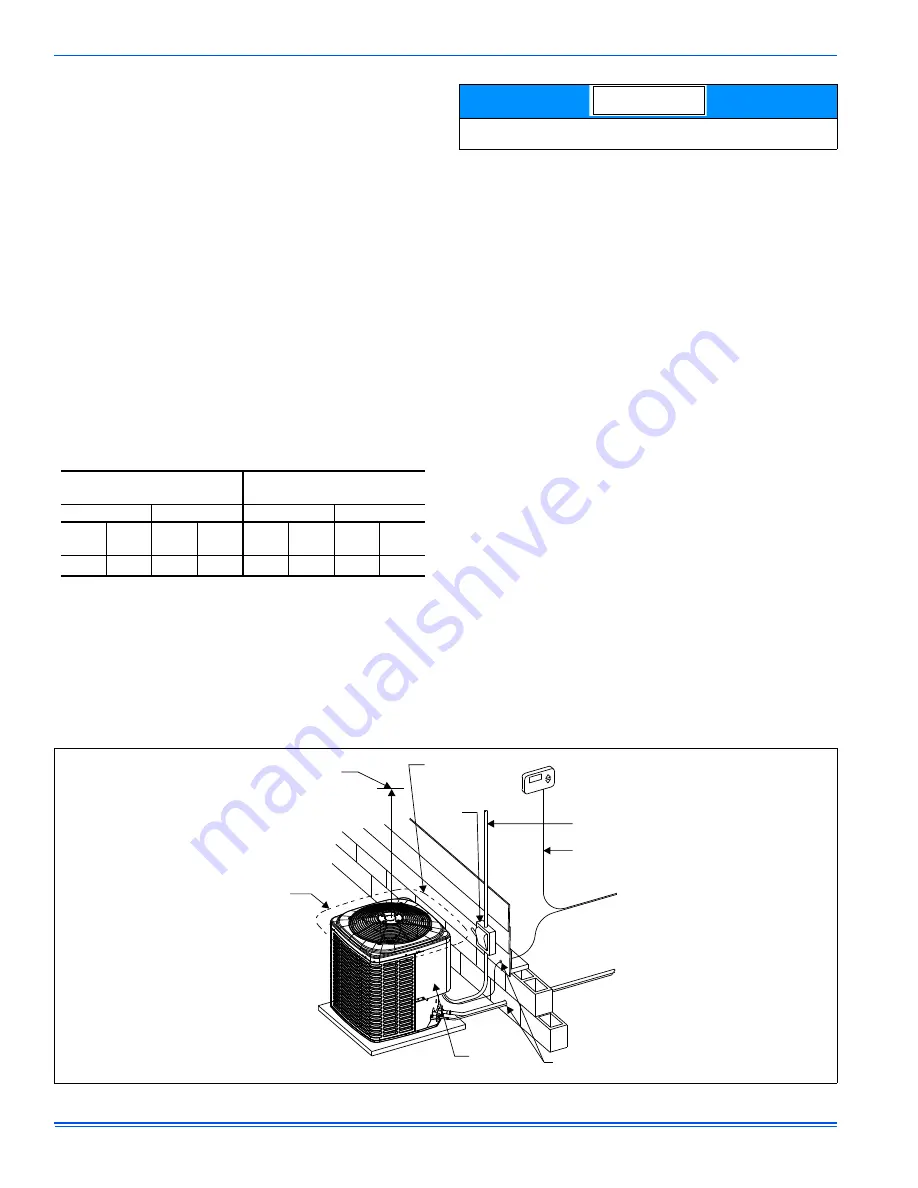
835961-UIM-D-0213
2
Johnson Controls Unitary Products
Requirements For Installing/Servicing R-410A Equipment
•
Gauge sets, hoses, refrigerant containers, and recovery system
must be designed to handle the POE type oils, and the higher
pressures of R-410A.
•
Manifold sets should be 800 psig high side and 250 psig low side
with 550 psig low side restart.
•
All hoses must have a 700 psig service pressure rating.
•
Leak detectors should be designed to detect HFC refrigerant.
