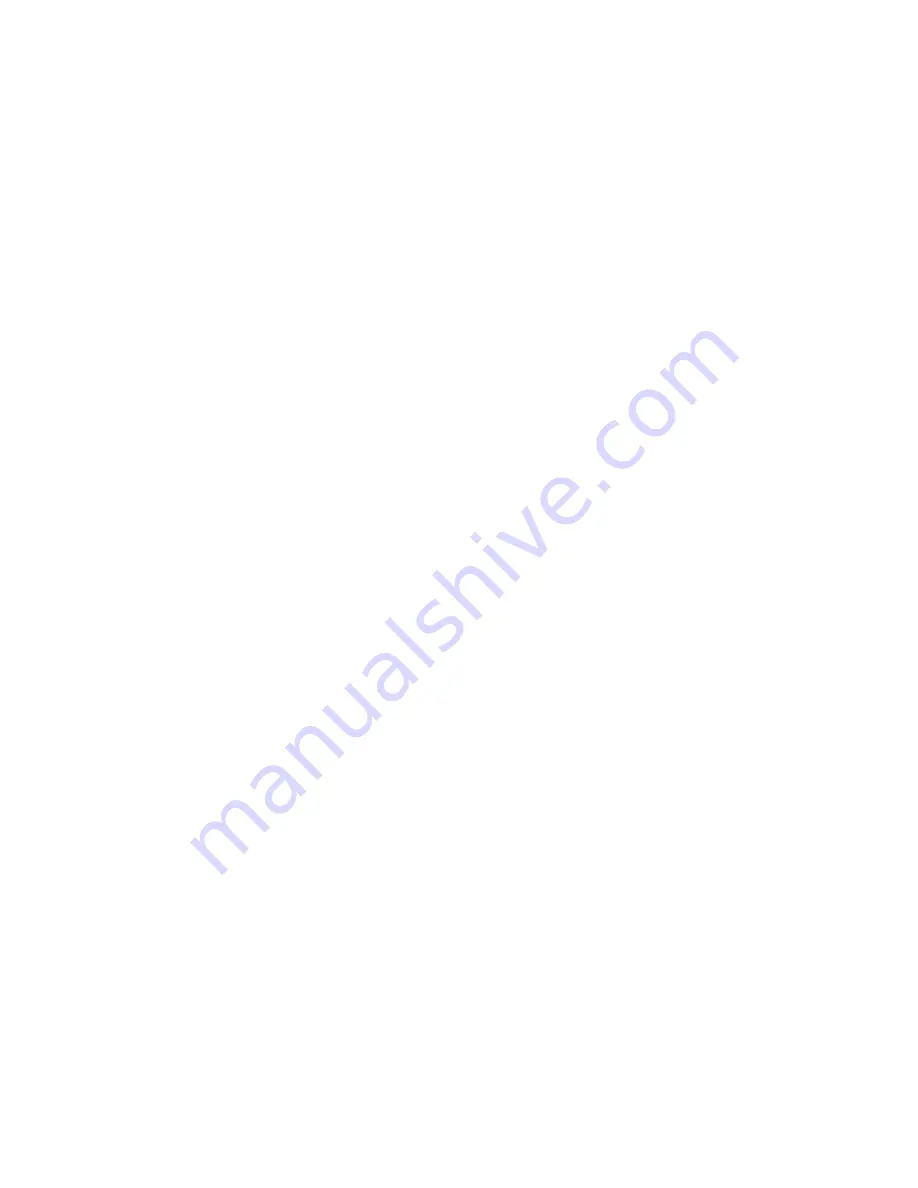
FORM 150.60-NM4
YORK INTERNATIONAL
73
OPERATING SEQUENCE
NOTE: The operating sequence described below relates
to operation after power has been applied on a
hot water start (such as start-up commissioning).
Under these circumstances, loading will deviate
from normal sequence and timing previously de-
scribed. When a compressor starts, internal tim-
ers limit minimum time before another compres-
sor can start to 1 minute. Time between stages
of loading is also limited by internal timers to a
minimum of 1 min., although the micro would
like to load at 30 sec. intervals which may cause
the lag compressor to start before the lead sys-
tem fully loads optional steps. This also devi-
ates from the normal sequence of loading. If
rate control dictates, time between stages of
loading may be up to 150 sec. or may not occur
at all. This will be determined by rate control
programming and actual water temperature rate
of change.
1. For the system compressors to run, all Manual Re-
set Cut-outs must be reset, the Flow Switch must
be closed, any remote cycling contacts must be
closed, the System Switches must be ON, the Daily
Schedule must be scheduling the chiller to run, and
temperature demand must be present.
2. As long as power is applied, the Crankcase Heat-
ers will be on and stay on as long as the compres-
sors are not running.
3. When power is applied to the system, the micro-
processor will start a 2 minute timer. This is the
same timer that prevents an instantaneous start after
a power failure.
4. At the end of the 2 minute timer, the microproces-
sor will check for cooling demand as well as check
to see if any system safeties are exceeded. If all
conditions allow for start, the lead compressor will
start unloaded. Coincident with the start, the
programmable anti-recycle timer will be set and
begin counting downward to 0. The liquid line so-
lenoid valve will open when the system is pumped
down to the suction pressure cut-out (Pumpdown
on start-up).
5.
After 4 seconds of run time,
the motor current of
the lead compressor must be >14% FLA and <115%
FLA. Oil pressure must be 5 PSID or greater. If these
conditions are not met, the lead compressor will
shut down.
6.
After 30 seconds of run time,
the oil pressure of
the lead compressor must be a minimum of 20 PSID
and the suction pressure must be a minimum of
50% of cut-out.
7.
After 60 sec of run time,
if cooling demand re-
quires and no safeties have been exceeded, the
lead compressor will load, if cooling demand (tem-
perature and rate control) requires.
8.
After 90 seconds of run time,
if cooling demand
requires and no safeties have been exceeded the
lag compressor will start unloaded. Coincident with
the start, the programmable anti-recycle counter will
be set and begin counting downward to 0. The
liquid line solenoid will open when the system is
pumped down to the suction pressure cut-out.
9.
After 94 seconds of run time,
the oil pressure of
the lag compressor must be a minimum of 5 PSID
and suction pressure must be greater than 50% of
cut-out.
10.
After 2 minutes of run time,
the lead compressor
will continue to load, if cooling demand (tempera-
ture and rate control) requires and extra steps of
capacity are present. The oil pressure of the lag
compressor must be a minimum of 20 PSID and
the suction pressure must be a minimum of 50%
cut-out.
11.
After 2 minutes and 30 seconds of run time,
the
lag compressor will load, if cooling demand (tem-
perature and rate control) requires.
12.
After 3 minutes of run time,
the lead compressor
will load, if cooling demand (temperature and rate
control) requires, and extra steps of capacity are
present.
13.
After 3 minutes and 30 seconds of run time,
the
lag compressor will load, if optional stages of load-
ing are present and cooling demand requires.
14.
After 4 minutes of run time,
the lead compressors
suction pressure must be greater than the pro-
grammed cut-out. In addition, the oil pressure of
the lead compressor must be greater than 25 PSID.
15.
After 4 minutes and 30 seconds of run time,
the
lag compressor will load, if optional stages of load-
ing are present and cooling demand requires.
16.
After 5 minutes and 30 seconds of run time,
the
lag compressors suction pressure must be greater
than the programmed cut-out. In addition, the oil
pressure of the lead compressor must be greater
than 25 PSID.
17. Operation beyond 6 minutes will be dictated by cool-
ing demand. Anti-recycle timers will time out and
system safety thresholds will continue to be moni-
tored.