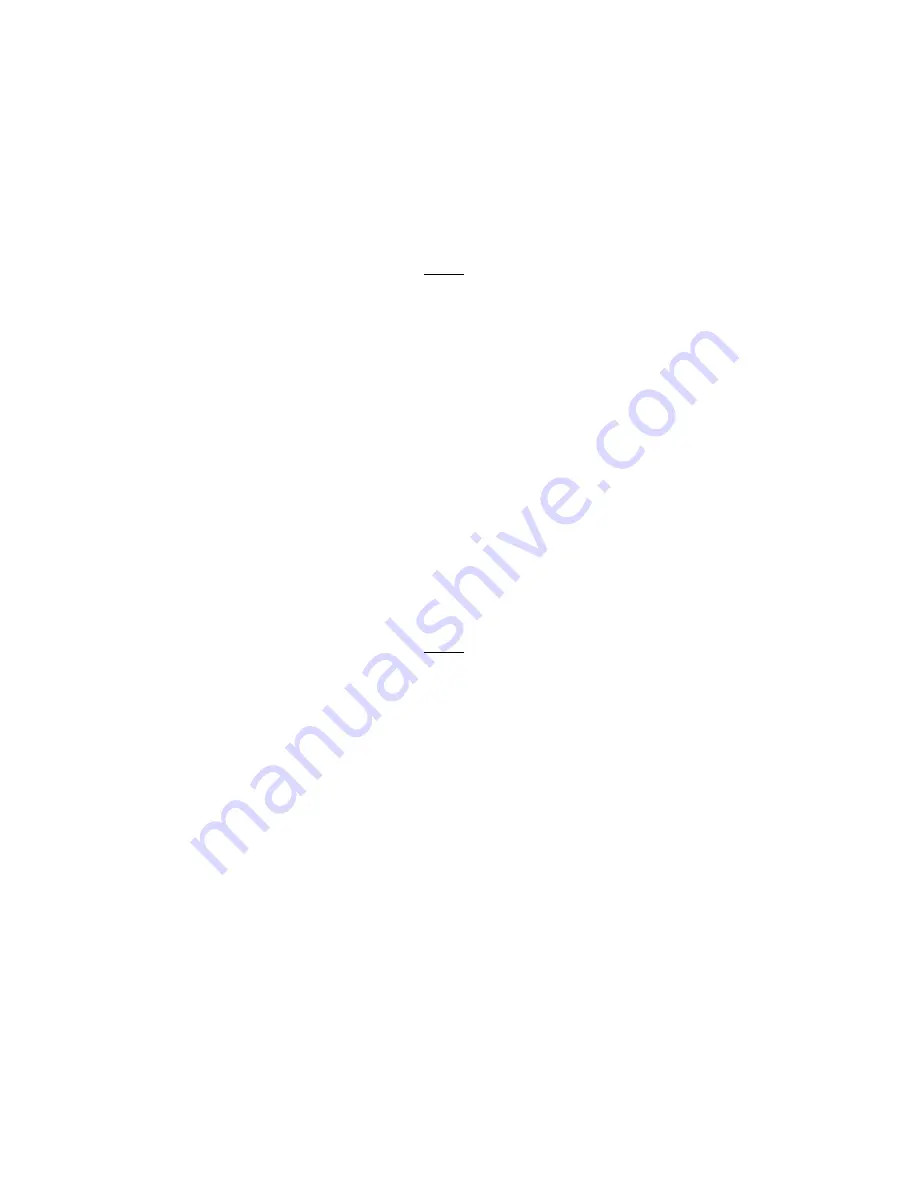
FORM 150.60-NM3
71
YORK INTERNATIONAL
The subcooling temperature should be taken by record-
ing the temperature of the liquid line at the outlet of the
condenser and recording the liquid line pressure at the
liquid stop valve and converting it to a temperature from
temperature/pressure chart.
Example:
LIQUID LINE PRESSURE
202 PSIG converted to
102°F
Minus Liquid Line Temperature
- 87°F
Subcooling =
15°F
After the subcooling is set at 10° - 15°F the superheat
should be checked.
