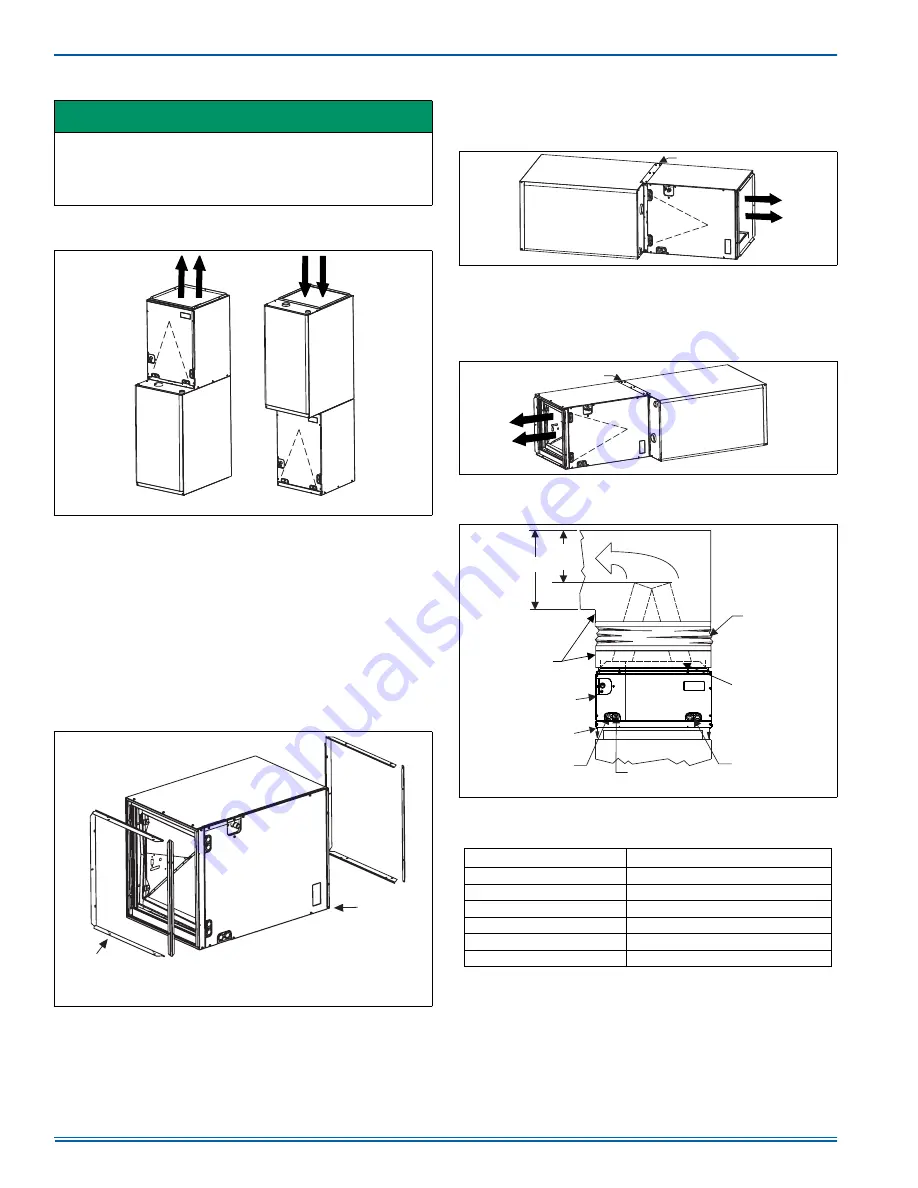
5402847-UIM-A-0917
6
Johnson Controls Unitary Products
COIL INSTALLATION
COIL/FURNACE ASSEMBLY - MC/FC/PC SERIES
COILS
FURNACE ASSEMBLY - MC & FC SERIES COILS
These coils are factory shipped for installation in either upflow or down-
flow applications with no conversion.
Position the coil casing over or under the furnace opening as shown in
Figure 2 after configuring coil flanges as required see “Coil Flange” sec-
tion below.
COIL FLANGE INSTALLATION
The coils include removable flanges to allow proper fit up with furnaces
having various inlet and outlet flange configurations. The two flanges
are attached to the top of the coil in the factory during production. For
proper configuration of flanges refer to Figure 3.
FURNACE ASSEMBLY - MC SERIES COILS ONLY
MC coils are supplied ready to be installed in a horizontal position. A
horizontal pan is factory installed. MC coils should be installed in all hor-
izontal applications with the horizontal drain pan side down.
For horizontal left hand applications no conversion is required to an MC
coil when used with a downflow/horizontal furnace. A mounting plate,
supplied with every coil should always be installed on the side desig-
nated as top side. See Figures 4 & 5.
FURNACE ASSEMBLY - PC SERIES COILS
Dimension “C” should be at least 2/3 of dimension “D”. See Figure 6.
IMPORTANT
On all installations without a coil, a removable access panel is recom-
mended in the outlet duct such that smoke or reflected light would be
observable inside the casing to indicate the presence of leaks in the
heat exchanger. This access cover shall be attached in such a man-
ner as to prevent leaks.
FIGURE 2:
Vertical Applications
FIGURE 3:
Coil Flange
UPFLOW
DOWNFLOW
Furnace
Furnace
ALTERNATE
FLANGE LOCATION
(Used for downflow or
horizontal left installations)
FACTORY
FLANGE
LOCATION
(Used for upflow
or horizontal
right installations)
FIGURE 4:
Horizontal Right Application
FIGURE 5:
Horizontal Left Application
FIGURE 6:
PC Series Upflow Coil Installation
Table 2:
Coil Projection Dimensions - PC Series Coils
COIL SIZE
DIMENSION “C” INCH
PC18
3-1/2
PC24
4-1/2
PC30, PC32, PC35
4-1/2
PC42, PC43, PC36, PC37
5-1/2
PC48
6-1/2
PC60
9
Furnace
Mounting Plate
Furnace
Mounting Plate
Flexible
Duct Collar
Do not drill
or Screw
this flange
Field
Fabricated
Ductwork
Upflow
Coil
Upflow
Furnace
Secondary
Drain
Primary
Drain
D
C
(Min)
Alternate
Drain Location