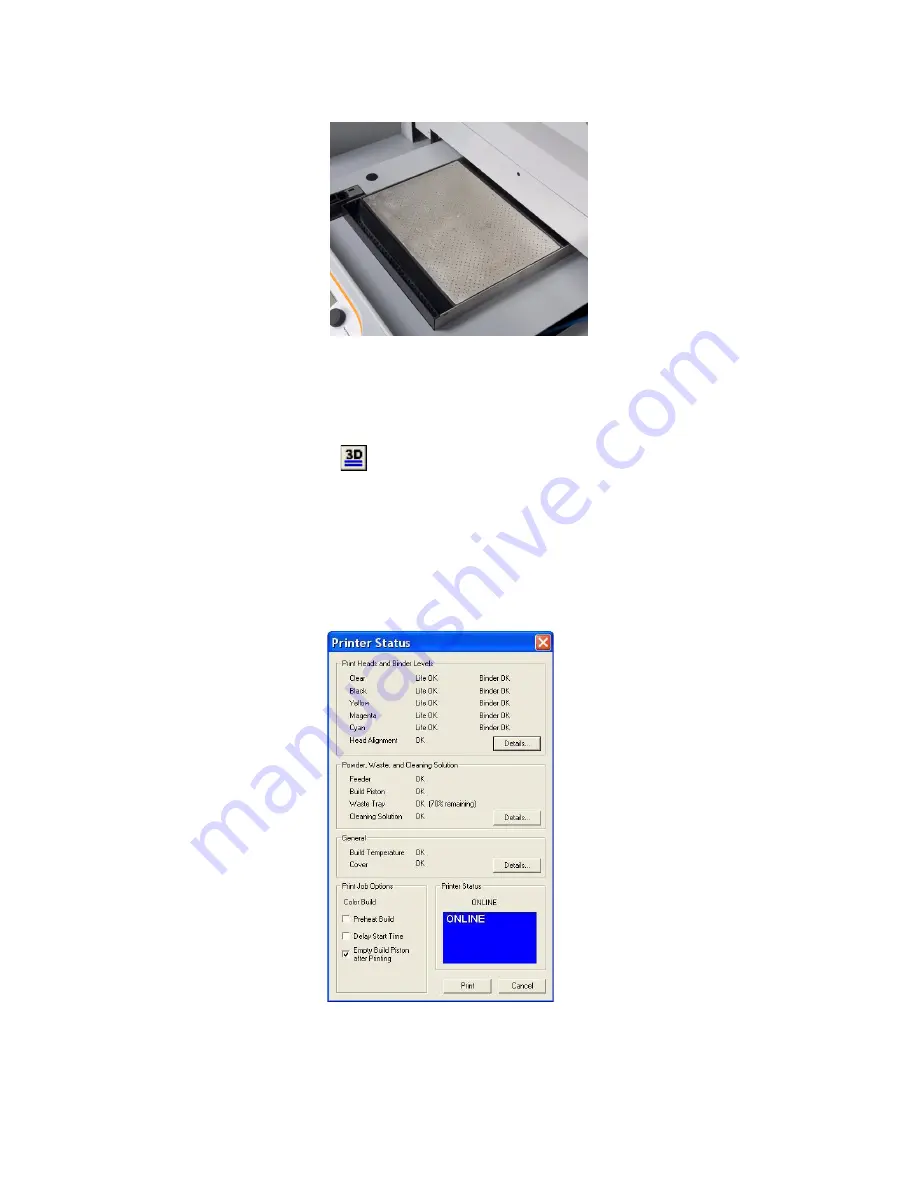
ZPrinter
®
650 Hardware Manual
Setup And Print The Build
zcentral.zcorp.com
31
All Rights Reserved
10/21/08
A clean, properly prepared Build Bed
2.13 Print the Build
1. Select
File >
3D Print
, or click
on the Toolbar, to display the
Printer Status
dialog.
NOTE:
ZPrint checks the printer readiness and calculates the materials needed to complete the
build. The results are reported in the
Printer Status
dialog for you to check before starting the
build.
•
The dialog shows
OK
for each item and the
button is enabled when the printer is ready.
•
If you see a message and the
button is not available for selection, see
Chapter 5 - Additional
Operations
for instructions on how to clear a message.
2. Choose your options for the build in the
Print Job Options
section of the
Printer Status
dialog.