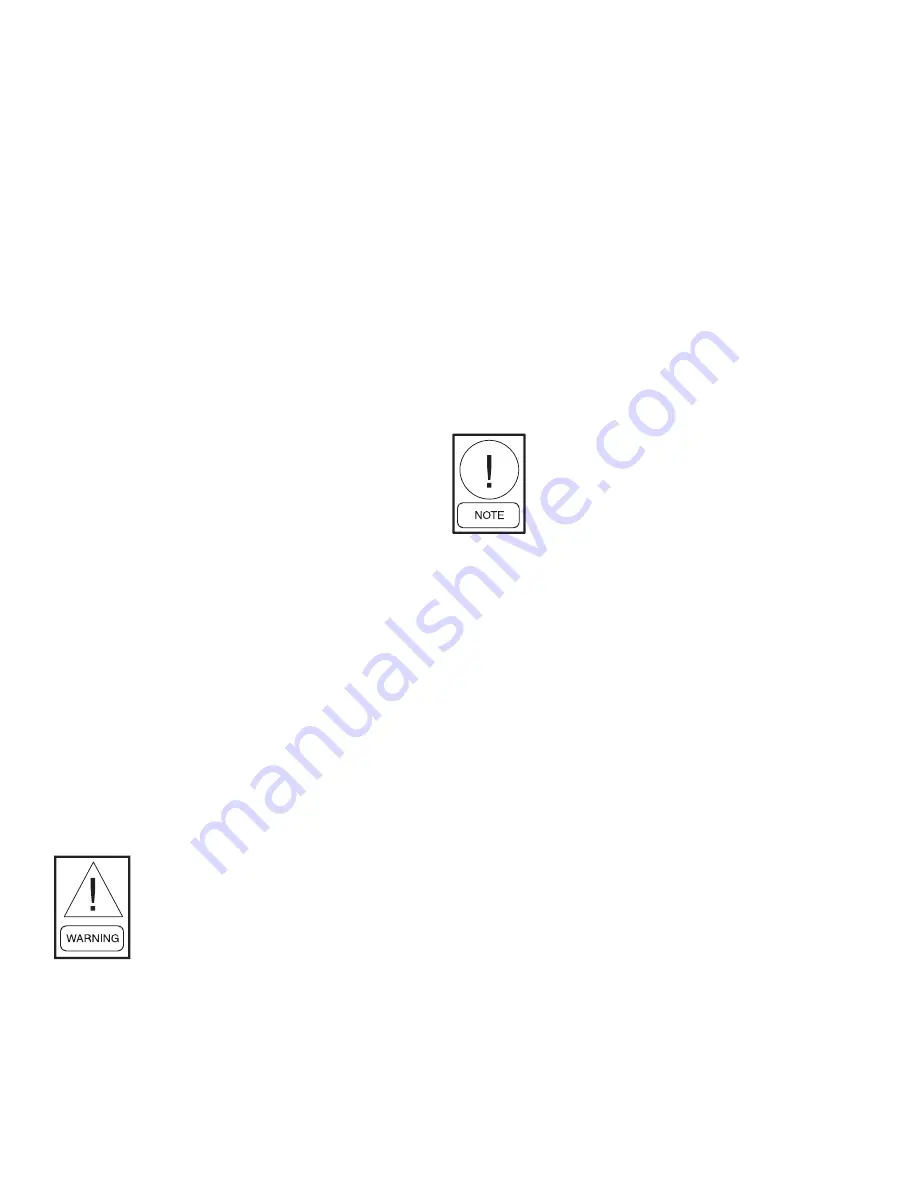
INSTALLATION
F
or piping guidelines, see the most recent issue of
Form 050.40-ES3.
Condensate drain lines must be installed with adequate
slope away from the unit to assure positive drainage.
Since the drain pan is located on the suction side of
the blower, a negative pressure exists at the drain pan
and a minimum trap of 1-1/2 inches must be provided
in the drain line to assure proper drainage. Drain pan
has positive slope to the nipple, which is located on
the coil connection side of the unit.
PIPING INSULATION
After the system has been proven leak free, all lines
and valve control packages must be insulated to pre-
vent condensate drippage or insulated as specifi ed on
the building plans.
Many valve packages will not physi-
cally allow all components to fi t over
an auxiliary drain pan. It is the in-
stallers responsibility to capture all
condensation or insulate the piping
to prevent condensation.
GENERAL PIPING PRECAUTIONS
• Clean all fi eld piping prior to connection to remove
all debris.
• Use wet cotton rags to cool valve bodies, if present,
when soldering.
• Open all valves (mid-way for hand valves, manually
open on motorized valves) prior to soldering.
• When soldering to bronze or brass, heat the piping
while in the socket/cup and begin introducing the
solder when the fl ux boils rapidly. Avoid direct
fl ame into the solder joint.
• Heat can only be applied to the cup of the valve body
for a minimal time before damage occurs (even with
the use of wet rags.
• Avoid rapid quenching of solder joints as this will
produce joints of inferior quality.
• The coil header or valve package will not support
the weight of the connecting pipes. All pipes,
which are connected to the unit, must be completely
supported prior to connection to the unit.
• Provisions must be made for expansion and
contraction of piping systems. All horizontal and
vertical risers, including runouts, must be able to
withstand signifi cant movement with temperature
changes. Failure to do so will result in damage and
failure of piping, fi ttings and valves throughout the
building.
CONTROL WIRING
These blower coil units can be provided with an
optional class 2 relay/transformer for 24-volt control
circuits (3/4 HP maximum load rating). Should any
add-on equipment also have a Class 2 transformer fur-
nished, care must be taken to prevent interconnecting
outputs of the two transformers by using a thermostat
with isolating contacts.
DRAIN PIPING
Unit models incorporate a positive slope drain pan
with a ¾” NPT nipple that exits the unit on the side
of the coil header connections. All units need to be
leveled to insure positive slope toward the condensate
drain nipple.
AIR DISTRIBUTION DUCT WORK
All duct work must be installed in accordance with
national fi re protection Association codes 90A and
90B. Ducts should be adequately insulated to prevent
condensation during the cooling cycle and to minimize
heat loss during the heating cycle. All return air must
be fi ltered to prevent dirt buildup on the coil surface.
In many cases, it is acceptable to use ducting of the
same size as the blower coil return air connection.
However, unique arrangements or long duct runs, must
be confi rmed by a local professional.
PIPING
YSHW units employ a hydronic coil designed for use
with either hot or chilled water. Each coil has a 1/4
inch bleed line.
All piping must be adequately sized to meet the design
water fl ow requirements as specifi ed for the specifi c
installation. Piping must be installed in accordance
with all applicable codes. All chilled water piping
must be insulated to prevent condensation.
YSHX units have a DX coil for use with cooling or
heat pump condensing units (2-5 Ton only).
When connecting piping or valve kits
to blower coil units, do not bend or
reposition the coil header tubing for
alignment purposes. This could cause
a tubing fracture resulting in a water
leak when water pressure is applied to
the system. All units have knockouts
on both sides for either right or left
side coil stubouts.
The piping connections on the equipment
(see Figure
4 & 5)
are not necessarily indicative of the proper
supply and return line sizes. All units have knockouts
on both sides for either right or left side coil stubouts.
YORK INTERNATIONAL
4
FORM 115.22-NOM5 (704)