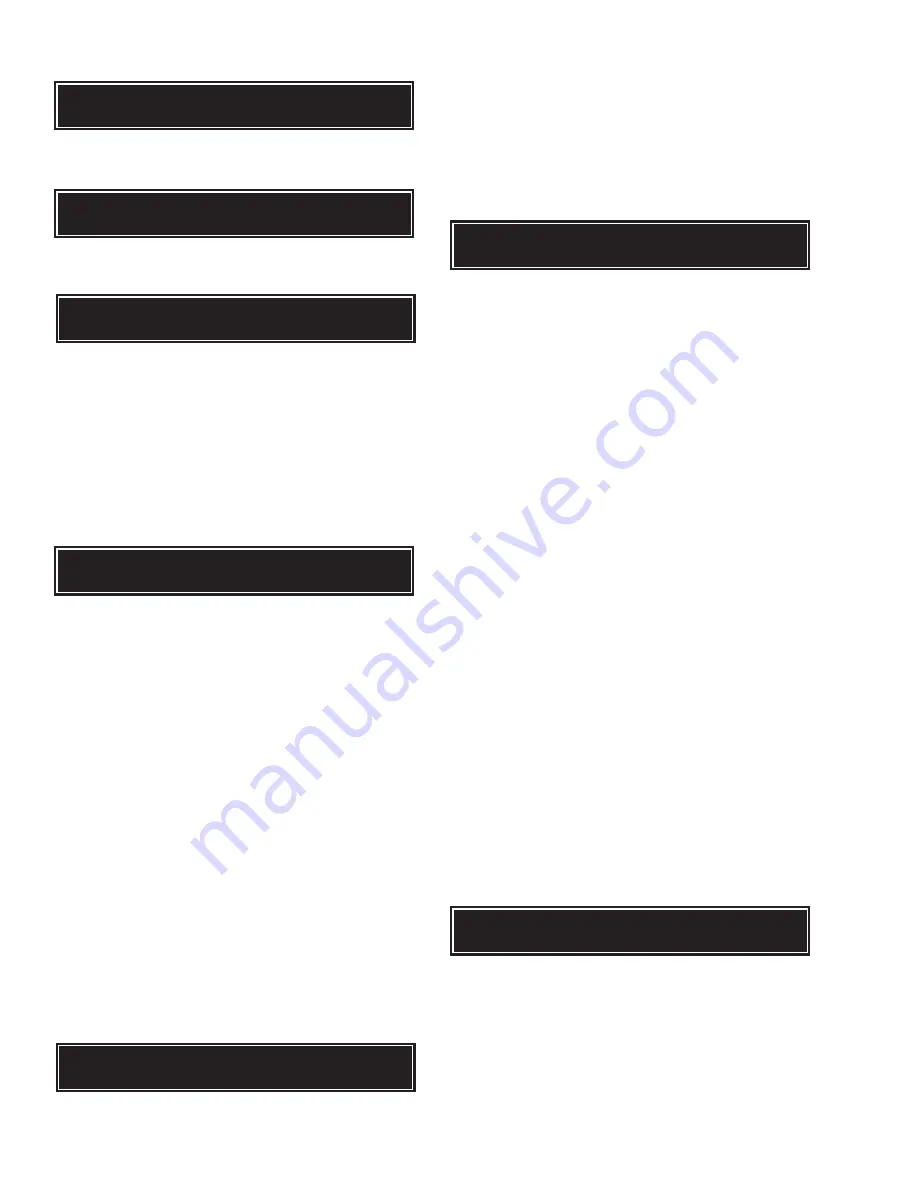
84
YORK INTERNATIONAL
The COMP RUNNING message indicates that the
respective compressor is running due to demand.
The anti-recycle timer message shows the amount of
time left on the respective anti-recycle timer.
The anti-coincident timer is a software feature that guards
against 2 compressors starting simultaneously. This
assures instantaneous starting current does not become
excessively high due to simultaneous starts. The micro
limits the time between compressor starts to 1 minute
regardless of demand and anti-recycle timers that are
timed out. The time shown on the anti-coincident timer is
the time left on the timer before the respective system will
start. It will only appear when the anti-recycle timer has
timed out.
The Motor Current Limiting message indicates a system
is being unloaded by the micro even though demand
requires loading. Used as a safety, this feature assures
that motor current does not become excessively high
causing compressor shutdown. The safety will activate
when the user programmed threshold is exceeded,
providing as much capacity as possible up to the limit
programmed. Additional loading will take place when
motor current drops below the threshold. In most
circumstances, this safety will never activate if current
limiting is programmed for 100% -115%. However, in
extremely high ambients, high chilled liquid temperature,
and situations where the condenser becomes dirty, the
protection provided by this safety will assure that
compressor shutdown does not result in total cooling loss
by limiting loading until the usually short term situation
causing the problem clears.