The superheat should be checked only after steady op-
eration of the chiller has been established, the leaving
chilled liquid has been pulled down to the required tem-
perature, and the unit is running fully loaded. Correct su
perheat setting is 12° - 15°F.
The superheat is the difference between the actual tem-
perature of the returned refrigerant gas entering the com-
pressor and the temperature corresponding to the suc-
tion pressure as shown in a standard pressure/tem-
perature chart.
Example:
Suction Temperature
46°F
Minus Suction Pressure 60 PSIG
Converted to Temperature
- 34°F
Superheat
12°F
The suction temperature should be taken 6" before the
compressor service valve, and the suction pressure is
taken at the compressor suction service valve.
Normally, the thermal expansion valve need not be ad-
justed in the field. If, however, an adjustment is to be
made, the expansion valve adjusting screw should be
turned not more than one turn at a time, allowing suffi-
cient time (approximately 15 minutes) between ad-
justments for the system and the thermal expansion
valve to respond and return to settled operation.
If the unit has been functioning satisfactorily during the
initial operating period, it is ready for continuous opera-
tion.
*
Leak check compressors, fittings, and piping to as-
sure no leaks are present from improper handling.
OPERATING SEQUENCE
NOTE: The operating sequence described below re-
lates to operation after power has been applied
on a hot water start (such as start-up commis-
sioning). Under these circumstances, loading
will deviate from normal sequence and timing
previously described. When a compressor
starts, internal timers limit minimum time before
another compressor can start to 1 minute. Time
between stages of loading is also limited by in-
ternal timers to a minimum of 1 minute, al-
though the micro would like to load at 30 sec-
onds intervals which may cause the lag com-
pressor to start before the lead system fully
loads optional steps. This also deviates from
the normal sequence of loading. If rate control
dictates, time between stages of loading maybe
up to 150 seconds or may not occur at all. This
will be determined by rate control programming
and actual water temperature rate of change.
1. For the system compressors to run, all Manual Re-
set Cut-outs must be reset, the Flow Switch must
be closed, any remote cycling contacts must be
closed, the System Switches must be ON, the Daily
Schedule must be scheduling the chiller to run, and
temperature demand must be present.
2. As long as power is applied, the Crankcase Heaters
will be on and stay on as long as the compressors
are not running.
3. When power is applied to the system, the micro-
processor will start a 2 minute timer. This is the
same timer that prevents an instantaneous start af-
ter a power failure.
4. At the end of the 2 minute timer, the microprocessor
will check for cooling demand as well as check to
see if any system safeties are exceeded. If all condi-
tions allow for start, the lead compressor will start
unloaded. Coincident with the start, the pro-
grammable anti-recycle timer will be set and begin
counting downward to 0. The liquid line solenoid
valve will open when the system is pumped down to
the suction pressure cut-out (Pumpdown on startup).
5.
After 4 seconds of run time,
the motor current of
the lead compressor must be >14% FLA and
<115% FLA. Oil pressure must be 5 PSID or
greater. If these conditions are not met, the lead
compressor will shut down.
6.
After 30 seconds of run time,
the oil pressure of
the lead compressor must be a minimum of 20 PSID
and the suction pressure must be a minimum of
50% of cut-out.
7.
After 60 seconds of run time,
if cooling demand
requires and no safeties have been exceeded, the
lead compressor will load, if cooling demand (tem-
perature and rate control) requires.
Summary of Contents for YCAJ44HE8
Page 16: ...16 YORK INTERNATIONAL WIRING DIAGRAMS LD02165 FIG 5 ELEMENTARY DIAGRAM...
Page 17: ...FORM 150 60 NM3 17 YORK INTERNATIONAL FIG 5 ELEMENTARY DIAGRAM Cont d LD02166...
Page 20: ...20 YORK INTERNATIONAL CONNECTION DIAGRAM ELECTRICAL BOX FIG 7 CONNECTION DIAGRAM LD02171...
Page 21: ...FORM 150 60 NM3 21 YORK INTERNATIONAL FIG 7 CONNECTION DIAGRAM Cont d LD02172...