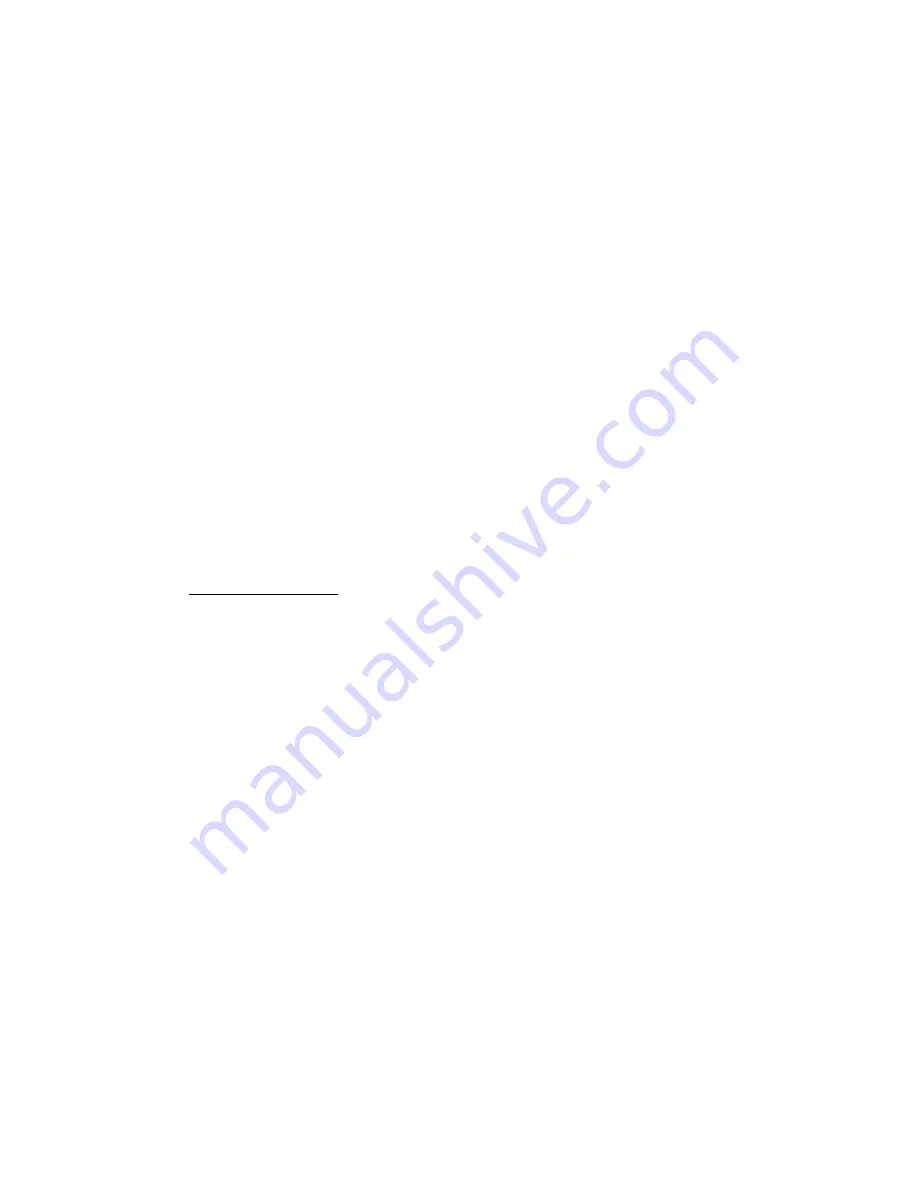
Z
Corporation
Z810
System
User
Manual
www.zcorp-users.com
32
3.7.1.2
Gross and Fine Depowdering
•
Become familiar with where the parts are placed and how they are oriented in the build
box so you do not accidentally bump or brush against a fragile part during the
depowdering process.
•
When performing the gross depowdering (removal of excess powder in the build box) do
not plunge the vacuum nozzle into the powder bed. Begin at the outer perimeter of the
build box, slowly work your way into the build. Hold the tip of vacuum nozzle
approximately 0.25” (6.4 mm) to .375” (9.5 mm) away from the powder and allow the
vacuum to pull the powder up. Slanting the vacuum nozzle will enable you to control the
suction. This will decrease the chance of breaking a part that is hidden beneath the
surface of the powder.
•
While fine depowdering in the depowderer, always start with a low air pressure and
gradually increase the pressure as the fine details and features of the part become
visible. When the top and sides of the part are completely depowdered tilt the part onto
one of its sides. Handle the part carefully. The part may be fragile and brittle before
infiltration. If none of the sides of the part will be able to support the weight of the part
you can apply a small amount of resin or epoxy to strengthen it. You want to be careful
not to let any of the infiltrant come into contact with any unprinted powder that may still be
on the part. Let the infiltrant dry before continuing to depowder.
3.7.1.3
Oven Dry the Part
•
Although the part can be handled when it is not completely dried, the part reaches full
strength when dried. Placing the part in an oven at temperatures less than 200
°
F (93
o
C)
for 2-4 hours will increase the strength of the part. This is only recommended for plaster-
based powders.
3.7.2 PART
INFILTRATION
3.7.2.1
When Using Z-Bond
TM
Resin
•
Always infiltrate the most delicate features of the part first. Z-Bond resin gives almost
immediate strength to the area of the part that has been infiltrated. As you handle the
areas of the part that have been infiltrated it will be less likely to break it.
•
Try to avoid infiltrating the part by applying Z-Bond resin from spot to spot. Pick a good
starting place and hold that area upward relative to the rest of the part. With your free
hand, place the tip of the Z-Bond bottle against the part and allow the cyanoacrylate (CA)
to flow from the bottle. It is important that the CA flows at a uniform rate making it easier
for you to judge how quickly it will flow from the tip of the bottle before it wicks into the
part. By seeing how quickly it wicks into the part you will be able to judge where and how
quickly to move the tip of the bottle while applying the CA, being sure not to apply the CA
to the same place more than once.
3.7.2.2
When Using a Z-Snap
TM
or Z-Max
TM
Epoxy
•
If the part has delicate features, infiltrate them last as the feature will be less strong after
being infiltrated until the epoxy begins to cure. This will decrease the chance the feature
will break from the part if nudged or bumped.
•
If the part has multiple delicate features or it is impossible to handle the part without
breaking a feature you may infiltrate these features only. Allow the Z-Snap or Z-Max
epoxy to cure. Then infiltrate the rest of the part. This will add time to post-processing
the part but it ensures that you have a good strong part without any fractures.