This message also indicates unloading due to current
limiting where the user has the programmed unload point
set below 100% to utilize the programmable unload for
“demand limiting”. Resetting of current limit unloading
may be done through the “PROGRAM” mode on the
Control Panel.
Discharge Pressure Limiting takes affect when discharge
pressure nears the point at which the high pressure cut-
out will shut the system down causing total loss of
cooling. When this message appears, discharge pressure
has exceeded the “user” programmable threshold and the
micro is unloading the affected system to prevent
shutdown on a manual high pressure cut-out. Reloading
will take place when discharge pressure has dropped 60
PSIG below the threshold.
The Suction Temperature Limiting Message indicates
that the microprocessor is in the water temperature
control mode and is sensing that the saturated suction
temperature has dropped to a point (29°F) where further
temperature reduction could cause some icing of the
tudes. This control will not operate in the brine mode since
icing of the tubes is not a problem if proper bine
concentration is maintained. This saturated suction
temperature is conputed by the micro by converting
suction pressure to temperature.
When the micro senses that saturated suction temp-
erature has dropped below 29°F, the micro will inhibit
loading for the first 3 minutes during which the condition
occurs to allow time fo the temperature to rise. If the
condition persists for more than 3 min., the micro will set
a 5 minute timer. During this 5 minute period, it will take
action to cause the saturated suction temperature to rise
above 31°F. As this 5 minute timer counts down to zero,
the micro will pulse the slide valve to unload every 5
seconds as long as the temperature is below 31°F. If the
temperature rises above 31°F, the micro will inhibit
loading for the remainder of the 5 minute period.
If after the 5 minute period the saturated suction
temperature is above 29°F, the micro will allow the
compressor to load to assure that the leaving chilled water
requirements are satisfied. Otherwise, the micro will reset
the 5 minute timer and start the process over again.
To assure that leaving chilled water requirements are
satisfied while one compressor is under suction temp
limiting control, the micro will start or load the other
compressor as necessary.
This message indicates the current limiting is in effect
through the Current Limit PWM input on Terminals 13 and
16 of the Microprocessor Board. As long as this input is
activated, the micro will not allow loading beyond the
PWM % that has been sent to the microprocessor through
the PWM input. Generally, this input is used for purposes
of demand limit. Details of the use of this feature are
outlined on page 130.
S Y S
1
C O M P
R U N N I N G
S Y S
2
C O M P
R U N N I N G
S Y S
1
D S C H
L I M I T I N G
S Y S
2
D S C H
L I M I T I N G
S Y S
1
A R
T I M E R
X X X
S
S Y S
2
A R
T I M E R
X X X
S
S Y S
1
A C
T I M E R
X X
S
S Y S
2
A C
T I M E R
X X
S
S Y S
1
C R N T
L I M I T I N G
S Y S
2
C R N T
L I M I T I N G
S Y S
1
S T E M P
L I M I T I N G
S Y S
2
S T E M P
L I M I T I N G
S Y S
1
E M S
L I M I T I N G
S Y S
2
E M S
L I M I T I N G
Summary of Contents for Millennium YCAS 316
Page 11: ...FORM 201 10 NM1 11 YORK INTERNATIONAL YCAS 140 246 DIMENSIONS English LD01444 LD01446...
Page 13: ...FORM 201 10 NM1 13 YORK INTERNATIONAL YCAS 140 246 DIMENSIONS SI LD01440 LD01442...
Page 15: ...FORM 201 10 NM1 15 YORK INTERNATIONAL YCAS 216X 266X DIMENSIONS English LD01454 LD01454...
Page 17: ...FORM 201 10 NM1 17 YORK INTERNATIONAL YCAS 216X 266X DIMENSIONS SI LD01450 LD01448...
Page 33: ...FORM 201 10 NM1 33 YORK INTERNATIONAL 28514A FILTER DRYER LIQUID STOP VALVE...
Page 37: ...FORM 201 10 NM1 37 YORK INTERNATIONAL LD01285 FIG 3 SCREW CHILLER REFIGERANT FLOW DIAGRAM...
Page 59: ...FORM 201 10 NM1 59 YORK INTERNATIONAL FIG 11 CONTINUED LD01465 D...
Page 61: ...FORM 201 10 NM1 61 YORK INTERNATIONAL FIG 12 CONTINUED LD01458 D...
Page 69: ...FORM 201 10 NM1 69 YORK INTERNATIONAL FIG 16 CONTINUED LD01206 D...
Page 71: ...FORM 201 10 NM1 71 YORK INTERNATIONAL FIG 17 CONTINUED LD01202 D...