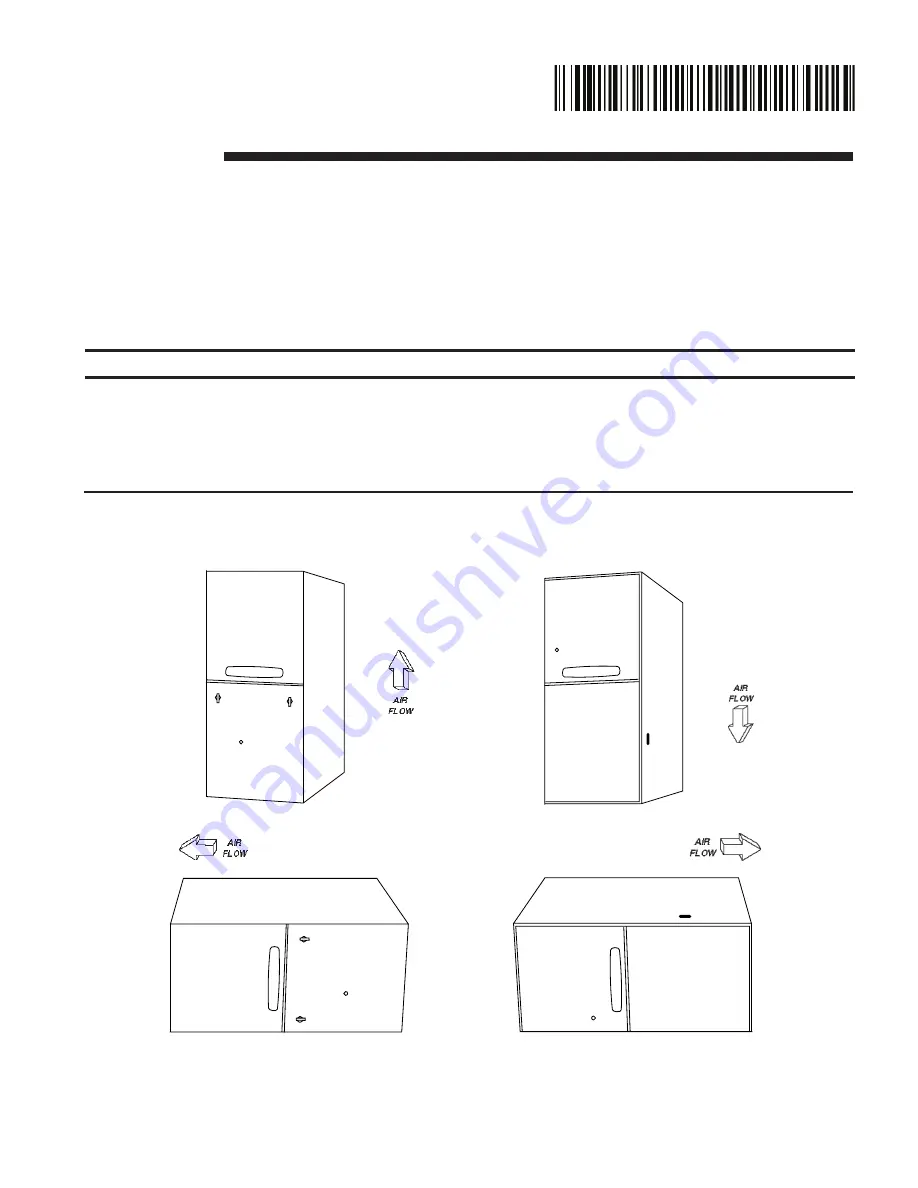
UPFLOW
*UHM
UPFLOW/HORIZONTAL
*DHM
DOWNFLOW
DOWNFLOW/HORIZONTAL
*UHMB060ACV3VB
*UHMB080ACV3VB
*UHMC100ACV4VB
*UHMD120ACV5VB
Upflow/ Horizontal and Downflow/ Horizontal,
Gas-Fired, Direct Vent, Variable Speed Inducer, Modulating
Condensing Communicating furnaces
ALL phases of this installation must comply with NATIONAL, STATE AND LOCAL CODES
IMPORTANT
— This Document is customer property and is to remain with this unit.
Please return to service information pack upon completion of work.
Installer’s Guide
*DHMB060BCV3VB
*DHMB080ACV3VB
*DHMC100ACV4VB
*DHMD120BCV5VB
* First letter may be “A” or “T"
1. Safety signal words are used to designate a degree or level of seriousness associated with a particular hazard.
2. The signal words for safety markings are WARNING, and CAUTION.
3. a. WARNING indicates a potentially hazardous situation which, if not avoided, could result in death or serious injury.
4. b. CAUTION indicates a potentially hazardous situation which, if not avoided, may result in minor or moderate injury. It
is also used to alert against unsafe practices and hazards involving only property damage.
A341624P14
NOTE:
This furnace can be configured for Communicating or 24 VAC modes. Using fully Communicating or 24 VAC
modes, the furnace can support single or multi-stage heat pump, AC, or heating only applications. Combined with
a communicating Comfort Control only, the furnace will support a single stage 24 VAC cooling outdoor unit only.
18-CD30D1-20-EN