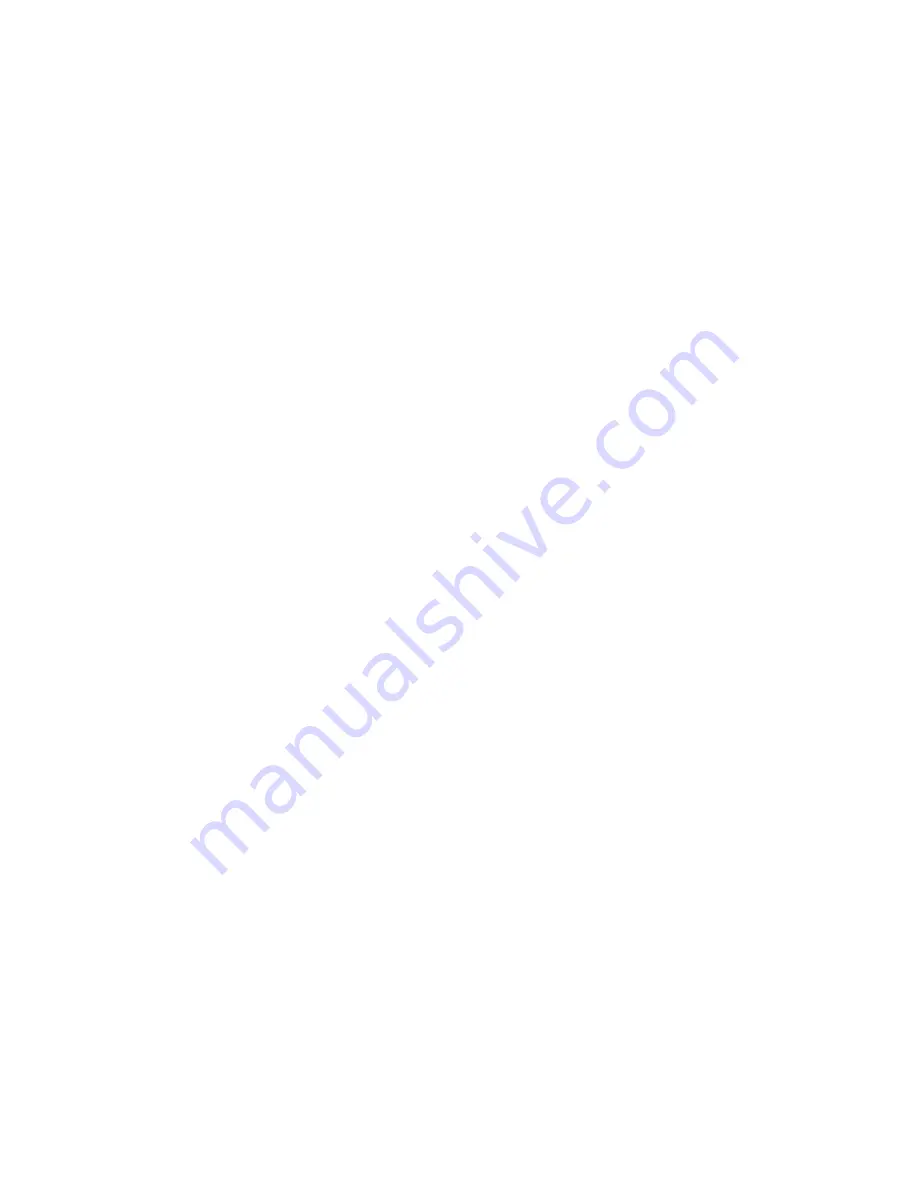
FORM 150.60-NM3
73
YORK INTERNATIONAL
4.
Operating Pressures and Temperatures
Check
to see that operating pressures and temperatures
are within the LIMITATIONS shown in this book.
ANNUAL MAINTENANCE
It is recommended that the following items be checked
annually.
1. All items under WEEKLY MAINTENANCE.
2.
Operating Controls
Check to see if controls are
set and operating within the proper limits. See Unit
Controls and OPERATION section of this book.
3.
Compressor Oil
Drain, inspect and refill with
new oil. This requires pumping out the compressor.
If possible, this should be done after the unit has
been in operation for some time, when the oil in the
crankcase will contain the least amount of refriger-
ant. To pump out the compressor, proceed as fol-
lows:
A. Close the suction stop valve.
B. Open the discharge stop valve two turns of the
stem.
C. Operate the compressor until 15 to 20 inches
vacuum is obtained. Do this by disconnecting
the wiring to LLSV and repeatedly starting the
compressor. Recycle 115VAC power to the
Logic Panel to reduce anti-recycle time to 2
minutes if needed. The compressor should in no
case be operated under vacuum conditions for
longer than 10 to 15 seconds.
D. Stop the compressor and immediately close the
discharge stop valve. The procedures outlined in
steps (b) and (c) above should be repeated if the
suction pressure rises rapidly to 15 PSIG or
more which would indicate considerable refriger-
ant remaining in the crankcase oil. Do not ex-
pect to retain 0 PSIG since some refrigerant will
continually be released from the oil in the crank-
case.
E. After pumping down the compressor, wait until
the pressure builds up to 2 or 3 PSIG before
opening up any part of the hermetic compres-
sor.
F. Open the coil drain valve slowly and drain as
much oil from the compressor as possible.
G. Examine the oil for any metal particles which
would indicate wear on the bearings, crankshaft
or connecting rods. If metal particles are found,
the need for closer examination by factory ser-
vice personnel is indicated.
H. If the oil is clean and free of metal particles, refill
the compressor with YORK oil C. To add oil or
to fill the compressor crankcase, connect the
delivery tube of the YORK Hand Oil Pump.
YORK Part No. 470-10654 or equal to the com-
pressor oil charging and drain valve. Expel all air
from the delivery tube by pumping it full of oil,
allowing a few drips to drip out before tightening
the flare nut to the oil charging valve. Then open
the oil charging valve and pump oil into the
crankcase to the proper level. It is necessary
that the suction end of the hand oil pump be
kept submerged under the oil level in the con-
tainer at all times, to avoid entrance of air into
the compressor.
I. Before opening the suction or discharge stop
valves, connect a vacuum pump to the pumpout
port in the discharge stop valve. (Pumpout port
is port on valve stem side of valve). With the
vacuum line shutoff valve open, run the vacuum
pump until a vacuum of at least 1000 microns is
reached. Stop the vacuum pump, close the
shut-off valve and open the discharge valve fully
before disconnecting the line from the vacuum
pump. Disconnect the vacuum pump and re-
place the plug in the pumpout port.
NOTE: If suction or discharge valves are not
seated properly, a 1000 micron vacuum
can not be obtained. Do not evacuate
for long periods of time.
J. Be sure both discharge and suction stop valves
are open before operating the unit.
4.
Suction and Discharge Valves
The condition of
the suction and discharge valves should be checked
by YORK service personnel.
Summary of Contents for YCAJ44HE8
Page 16: ...16 YORK INTERNATIONAL WIRING DIAGRAMS LD02165 FIG 5 ELEMENTARY DIAGRAM...
Page 17: ...FORM 150 60 NM3 17 YORK INTERNATIONAL FIG 5 ELEMENTARY DIAGRAM Cont d LD02166...
Page 20: ...20 YORK INTERNATIONAL CONNECTION DIAGRAM ELECTRICAL BOX FIG 7 CONNECTION DIAGRAM LD02171...
Page 21: ...FORM 150 60 NM3 21 YORK INTERNATIONAL FIG 7 CONNECTION DIAGRAM Cont d LD02172...