•
Recovery equipment (including refrigerant recovery containers)
must be specifically designed to handle R-410A.
•
Do not use an R-22 TXV.
•
A liquid-line filter drier is required on every unit.
LIMITATIONS
The unit should be installed in accordance with all National, State, and
Local Safety Codes and the limitations listed below:
1. Limitations for the indoor unit, coil, and appropriate accessories
must also be observed.
2. The outdoor unit must not be installed with any duct work in the air
stream. The outdoor fan is the propeller type and is not designed to
operate against any additional external static pressure.
3. The maximum and minimum conditions for operation must be
observed to assure a system that will give maximum performance
with minimum service.
4. The maximum allowable line length for this product is 75 feet.
SECTION III: UNIT INSTALLATION
LOCATION
Before starting the installation, select and check the suitability of the
location for both the indoor and outdoor unit. Observe all limitations and
clearance requirements.
The outdoor unit must have sufficient clearance for air entrance to the
condenser coil, for air discharge, and for service access. See Figure 1.
If the unit is to be installed on a hot sun exposed roof or a black-topped
ground area, the unit should be raised sufficiently above the roof or
ground to avoid taking the accumulated layer of hot air into the outdoor
unit.
Provide an adequate structural support.
ADD-ON REPLACEMENT/RETROFIT
When this unit is being used as a replacement for an R-22 unit, it is
required that the outdoor unit, indoor coil, and metering device all be
replaced. The following steps should be performed in order to insure
proper system operation and performance. Line-set change out is also
recommended.
1. Change-out of the indoor coil to an approved R-410A coil/ condens-
ing unit combination with the appropriate metering device.
2. Change-out of the line-set when replacing an R-22 unit with an
R410-A unit is highly recommended to reduce cross-contamination
of oils and refrigerants.
3. If change-out of the line set is not practical, then the following pre-
cautions should be taken.
•
Inspect the line set for kinks, sharp bends, or other restrictions,
and for corrosion.
•
Determine if there are any low spots which might be serving as oil
traps.
•
Flush the line set with a commercially available flush kit to
remove as much of the existing oil and contaminants as possible.
•
Install a suction line filter-drier to trap any remaining contami-
nants, and remove after 50 hours of operation.
4. If the outdoor unit is being replaced due to a compressor burnout,
then installation of a 100% activated alumina suction-line filter drier
in the suction-line is required, in addition to the factory installed liq-
uid-line drier. Operate the system for 10 hours. Monitor the suction
drier pressure drop. If the pressure drop exceeds 3 psig, replace
both the suction-line and liquid-line driers. After a total of 10 hours
run time where the suction-line pressure drop has not exceeded 3
psig, replace the liquid line drier, and remove the suction-line drier.
Never leave a suction-line drier in the system longer than 50 hours
of run time.
AIR TEMPERATURE AT
OUTDOOR COIL, °F
AIR TEMPERATURE AT
INDOOR COIL, °F
Min.
Max.
Min.
Max.
DB
Cool
DB
Heat
DB
Cool
DB
Heat
WB
Cool
DB
Heat
WB
Cool
DB
Heat
50
-10
115
75
57
50
1
1. Operation below this temperature is permissible for a short period of
time, during morning warm-up.
72
80
For multiple unit installations, units must be spaced a minimum of 24
inches apart (coil face to coil face).
NOTICE
FIGURE 1:
Typical Installation with Required Clearances
60” OVERHEAD
CLEARANCE
MINIMUM 18” SERVICE
ACCESS CLEARANCE
ON ONE SIDE
WEATHERPROOF
DISCONNECT
SWITCH
THERMOSTAT
10” CLEARANCE
AROUND PERIMETER
CONTROL
ACCESS
PANEL
TO INDOOR COIL
NEC CLASS 1 WIRING
NEC CLASS 2 WIRING
TO FURNACE OR
AIR HANDLER
TERMINAL BLOCK
SEAL OPENING(S) WITH
PERMAGUM OR EQUIVALENT
NOTES:
ALL OUTDOOR WIRING MUST BE WEATHERPROOF.
MINIMUM 24” UNIT TO UNIT CLEARANCE.