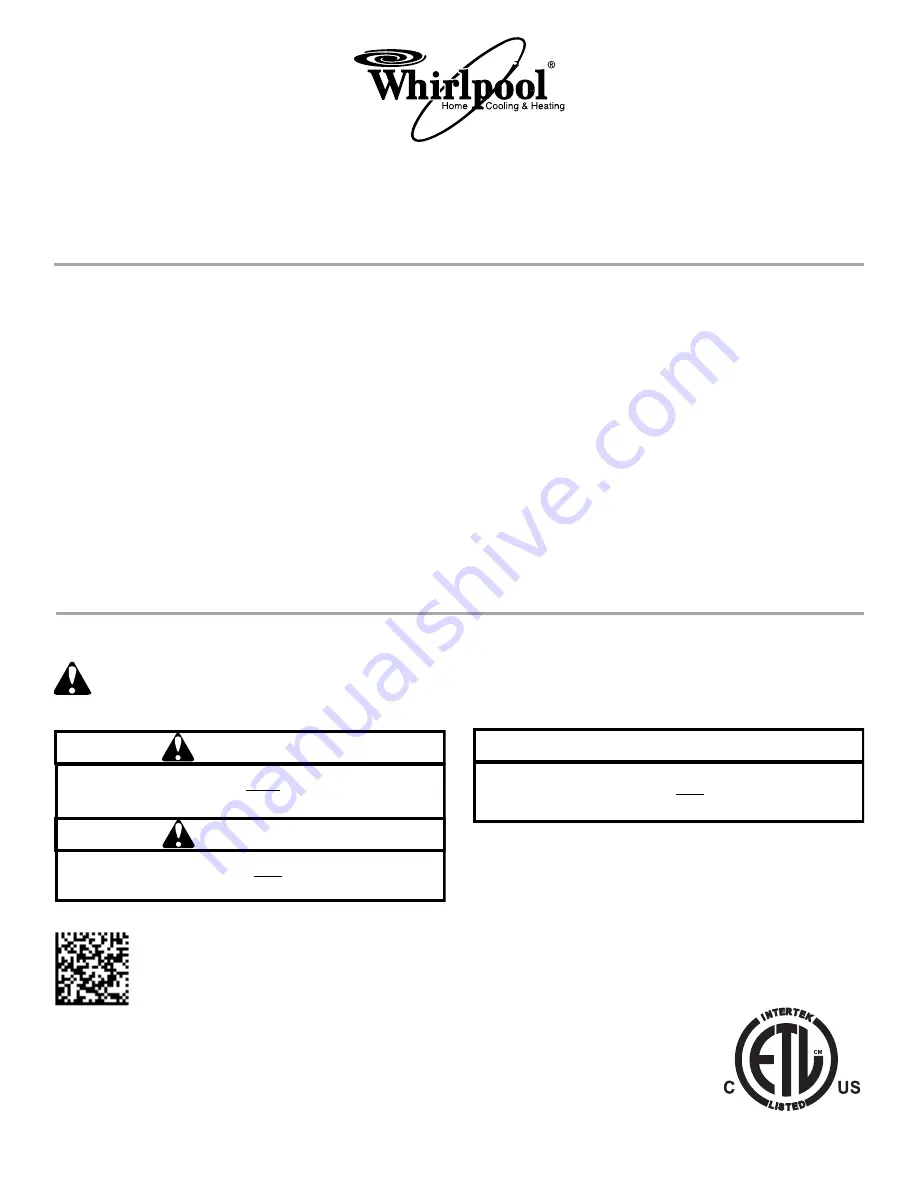
PACKAGE GAS ELECTRIC FURNACES
INSTALLATION INSTRUCTIONS
GAS FURNACE SAFETY
Recognize this symbol as a safety precaution.
Please adhere to the following warnings and cautions when installing, adjusting, altering, servicing or operating the furnace.
Table of Contents
GAS FURNACE SAFETY................................................................1
INSTALLATION REQUIREMENTS ................................................4
Tools and Parts ............................................................................4
Location Requirements ................................................................4
Ductwork Requirements ..............................................................6
Filter Requirements ......................................................................6
Electrical Requirements ...............................................................7
Gas Supply Requirements ...........................................................7
INSTALLATION INSTRUCTIONS ..................................................7
Inspect Shipment .........................................................................7
Place Unit in Final Location .........................................................7
Airflow Conversion .......................................................................7
Hood Installation ..........................................................................8
Connect Condensate Drain .........................................................8
Install Ductwork............................................................................8
Make Electrical Connections .......................................................9
Make Gas Connections..............................................................10
Start-up, Adjustments and Checks ...........................................14
Gas Manifold Pressure Measurement and Adjustment.............15
Blower Speed Adjustments........................................................17
Blower Performance Data ..........................................................17
Unit Shutdown............................................................................19
Cooling Start-Up ........................................................................19
SEQUENCE OF OPERATION ......................................................20
Heating System ..........................................................................20
Cooling System ..........................................................................20
Fan Only .....................................................................................21
Cooling Start-Up ........................................................................21
MAINTENANCE ............................................................................22
TROUBLESHOOTING ..................................................................23
Unit Fails to Operate Properly....................................................23
Ignition Control Error Codes ......................................................23
Abnormal Operation—Heating...................................................24
Abnormal Operation—Cooling...................................................25
ASSISTANCE OR SERVICE .........................................................28
Accessories ................................................................................28
WPIO-325C
Whirlpool
®
Home Cooling and Heating
14610 Breakers Drive
Jacksonville, FL 32258
Whirlpool Gold
®
Models
WGGE45
Goodman 1
Hazards or unsafe practices could result in property
damage, product damage, severe personal injury or death.
Hazards or unsafe practices may result in property
damage, product damage, personal injury or death.
WARNING
CAUTION
Placeholder
for
Bar
Code
Goodman 9
Hazards or unsafe practices may result in property
or product damage.
CAUTION