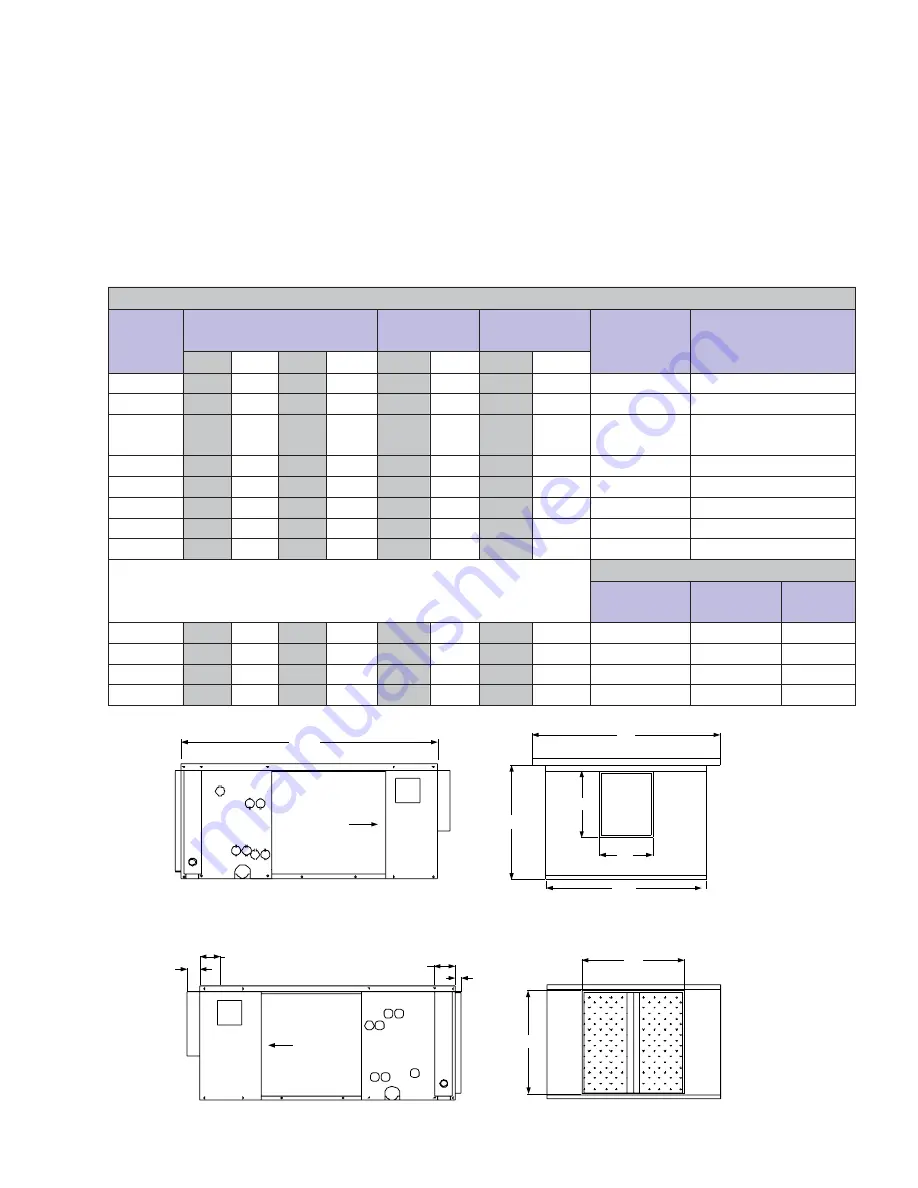
INSTALLATION
• Never insulate the heads or motorized portion of
control valves. Damage can occur in the form
of excessive heat build up and interference to the
operation and moving parts may result.
• All piping fabricated in the fi eld should be installed
with consideration of additional space for any
electrical routing that may be required.
• Connect all piping per accepted industry standards
GENERAL DIMENSIONS
MODEL
UNIT CABINET
BLOWER
OUTLET
RETURN DUCT
CONNECTION
FILTER SIZE
MANIFOLD
CONNECTION
AA
BB
CC
DD
EE
FF
GG
HH
24YSHW4
37
32-1/2
27
18-7/8
8-3/4
10-7/8
18
16-1/4
16 X 25
7/8 ODS.
36YSHW4
37
42
36-1/2
18-7/8
12-1/4
10-7/8
27-1/2
16-1/4
16 X 16 (2)
7/8 ODS.
48YSHW4
39
43-1/2
38
22-7/8
13-5/8
11-7/8
29
20-1/4
16 X 20 (2)
7/8 ODS.
60YSHW4
42
50-1/2
45
22-7/8
16
13-7/8
36
20-1/4
20 X 20 (2)
1-1/8 ODS.
24YSHW6
37
32-1/2
27
18-7/8
8-3/4
10-7/8
18
16-1/4
16 X 25
7/8 ODS.
36YSHW6
37
42
36-1/2
18-7/8
12-1/4
10-7/8
27-1/2
16-1/4
16 X 16 (3)
7/8 ODS.
48YSHW6
39
43-1/2
38
22-7/8
13-5/8
11-7/8
29
20-1/4
16 X 20 (3)
7/8 ODS.
60YSHW6
42
50-1/2
45
22-7/8
16
13-7/8
36
20-1/4
20 X 20 (2)
1-1/8 ODS.
4 ROW COIL
FILTER SIZE
LIQUID
(SWEAT)
SUCTION
(SWEAT)
24YSHX4
37
31
27
18-7/8
8-3/4
10-7/8
18
16-1/4
16 X 25
3/8 ODS.
3/4 ODS.
36YSHX4
37
40-1/2
36-1/2
18-7/8
12-1/4
10-7/8
27-1/2
16-1/4
16 X 16 (2)
3/8 ODS.
3/4 ODS.
48YSHX4
39
42
38
22-7/8
13-5/8
11-7/8
29
20-1/4
16 X 20 (2)
1/2 ODS.
7/8 ODS.
60YSHX4
42
49
45
22-7/8
16
13-7/8
36
20-1/4
20 X 20 (2)
1/2 ODS.
7/8 ODS.
FIG 4 - DIMENSIONS FOR 2 - 5 TON UNITS
DD
EE
FF
CC
BB
2.00
3.50
3.50
1.00
AIR FLOW
HH
GG
AIR FLOW
AA
Note: The 3.50” dimension locates the 7/8” knock outs for mounting rods.
and observe all regulations governing installation of
piping systems. When all connections are complete,
the system must be pressure tested. Repair any
solder joint leaks and gently tighten any leaking
valve packing nuts and piping accessories as
required. Hydronic systems are not designed to
hold pressurized air and should only be tested with
water.
5
YORK INTERNATIONAL
FORM 115.22-NOM5 (704)